Occupational Safety and Health/Disaster Prevention
- Goals and Achievements of Major Initiatives
- Occupational Safety and Health
Basic Approach - Framework for Promotion
- Principal Initiatives in Fiscal Year 2023
- Infrastructure for Preventing Occupational Accidents
- Hands-On Safety Training
- Efforts to Foster a Safety-Conscious Corporate Culture
- Disaster Prevention
Basic Approach - Framework for Promotion
- Principal Initiatives in Fiscal Year 2023
- Environmental Protection
Basic Approach - Groupwide Environmental Performance
Goals and Achievements of Major Initiatives
Ensure occupational safety and health.
Scope of target | Global |
---|---|
Goals for fiscal year 2023 | Reduce TRIR. Targets: DIC Group in Japan: 2.10 PRC: 1.00 Asia–Pacific region: 1.00 Sun Chemical Group: 8.00 (Global DIC Group: 4.65) |
Achievements in fiscal year 2023 | DIC Group in Japan: 2.09 PRC: 2.06 Asia–Pacific region: 1.11 Sun Chemical Group: 4.53 (Global DIC Group: 3.00) |
Evaluation | ★★ |
Goals for fiscal year 2024 | Reduce TRIR. Targets: DIC Group in Japan: 1.90 PRC: 1.00 Asia–Pacific region: 1.00 Sun Chemical Group: 8.00 (Global DIC Group: 4.47) |
Prevent disasters.
Scope of target | Global |
---|---|
Goals for fiscal year 2023 | Maintain 0 major accidents. Achieve process safety accident frequency rate of 0.110 (maintain at fiscal year 2022 level). |
Achievements in fiscal year 2023 | Process safety accident frequency rate: 0.124 |
Evaluation | ★ |
Goals for fiscal year 2024 | Maintain 0 major accidents. Achieve process safety accident frequency rate of 0.110 (maintain at fiscal year 2023 level). |
- Note: TRIR is calculated as (Number of casualties due to occupational accidents resulting in workdays lost + Number of casualties due to occupational accidents not resulting in workdays lost) / Million work hours.
- Evaluations are based on self-evaluations of current progress.
Key: ★★★ = Excellent; ★★ = Satisfactory; ★ = Still needs work
Policies
Basic Approach
Viewing the prioritization of operational safety as a core management tenet, the DIC Group works tirelessly to prevent occupational accidents and disasters, as well as to bolster occupational health and safety levels.
The DIC Group recognizes operational safety both as fundamental to its businesses and the core component of Responsible Care. The Group thus promotes active occupational safety and health, security and disaster prevention measures to foster a “Safety First” philosophy Groupwide and on the part of every employee. Because its operations span diverse fields, the Group has numerous processes that use hazardous and toxic materials, as well as rotating devices, not all of which involve chemical reactions. Any accident using such materials or devices has the potential to significantly impact society in general and damage the health of Group and/or partner company employees and local residents. With the aim of preventing such accidents, the Group encourages individual Group companies to earn the International Organization for Standardization’s Occupational Safety and Health Management System (OSHMS) certification and, based on the results of stringent risk assessments, prioritizes reducing risks in the workplace by promoting adherence to Principles of Safe Conduct and training highly perceptive safety personnel. The Group also strives to enhance safety through efforts to reinforce its safety infrastructure and create a safetyoriented corporate culture.
