Kawamura Ink Manufactory is established
Popular and consumer culture evolved swiftly in Japan following the Russo-Japanese War with the rapid modernization of daily life. Underscored by the launch of numerous magazines devoted to the arts and a boom in the popularity of picture postcards, as well as by rising demand for attractive packaging for cosmetics and food products, a revitalized cultural scene had a direct and positive impact on demand for printing services, spurring the growth of Japan's printing industry. Recognizing the potential of this trend, Kijuro Kawamura resolved to go into business as a manufacturer of printing inks and established Kawamura Ink Manufactory.
Kawamura set up a plant in Tokyo, installing three gas engine–powered 8x12-inch roll mills, and launched operations with just three employees, commissioning a traveling salesman to handle marketing. The new company began by manufacturing white, blue, yellow and red inks for woodblock, lithographic and typographic printing, all of which were in particularly high demand, purchasing raw materials (pigments and varnishes) and selling milled inks. Sales were brisk from the word go, ensuring the Company got off to a smooth start.
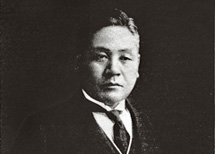