Special Feature Environment-Friendly Polyurethane Resins for Use in Artificial and Synthetic Leathers
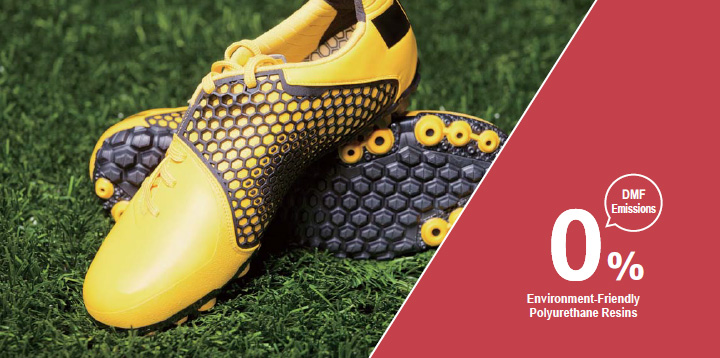
Providing Materials that Facilitate Safe and Secure Production and Use
Value Creation Promoting environment-friendly polymers worldwide
With the rapid tightening of environmental regulations in global markets, including the PRC, a shift in demand from solvent-based to water-based and solvent-free products poses a considerable challenge for manufacturers of polyurethane resins. In the polymers business, the DIC Group is advancing the swift development of environment-friendly products that respond to pertinent laws and regulations and promoting sales of environment-friendly polymers worldwide. DIC is actively expanding its polymers business in the PRC, taking a multifaceted approach that includes growing markets for products exported from Japan and produced in Taiwan and using Group sites in the PRC to further business development. As a natural extension, the Group is also looking to expand its environment-friendly polymers business beyond the PRC. In addition, DIC is exploring the idea of collaborating with the Sun Chemical Group—a DIC Group member—to encourage a broader market presence in the Americas and Europe, where environmental concerns have long been at the forefront. Looking ahead, the DIC Group will take decisive steps to invest strategically and work in collaboration with other companies to reinforce the foundation of the business, positioning it to expand sales of environment-friendly products by ensuring an accurate and timely grasp of changing market needs.
Value Creation Contributing to the manufacture of products with a lower environmental impact
Polyurethane resins, in which molecular design technologies are leveraged to impart unique performance properties, are used in compounds for a wide range of applications, from clothing and various everyday commodities to building materials and materials for automobiles, electronics and various industrial uses. Of note, annual global production of polyurethane resins for use as raw materials and adhesives for artificial and synthetic leathers amounts to 240,000 metric tonnes, making this the Group’s second-largest product group in terms of output after polyurethane foam (used in polyurethane sheets and insulating materials). Bolstered by outstanding performance features and a shift in preference from natural to artificial and synthetic leathers, demand for polyurethane resins continues to increase.
The process used to manufacture polyurethane resins for artificial and synthetic leathers uses the organic solvent dimethylformamide (DMF). VOCs emitted during this process and the health consequences of DMF residue in artificial and synthetic leathers are thus major concerns. For this reason, DMF is likely to be added to the European Union’s Registration, Evaluation, Authorisation and Restriction of Chemicals (REACH) list of banned substances. Many global sportswear manufacturers around the world have declared their intention to discontinue use of DMF by 2020. Moreover, restrictions on VOC emissions resulting from the use of solvents have been strengthened in both the PRC and Taiwan, both major supply bases for athletic shoes.
The DIC Group, which develops and manufactures a diverse range of solventborne and waterborne polyurethane resins, took prompt steps to address these and other challenges related to the use of DMF in artificial and synthetic leathers and has succeeded in developing and marketing DMF-free environment-friendly polyurethane resins with properties identical to their conventional counterparts. The Group is currently establishing a framework for providing total solutions, including raw materials and production systems, to manufacturers of athletic shoes.