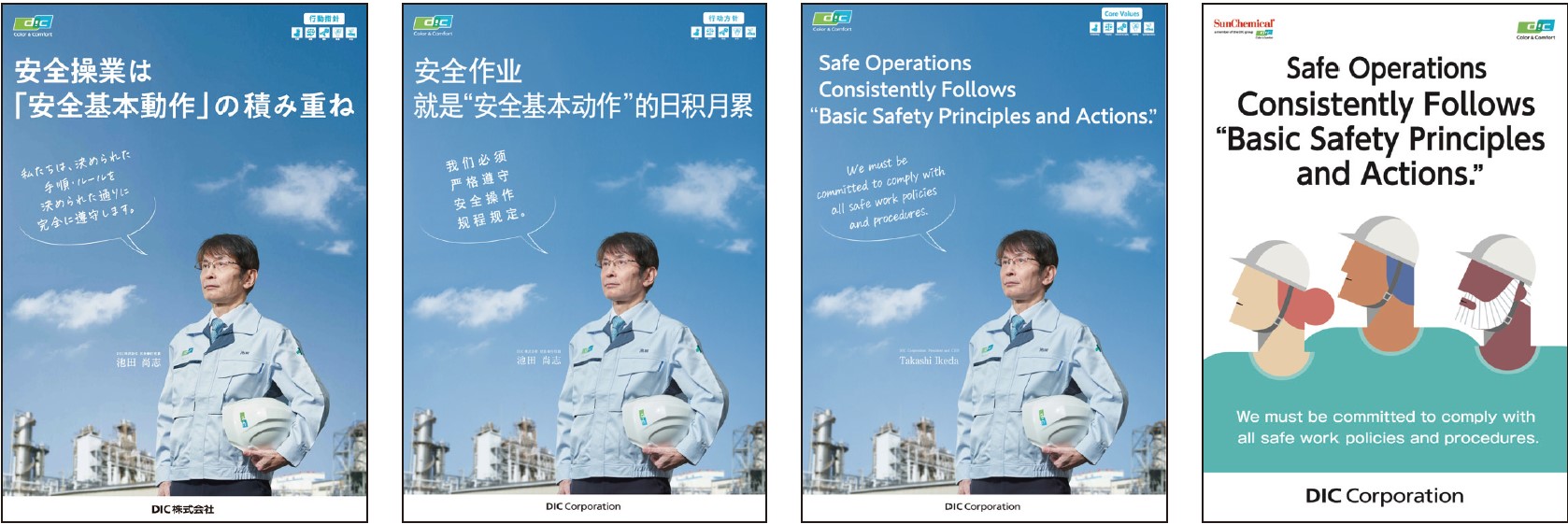
Framework for Promotion
Under the supervision of the Sustainability Committee chair (DIC’s president and CEO), the Responsible Care Department promotes a variety of occupational safety and health initiatives in collaboration with sites via individual regional headquarters. In Japan, the Responsible Care Department meets regularly with site ESH officers to confirm the status of priority issues and the achievement of targets, as well as to manage the progress of related efforts. Elsewhere, the Responsible Care Department and individual regional headquarters work together to set regional targets, while site ESH officers conduct site risk assessments, analyze accidents and promote remedial measures to ensure the continuous improvement of occupational safety and health overseas. (For more information, please see “Policies, Targets and Framework.”)
Principal Initiatives in Fiscal Year 2023
1. Global DIC Group
The DIC Group sets regional targets and promotes a variety of initiatives around the world with the aim of eliminating occupational accidents. Occupational accident frequency rate—the frequency of occupational accidents resulting in workdays lost—is generally used as an indicator. This is calculated as the number of fatalities or injuries due to occupational accidents per million work hours. DIC Group companies in Japan, Greater China and the Asia–Pacific region, as well as Sun Chemical, use total recordable incident rate (TRIR), an even more stringent indicator. TRIR is calculated as the number of casualties (fatalities and injuries) due to occupational accidents, both those resulting in workdays lost and those not resulting in workdays lost, per million work hours. The number of employees used to calculate TRIR is the number of direct, regular, temporary and part-time employees. Employees of on-site and outside contractors are not included.
In fiscal year 2023, the TRIR for the global DIC Group was 3.00, below its 4.65 goal. None of the occupational accidents at global Group sites resulted in fatalities. A total of 76 injuries resulting in workdays lost were reported, while injuries not resulting in workdays lost numbered 56. Looking ahead, the Group will continue working to reduce occupational accidents by promoting the sharing of information on accidents and disasters, conducting risk assessments, promoting adherence to Principles of Safe Conduct, analyzing the causes of accidents and formulating countermeasures, and providing occupational safety and health–related education and training. Some of these efforts are described in this report.
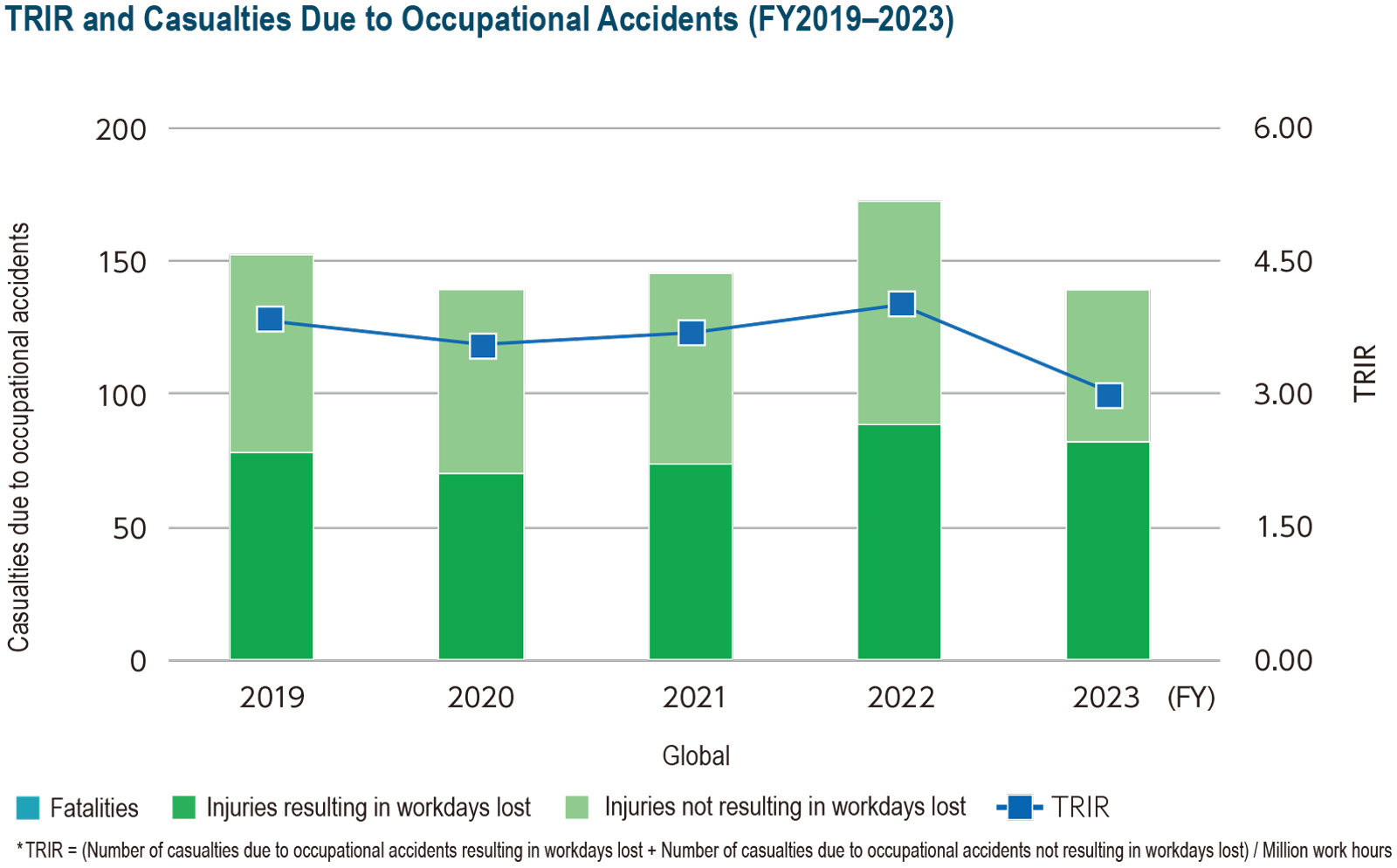
2. DIC Group in Japan
In fiscal year 2023, the DIC Group in Japan achieved a TRIR of 2.09, better than its target of 2.10 and an improvement from 2.23 in the previous fiscal year. No occupational accidents resulting in fatalities were reported. There were nine injuries resulting in workdays lost and 10 injuries not resulting in workdays lost. These numbers are broken down in the table to the right.
DIC Group (Japan)
Casualties | Illness/ill health | Total | |
---|---|---|---|
Fatalities | 0 | 0 | 0 |
Injuries resulting in workdays lost | 9 | 0 | 9 |
Injuries not resulting in workdays lost | 9 | 1 | 10 |
Total | 18 | 1 | 19 |
3. DIC Group in Other Countries and Territories
The TRIR for the Sun Chemical Group was 4.53, significantly better than the target of 8.00. Both the PRC and the Asia–Pacific region fell short of their 1.00 targets, reporting a TRIR of 2.06 and 1.11, respectively. No occupational accidents resulting in fatalities were reported. There were 66 injuries due to occupational accidents resulting in workdays lost and 46 injuries due to occupational accidents not resulting in workdays lost. (For more information, please see “Key Data.”)
TOPICS
DIC Plastics’ Saitama Plant Wins Prize for Excellence in Safety in the JCIA Safety Awards
On May 31, 2023, DIC Plastic, Inc.’s Saitama Plant received a prize for excellence in safety in the JCIA Safety Awards, which were presented in a ceremony at the Palace Hotel in Tokyo. These awards are given to establishments judged to serve as role models for the voluntary promotion of occupational safety and health in the chemicals industry. Winners in fiscal year 2023, the 47th time these awards have been given out, were chosen based on their performance up to December 31, 2022, with four establishments earning recognition. In selecting DIC Plastics’ Saitama Plant, the JCIA cited the facility’s dedication to building a safety-conscious corporate culture, as a result of which as of the end of 2022 it had achieved 16 years and nine months of accident-free operations. The DIC Group will continue to place a high priority on occupational safety and health going forward.
Infrastructure for Preventing Occupational Accidents
1. Monthly Occupational Safety and Health Data
The DIC Group conducts its diverse businesses in accordance with a wide range of national and regional legal systems, working conditions and practices. However, to raise the level of occupational safety and health of the entire Group, it is crucial to establish common standards and benchmarks and to align regional initiatives. The DIC Group promotes the sharing of information related to occupational safety and health across the global Group by aggregating regional statistical data on a monthly basis. Specifically, local data is gathered by DIC (China) for Greater China, DIC Asia Pacific for the Asia–Pacific region, and Sun Chemical for the Americas and Europe. This data is then collated and analyzed by the Responsible Care Department. This makes it possible for each Group company to objectively compare and evaluate their own operational safety, which assists in the establishment of precise targets for individual countries and regions, and the formulation of programs for making improvements. In fiscal year 2019, the Group introduced the cloud-based DIC ESH Data Collection System (DECS) in Japan, Greater China and the Asia–Pacific region to improve the efficiency of data collection. (For more information, please see “Key Data.”)