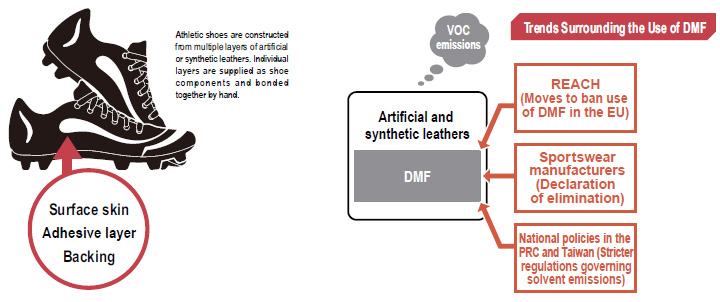
A Distinctively
DIC Response
Combining core technologies to establish technologies for the production of environment-friendly polyurethane resins




Artificial and synthetic leathers used in athletic shoes must deliver an appropriate texture (soft to touch and sufficiently strong), flex resistance at room temperature and low temperatures, durability and a light weight. Ensuring competitive production costs is also a key concern. With conventional solventborne polyurethane resin, the vaporization of solvent facilitates the formation of a strong surface skin, resulting in a product that satisfies performance requirements. In contrast, the use of waterborne resins hinders the achievement of a high molecular weight and even grain, making it difficult to realize sufficient strength, durability and scuff resistance.
By combining multiple key core technologies—including polymer design technologies used in HYDRAN waterborne adhesive polyurethane resins, moisture-curing technologies used in TYFORCE solvent-free hot-melt adhesives, and foam expansion and reactivity control used in PANDEX thermosetting polyurethane resins—DIC has succeeded in creating an environment-friendly polyurethane resin production system that yields solvent-free, i.e., DMF-free, polyurethane resins comparable in quality to conventional solventborne products, as well as shortens process times, thereby reducing energy consumption and production costs.
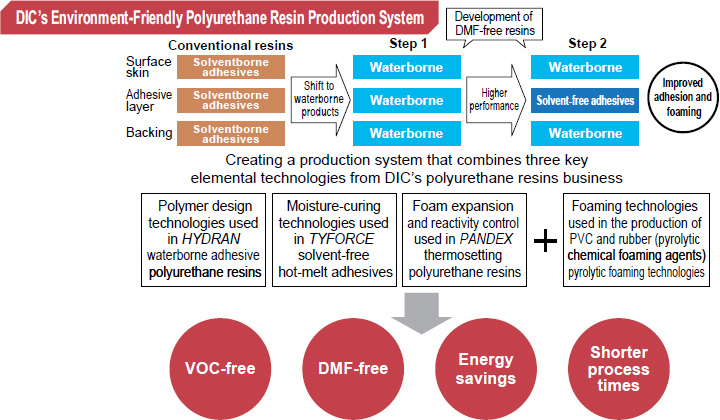
Providing a total production system that extends to processing rather than simply supplying materials
An environment-friendly polyurethane resin production system requires processing technologies, as well as molecular design technologies used in the production of resin. Accordingly, DIC collaborated with equipment manufacturers to develop production processes optimized to suit product properties and in fiscal year 2016 completed a system, which it will provide to customers together with materials. To ensure swift delivery to the PRC production bases of global athletic shoes manufacturers, the system will be supplied through Taiwan-based Group company Lidye Chemical Co., Ltd. DIC will endeavor to establish this system, which facilitates local procurement of both resin and equipment, as an environment-friendly global standard across a wide range of industries. Of particular note, DIC’s new total production system responds to the environmental requirements of automakers for materials used in vehicle interiors. Accordingly, DIC will continue working to improve the texture and durability (resistance to damage from wear, sebaceous matter, chemicals, heat, light and moisture) of artificial and synthetic leathers produced using the system, as well as to promote the system’s appeal in the market.
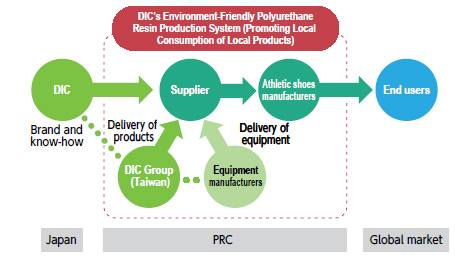
KEY PERSON of DIC
Recognizing tighter regulations as a business opportunity, we are working to define a new global standard for environment-friendly polyurethane resins.
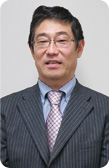
The passing of increasingly stringent VOC emissions regulations worldwide is testing the technological capabilities of chemicals companies. We recognize this trend as a golden opportunity to leverage our comprehensive strengths to expand our business.