- Number of employees
- Number of casualties due to occupational accidents resulting in workdays lost and not resulting in workdays lost
- Number of workdays lost
- TRIR
- Total work hours
- Number of accidents involving fires/explosions
- Occupational accident frequency rate
Statistical Occupational Safety and Health Data
2. Analyzing Accidents and Disasters and Providing Information in a Timely Manner
In the event of an accident or disaster at a DIC Group site, the site in question and the corporate headquarters’ department in charge of safety work together to analyze the causes thereof and implement appropriate countermeasures. The department in charge of safety and site Safety and Environment groups hold regular meetings to dig deeper into the causes of accidents and debate the effectiveness of countermeasures. Findings are deployed horizontally to Group sites and companies with the aim of preventing recurrence, as well as shared with DIC Group companies worldwide. DIC has compiled such information to create Accident Case Studies and Occupational Accident Case Study databases, which are used in safety education for Group companies in Japan.
3. Principles of Safe Conduct
Using resources such as case studies of accidents and disasters in the past, DIC has created rules and codes of conduct to ensure operational safety for DIC Group compa nies in Japan, the PRC and the Asia–Pacific region, which it has published as a guidebook titled Principles of Safe Conduct. The fifth edition of this guidebook was published in fiscal year 2019 in Japanese, English and Chinese.
4. Conducting Risk Assessments
The DIC Group identifies potential risks to occupational safety and health and implements initiatives to prevent accidents and occupational injuries. In Japan, the Group is working to further reduce risks posed by chemical substances by revamping its risk assessment procedures and lowering the impact of such substances on the health of employees. Of particular note, in fiscal year 2023 DIC updated its risk assessment guidelines, including those for assessment procedures. After providing pertinent training on the revised guidelines’ administration to management-level employees at domestic DIC Group plants, DIC evaluates hazards associated with and the toxicity of chemicals set forth in Japan’s Poisonous and Deleterious Substances Control Act and considers measures to lower related risks, such as revising handling methods and upgrading facilities.
5. Promoting E-Learning–Based Safety and ESH Training at Production Facilities
To enhance its capabilities in the area of occupational safety and health, and in disaster prevention, the DIC Group recognizes the importance of ensuring that all of its employees gain a broad understanding of chemical substances, production processes, and pertinent laws and regulations. In fiscal year 2016, the Group introduced an e-learning program in Japan. Initially structured around laws and regulations pertinent to the operational safety of production facilities, including Japan’s Fire Service Act, Air Pollution Control Law and High Pressure Gas Safety Act, the e-learning program’s focus was later expanded to include non-regulatory components such as static electricity, with the appropriateness of the program’s training materials verified from the perspective of Responsible Care Department specialists, site ESH officers and production departments. Employees are able to take up to 16 classes. Competence is confirmed through testing. Since fiscal year 2022, the Group has deployed an online occupational safety and health education service from Tokyo-based LaKeel, Inc., that centers on the distribution of short films on the subject.
6. Accident and Disaster Calendar
Since fiscal year 2022, the DIC Group has compiled information on past accidents and disasters into case studies in the form of a monthly calendar that is visible to all employees on the first page of the DIC Group portal site. Information posted includes date of occurrence, site, type of event (e.g., heatstroke, chemical injury or other) and impact (i.e., resulted in workdays lost or did not result in workdays lost). This allows users to identify incidents of concern to them and view detailed data summarizing conditions surrounding occurrence and the effectiveness of countermeasures. Displaying data for all accidents and disasters on a monthly basis also sheds light on trends. Employees looking at the calendar on any given day are able to learn about an accident or disaster that occurred on that day in the past, bolstering awareness of safety and disaster prevention across the Group.
TOPICS
Health and Safety Project Is Planned to Ensure the Health and Safety of Employees
Since fiscal year 2022, DIC’s Gunma Plant has promoted a program designed to advance the health of plant employees. Previously focused on fall prevention, in fiscal year 2023 the program emphasized employee health under the designation “Health and Safety Project.” Project groups worked together to implement three initiatives under the direction of the project leader.
The first initiative was to use the app Shisei Karte (“Posture Chart”), which involves using an iPhone to take photographs of a person performing six poses, which are then analyzed using AI and scored for factors such as posture distortion, to produce a 3D avatar that shows how the person’s posture can be expected to look in the future. These were then developed into a program encompassing diagnostics and care to help individuals improve posture-related issues, which was presented in a series of YouTube videos. The second initiative was to work with the company that operates the plant’s employee cafeteria, Wakana Co., Ltd., to plan a series of easy-to-prepare healthy microwavable meals. During the year, recipes and preparation videos for a total of six dishes were created and displayed via digital signage and on the Gunma Plant’s dedicated website. The third involved inviting Shinichiro Okada, a licensed nursing care worker and physical therapist who is an advocate of nursing care that deploys classical martial arts, to give a lecture on avoiding lower back strain when moving one’s body and an on-site demonstration of how to safely lift an 18-liter square can. Going forward, the DIC Group will continue to plan programs that improve employee health.