Success in the polyurethane resins business today demands more than the ability to provide materials. With consideration for the environment our guiding objective, we believe it is possible for us to define a new global standard by providing entire plants: in other words, comprehensive solutions. This distinctive business strategy is made possible by the DIC Group’s thorough grasp of all the technologies involved, from polymer design through to production, as well as its global network of production facilities.
General Manager, Osaka Urethanes Sales Dept., Polymers Product Division Masahiro Nishi
We must also devote considerable effort to research in the areas of design development and processing methods.

DIC is the top manufacturer of solventborne polyurethane resins in Japan. The Company also boasts a wealth of development and production technologies in a diverse range of other areas, from epoxy, phenolic, acrylic and other resins to pigments. Combining compounding and other core technologies makes it possible to create new performance properties. In line with the goal of providing total solutions, that is, solutions that extend as far as processing, the people in my laboratory are involved not only in flask synthesis but also in equipment development. For this reason, we strive to always keep abreast of the latest information and technological trends.
Group Manager, Polymer Technical Group 6, Polymer Technical Div. 2 Tamotsu Sakamoto
Related Link
2017 Special Feature
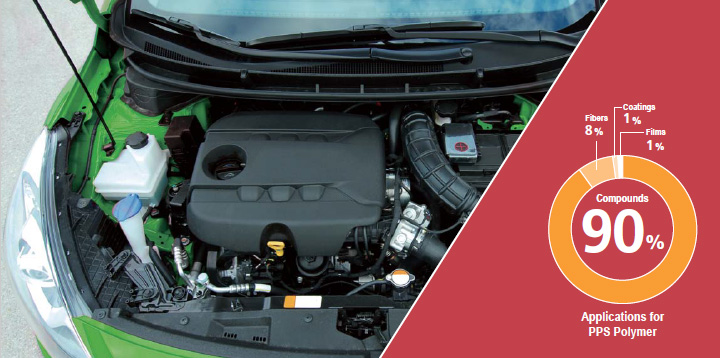
Super Engineering Plastics
Helping to Reduce Vehicle Weight, Improve Fuel Efficiency and Lower CO₂ Emissions
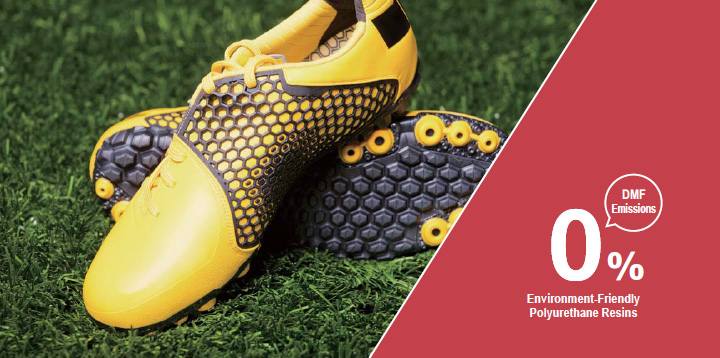
Environment-Friendly Polyurethane Resins for Use in Artificial and Synthetic Leathers
Providing Materials that Facilitate Safe and Secure Production and Use
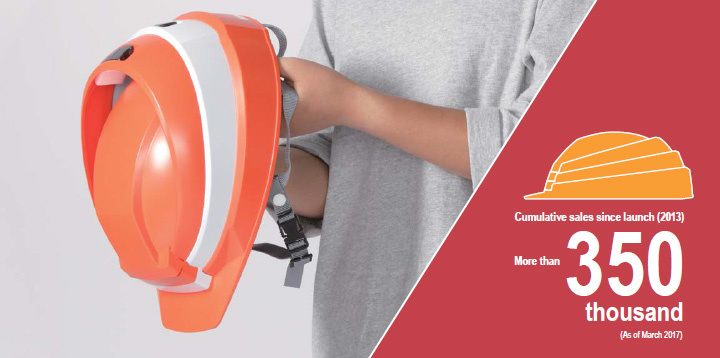
IZANO Folding Emergency Helmets
Delivering Easy Storability and Portability, IZANO Helmets Help Prevent and Mitigate Injuries in Disaster Situations
TOPICS
Helping Improve Food Packaging to Extend Product Shelf Life
Sun Chemical Promotes Initiatives Aimed at Addressing an Important Social Imperative