DIC Graphics’ Gunma and Tokyo Plants Conduct Fall Prevention Training
DIC Graphics’ Gunma Plant, in collaboration with several affiliated and associated companies, launched the Fall Prevention Project, which held four sessions in fiscal year 2022. The first session, a fall prevention seminar, featured a physiotherapist who introduced exercises to relieve lower back pain that can be done while lying down or sitting. This was followed by a seminar focusing on risk assessment self-checks (physical fitness checks) and gauging awareness levels. Individuals displaying a significant gap between physical fitness and awareness were judged as being at particular risk of falls and were urged to exercise caution. Third was a presentation by a nutritionist on dietary changes that can help prevent locomotive syndrome, a condition involving decreased mobility due to disorders of the musculoskeletal system. For the fourth session, members of the Hitachi Transport System Track and Field Club were invited to give a seminar about functional training,* which centered on correct walking posture, how to maintain one’s center of gravity and awareness, and how to use one’s shoulder blades and hamstrings, among others, as well as the importance of all of these factors. Also on offer was a program developed by Hitachi Transport System, Ltd., directed at the prevention of falls caused by tripping and stumbling.
The Tokyo Plant also conducted fall prevention training. Here, too, instructors were members of the Hitachi Transport System Track and Field Club, a renowned corporate club that is active in competitions across Japan, including the New Year Ekiden, one of Japan’s preeminent longdistance running multistage relay races. The Club’s manager, Kenji Beppu, taught participants how to walk correctly, including how to improve their posture, position their shoulders and raise their legs. Demonstrations were given by Kenta Ueda, a current member of the Club, who earned praise for his excellent posture and lithe movements. Going forward, the DIC Group will continue to plan programs like this that help improve employee health.
Hands-On Safety Training
The DIC Group provides hands-on safety training in Japan, Greater China and the Asia–Pacific region. The purpose of such training is to reduce employees’ willingness to take risks and foster their ability to recognize danger by simulating actual accidents. This began as a domestic initiative in 2012, after which deployment was expanded to include Greater China and the Asia–Pacific region. In Japan, handson safety training has helped to almost halve the occupational accident frequency rate at Group sites.
1. DIC Group Companies in Japan
In fiscal year 2014, the DIC Group opened the Saitama Hands-On Safety Center, a training facility that fosters skilled safety personnel by incorporating hands-on safety training in the new employee and rank-specific training programs. In the same year, DIC and DIC Graphics began including hands-on safety training and Kiken Yochi Training (KYT) (“hazard prediction training”) in the training curricula for new employees. The Chiba, Sakai, Hokuriku, Tokyo, Kashima and other plants have also established their own hands-on safety training equipment to further ingrain a safety-conscious corporate culture. In fiscal year 2015, the Group downsized six types of hands-on training equipment for lending to individual sites as part of a mobile training initiative. The Responsible Care Department trains employees at individual sites to serve as hands-on training instructors and has established an instructor licensing system.
2. DIC Group Companies in Other Countries and Territories
DIC Group companies in other countries and territories are also deploying Principles of Safe Conduct. In Greater China, hands-on safety training equipment has been installed at Nantong DIC Color Co., Ltd., DIC Graphics (Guangzhou) Ltd. and Changzhou Huari New Material Co., Ltd., in the PRC and DIC Graphics Chia Lung Corp. in Taiwan. In the Asia–Pacific region, equipment has been installed at DIC Compounds (Malaysia) Sdn. Bhd., PT. DIC ASTRA Chemicals in Indonesia, Thailand’s Siam Chemical Industry Co., Ltd., and DIC India Limited’s Noida Plant. These companies also provide hands-on safety training for employees of affiliated companies, as well as training for instructors, in their respective regions.
TOPICS
DIC Asia Pacific Holds Safety Day for Regional DIC Group Companies
The United Nations’ International Labour Organization (ILO)’s World Day for Safety and Health at Work, part of its campaign to promote occupational safety and health, is celebrated annually on April 28. In line with this initiative, DIC Asia Pacific held its first annual Safety Day on May 6, 2022. The theme of Safety Day in fiscal year 2022 was “CARE for Safety,” with the first word being an acronym drawn from three key ideas:
- Communication between colleagues and learning from each other
- Awareness of the environmental and safety issues
- Responsibility for actions and/or in actions
DIC Asia Pacific has set a target for its ESH program, encapsulated in the phrase “DIC ESH—Goal Zero,” which local Group employees are united in working to achieve. Safety Day 2022 activities at Group companies across the Asia–Pacific region centered on a Safety Day town hall meeting, which included video messages from the managing director who serves as general manager of the Production Management Unit and the managing director of DIC Asia Pacific, and Safety Day events and activities, which included games, quizzes, competitions, an awards ceremony and performances devised by the individual company.
Efforts to Foster a Safety-Conscious Corporate Culture
1. Safe Corporate Climate Cultivation Working Groups
In line with its “Safety First” philosophy, the DIC Group works to foster a safety-conscious corporate culture. In fiscal year 2011, personnel in charge of safety at plants belonging to DIC and DIC Graphics created Safe Corporate Climate Cultivation working groups, which meet regularly to discuss and exchange proposals regarding safety policies and measures, which are incorporated into Responsible Care initiatives.
2. DIC Safety Pledge Day
DIC has declared September 6 “DIC Safety Pledge Day,” an annual occasion for all of the DIC Group employees to pledge their commitment to ensuring safe operations and not repeating past serious accidents and disasters. On this day, each employee makes their pledge by writing a personal declaration on a special card.
Fiscal year | Working group initiatives |
---|---|
2012 | Working groups presented recommendations on safety policies and produced warning stickers to enhance awareness of workplace hazards. |
2013 | Working groups prepared safety posters featuring the president and CEO and started reading out key passages from Principles of Safe Conduct in workplaces with the aim of making the practices therein routine. |
2014 | Working groups prepared an illustrated version of Principles of Safe Conduct for reading out in workplaces. |
2015 | Working groups edited Principles of Safe Conduct into a tear-off calendar version for workplace reading circles, which was distributed to sites. The calendar version was also translated into English and Chinese. |
2016 | Working groups in the PRC began reading out key passages from Principles of Safe Conduct to foster a culture of safety. |
2017 | Working groups updated Principles of Safe Conduct. |
2018 | Working groups published the fifth edition of Principles of Safe Conduct. |
2019 | Working groups commenced production of a version of the fifth edition of Principles of Safe Conduct for workplace reading circles. |
2020 | The publication of a version of the fifth edition of Principles of Safe Conduct for workplace reading circles was scheduled, but was postponed until 2021 as a result of COVID-19. |
2021 | Site meetings were held at production facilities, with the president and vice present of DIC and the general manager of the Production Management Unit visiting each site to meet with frontline employees. A version of the fifth edition of Principles of Safe Conduct for workplace reading circles was published. |
2022 | Manual for protective equipment was revised. |
2023 | Accident records were revised to promote the effective horizonal dissemination of pertinent information and prevent the recurrence of past accidents. |
TOPICS
DIC Gives Presentations at the 5th China International Chemical Process Safety Symposium
The 5th China International Chemical Process Safety Symposium was held in May in the PRC. During the symposium, Responsible Care Department General Manager Shinobu Yamaguchi gave two presentations, at which he discussed the DIC Group’s chemical process safety initiatives and the Group’s management of chemical substance information, respectively. The symposium serves as a platform for the exchange of information on the latest technologies in the area of chemical process safety management, as well as on the outcomes of initiatives promoted by participating companies. DIC was invited to attend as a special guest of the China Chemical Safety Association, one of the symposium’s organizers.
DIC Participates in National Industrial Safety and Health Convention
The general manager of DIC’s Responsible Care Department took the stage as a panelist at National Industrial Safety and Health Convention 2022, which took place in Fukuoka, Japan, in November. The event, which focused on legal and regulatory changes in the realm of occupational health and safety made in 2022, featured panelists from government, academia and industry, namely, the Ministry of Health, Labour and Welfare; the University of Occupational and Environmental Health, Japan; the Japan Industrial Safety & Health Association; and DIC, who discussed challenges faced by companies in responding to legal revisions. Attendance at the event was high, with many attracted by the fact that it shone a spotlight on diverse related corporate initiatives. Participants could also take part from satellite facilities in other parts of the country. As a manufacturer of fine chemicals that handles a broad range of chemical substances, DIC presented past efforts to effectively manage chemical substances and comply with amended laws.
Disaster Prevention
Policies
Basic Approach
In addition to establishing a safety management system to prevent major accidents, the DIC Group implements prompt, effective countermeasures in the event an accident occurs.
Any fire, explosion or leakage of a hazardous substance from a chemicals plant could have a tremendous impact on local residents and the rest of the community and damage the health of employees, including those of our partner companies. As well as operating and maintaining its facilities in line with pertinent laws and regulations, the DIC Group regularly conducts emergency drills and has earthquake and other response measures in place in the event a major accident occurs.
Framework for Promotion
Under the supervision of the Sustainability Committee chair (DIC’s president and CEO), the Responsible Care Department works with the Safety and Environment groups of DIC Group companies, plants and R&D facilities to promote a variety of initiatives. In Japan, the Responsible Care Department holds meetings regularly with site Safety and Environment groups to confirm the status of priority issues and the achievement of targets, and to manage the progress of related efforts. In other countries and territories, the Responsible Care Department and individual regional headquarters work together to advance efforts, and site ESH officers, under the guidance of the pertinent regional headquarters, conduct risk assessments, analyze accidents and promote remedial measures to ensure the continuous improvement of occupational safety and health. (For more information, please see “Policies, Targets and Framework.”)
Principal Initiatives in Fiscal Year 2023
1. Process Safety Accidents
The International Council of Chemical Associations (ICCA) formulated criteria for chemical process safety accidents that require reporting in fiscal year 2017. Since fiscal year 2018, the DIC Group has reported process safety accidents for the Group in Japan in line with these standards. Beginning in fiscal year 2022, the Group sets targets based on results for the immediately preceding three years and implements measures to ensure their achievement.
In fiscal year 2023, the Group reported seven process safety accidents. The process safety accident frequency rate—the number of such accidents per 200,000 work hours—was 0.124, falling short of the Group’s target of 0.11. The principal reason for the Group’s suboptimal performance was the leakage of chemicals, which happened several times. Looking ahead, the Group will assess risks associated with production processes and make necessary improvements.
- Note: In Japan, a process accident requires reporting if the four criteria listed below are met. (These apply primarily to fires, explosions and the leakage of hazardous substances related to manufacturing processes).
- (1)The accident was related directly to a chemical substance or a chemical process.
- (2)The accident involved production, logistics, storage, utilities or pilot plants.
- (3)The accident caused the release of material or energy (e.g., a fire, explosion or implosion) from a process unit.
- (4)The accident resulted in any of the following events: Occupational accident, equipment damage, evacuation or the release of substances included in the Globally Harmonized System of Classification and Labelling of Chemicals (GHS).
Fiscal year 2019 |
Fiscal year 2020 |
Fiscal year 2021 |
Fiscal year 2022 |
Fiscal year 2023 |
|
---|---|---|---|---|---|
Number of ICCA process safety accidents |
6 | 4 | 7 | 3 | 7 |
Process safety accident frequency rate |
0.110 | 0.073 | 0.128 | 0.055 | 0.124 |
2. Risk Assessments at Chemicals Production Facilities
The DIC Group’s production facilities have an array of application-specific equipment, ranging from units where chemical reactions are conducted to machine presses and other processing equipment. In 2013, the Group formulated the DIC Process Risk Management (PRM) Guidelines, which it uses to conduct systematic risk assessments at individual sites. These guidelines outline timetables and implementation frameworks for assessing risks associated with chemical substances handled, production processes, production formulas, machinery and work practices. Since fiscal year 2020, the Group has also used hazard and operability (HAZOP) studies developed to assess the risk of accidents such as the leakage of hazardous substances, fires or explosions at chemicals production facilities. Specifically, the Group deploys HAZOP studies to assess risks at facilities that have chemical reaction equipment, including the Yokkaichi, Chiba, Kashima, Sakai and Hokuriku plants.
3. Third-Party Assessments by the Safety Competency Enhancement Center
In 2013, DIC introduced an assessment system as a means of objectively evaluating and enhancing its safety competency.* This system was developed by the Japan Society for Safety Engineering (JSSE), together with chemicals industry engineers, as a common industry benchmark and is currently used by all companies in Japan that are members of the Safety Competency Enhancement Center. Between fiscal year 2014 and fiscal year 2020, assessments were conducted at all DIC plants in Japan. These facilities have used assessment results to promote further improvements. The Yokkaichi Plant, for example, subsequently launched a HAZOP study–based risk assessment. In December 2019, the Safety Competency Enhancement Center provided DIC’s president and CEO with an overall report on the results of assessments conducted at six production facilities, facilitating the sharing of understanding regarding safety and disaster-related issues across the management team.
- The assessment system encompasses questions about safety infrastructure (technical considerations) and culture of safety (operation and management of organizational culture).
4. The DIC BC Portal
Because of its location, topography and climate, Japan is vulnerable to a variety of natural disasters, including typhoons, heavy rains, floods, earthquakes and tsunami. An accident at, for example, a chemicals production facility involving a fire, explosion or the leakage of hazardous substances, can also have a significant impact on local communities. In such a situation, it is necessary to collect, comprehend and share accurate information to facilitate appropriate decision making and prompt action. DIC has introduced the DIC BC Portal disaster information system, a web-based system facilitating the collection and sharing of information when an accident or disaster occurs.
A recent natural disaster that underscored the benefits of the DIC BC Portal was the 2024 Noto earthquake, a magnitude 7.6 earthquake that struck the Noto Peninsula of Ishikawa Prefecture on January 1, 2024, at approximately 4:10 pm. An intensity of 7 on the Japan Meteorological Agency (JMA) Seismic Intensity Scale was recorded in the cities of Shika and Wajima, while an intensity of 5 Lower was recorded in the city of Hakusan, where DIC’s Hokuriku Plant is located. The plant was fortunately not operating at the time and there was no major damage. The safety of employees was confirmed and damage to structures were reported via the new portal. Previously, information on accidents, disasters and resulting damage were made by telephone and email, among others, using an emergency contact network, but there were issues with the speed, precision and the scope of information sharing. The DIC BC Portal has thus allowed the Company to create a system for sharing information swiftly and exactly, positioning it better to make effective decisions.
5. Emergency Response Drills
In addition to daily security patrols and periodic equipment checks, the DIC Group conducts regular emergency response drills based on business continuity plans (BCPs) at production sites in Japan.
Environmental Protection
Policies
Basic Approach
The DIC Group seeks to contribute to protection of the global environment by improving its own environmental performance, as well as by complying with pertinent laws and regulations.
Environmental protection is among the most important of corporate sustainability activities. The DIC Group’s efforts focus on a number of areas, including addressing climate change, preventing environmental pollution, managing industrial waste (responding to a circular economy), managing water resources and biodiversity. As a manufacturer of fine chemicals with operations around the world, the Group promotes environmental protection with a global perspective.
Groupwide Environmental Performance
The DIC Group quantifies the environmental inputs (consumption of energy and other resources) and outputs (emissions into the environment) of its operating activities, and uses its findings to formulate far-reaching and efficient strategies for reducing its environmental footprint. The chart on the next page is a comprehensive illustration of the environmental impact of the Group’s operating activities in Japan and in other countries and territories. This chart shows environmental impact in fiscal year 2023 for two key items (total energy consumption and total water consumption) and three output items (emissions into the air, emissions into water and emissions into soil) in three categories: CO₂ emissions, total wastewater discharged and industrial waste disposed of as landfill. (Data for the DIC Group in Japan also includes emissions of substances targeted under pollutant release and transfer registers (PRTRs) into the air, water and soil of NOx and SOx, as well as COD in wastewater.)
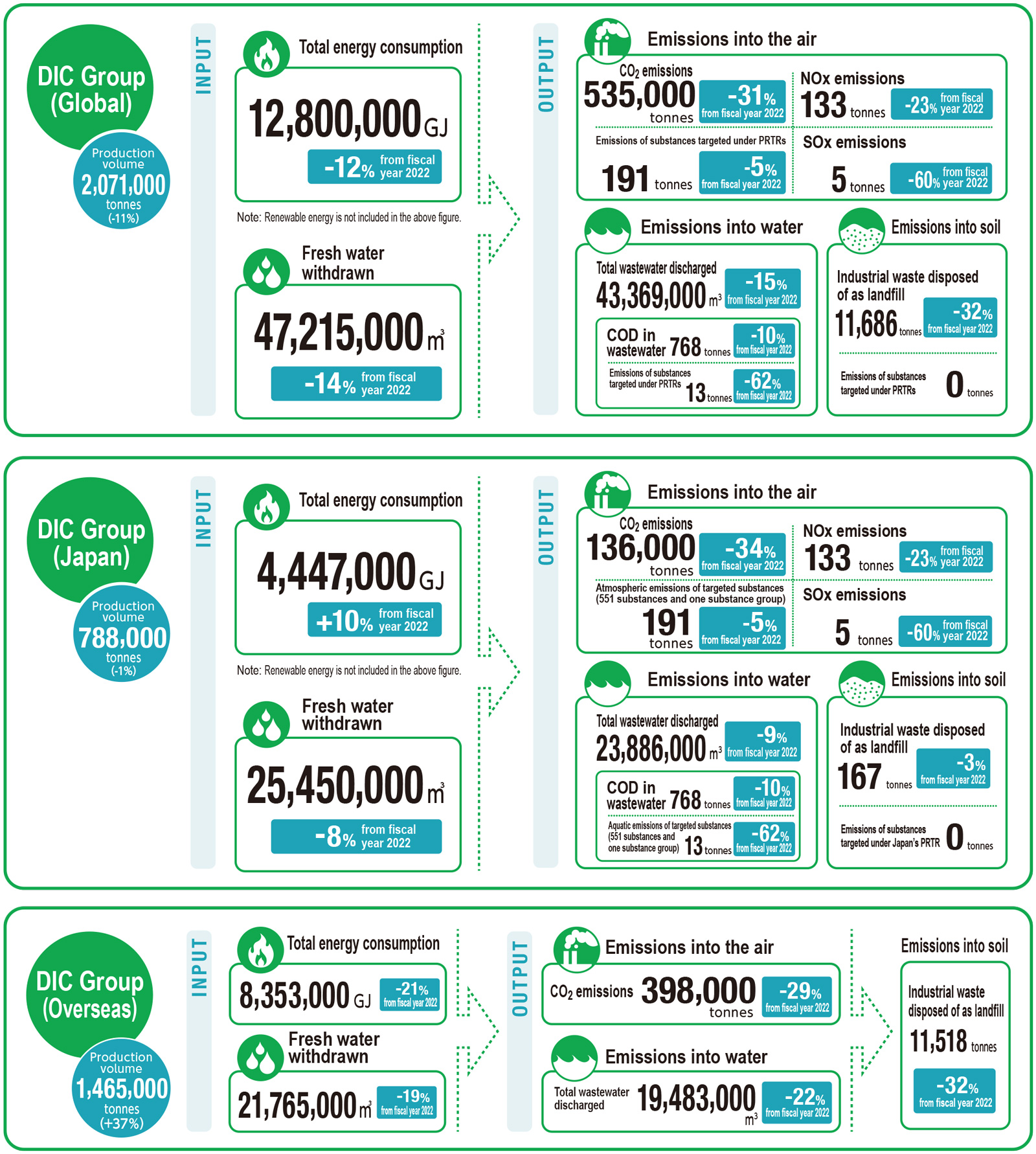
- Note: DIC monitors 462 class 1 chemical substances designated by Japan’s PRTR and 89 PRTR-designated substances (other than class 1) and one substance group (chain hydrocarbons with up to 4–8 carbon atoms) targeted for study by the JCIA.