Policies, Targets and Framework
Policies, Targets and Framework
Basic Approach
The DIC Group promotes a broad range of ESH initiatives through its Responsible Care program.
Initiatives to Date
As a global organization that manufactures and sells chemical substances, the DIC Group promotes a broad range of ESH initiatives through its Responsible Care program. Having established its Principle and Policy for the Environment, Safety and Health in 1992, in 1995 DIC pledged to implement the precepts of Responsible Care. Since reaffirming its support for Responsible Care management in January 2006 by signing the CEO’s Declaration of Support for the Responsible Care Global Charter, the Company has promoted constant improvements. Today, the Group manages its Responsible Care program in a uniform manner using standardized codes, guided by its Environment, Safety and Health Policy, and works to implement initiatives that exceed regulatory requirements, in line with annual Responsible Care activity plans, and to fully disclose the results thereof.
- Note:
Responsible Care describes voluntary management initiatives undertaken by companies that manufacture or otherwise handle chemical substances, in line with the principles of autonomous action and self-assessment, pledging in their management policies to protecting the environment and ensuring health and safety across the entire life cycle of products, from development to manufacturing, distribution, use and end-of-life disposal, as well as to disclosing related information and promoting improvements.
Environment, Safety and Health Policy
As a responsible corporate citizen and as a company that manufactures and sells chemical substances, DIC recognizes that care for the environment, safety and health is fundamental to the management of the Company. DIC is committed to the concept of sustainable development in all aspects of its businesses and contributes to the global environment, including biodiversity, by creating environmentally sound products and technologies.
- We take responsibility for the environmental, safety and health implications of products throughout their life cycles.
- We continuously set goals and targets for environmental, safety and health improvements.
- We comply strictly with laws, regulations and agreements relative to the environment, safety and health. For countries lacking such laws, we prioritize safe operations and protection of the environment.
- We systematically provide education and training on the environment, safety and health.
- We prepare systems and audit internally to benefit the environment, safety and health.
We disclose these policies internally and externally and ask that all DIC Group companies observe them. The abovementioned “safety” also encompasses security and disaster prevention.
Responsible Care Codes
The DIC Group manages its Responsible Care program in accordance with seven codes:* “Occupational safety and health” (protection of the safety and health of employees), “disaster prevention” (prevention of fires, explosions and the discharge of chemicals), “environmental protection” (continuous reduction of chemical emissions and the discharge of waste), “safety in logistics” (reduction of chemical risks associated with the distribution of chemicals), “ensuring the safety of chemical substances” (management of risks associated with chemicals), “engaging with society” (communication with local communities regarding ESH) and “management systems” (ensure the uniform administration of the first six codes). In line with these codes, the Group applies the plan-do-check-act (PDCA) cycle and conducts annual ESH audits and management reviews to evaluate initiatives.
- The seven Responsible Care codes were developed by the Japan Responsible Care Council (JRCC), which is part of the JCIA, as a framework for Responsible Care programs with the goal of helping achieve a society that supports efforts to address ESH-related initiatives.
- Occupational safety and health (protection of the safety and health of employees)
- Disaster prevention (prevention of fires, explosions and the discharge of chemicals)
- Environmental protection (continuous reduction of chemical emissions and the discharge of waste)
- Safety in logistics (reduction of chemical risks associated with the distribution of chemicals)
- Ensuring the safety of chemical substances (management of risks associated with chemicals)
- Engaging with society (communication with local communities regarding ESH)
- Management systems (ensure the uniform administration of the first six codes)

Message from the President
DIC’s president prepares a message for employees for Environment Month and National Safety Week.
TOPICS
Management Spearheads the Promotion of Safety Initiatives
Believing that it is important for management to take the lead in promoting a “Safety First” philosophy, the managing executive officer who serves as general manager of the Production Management Unit prepares a monthly memo for distribution to all DIC Group sites in Japan.
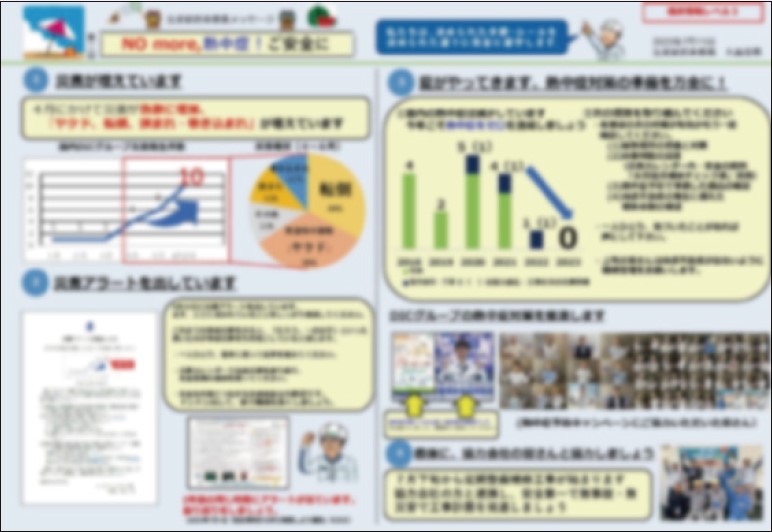
Framework for Promoting Responsible Care
The Sustainability Committee, which answers directly to the president and CEO, is responsible for setting Responsible Care initiatives. Chaired by the president and CEO, the committee includes business group presidents, administrative unit heads, CEOs of regional headquarters and members of the Audit & Supervisory Board. The committee approves Groupwide sustainability targets and policies, as well as deliberates and evaluates medium-term sustainability policies and annual sustainability activity plans. The PDCA cycle is used to evaluate voluntary Responsible Care initiatives implemented by Group companies, plants and R&D facilities in line with these policies and plans in collaboration with the Safety and Environment Group. The Responsible Care Department provides support to ensure the smooth progress of these initiatives and conducts audits to ensure compliance and improve safety and environmental performance.
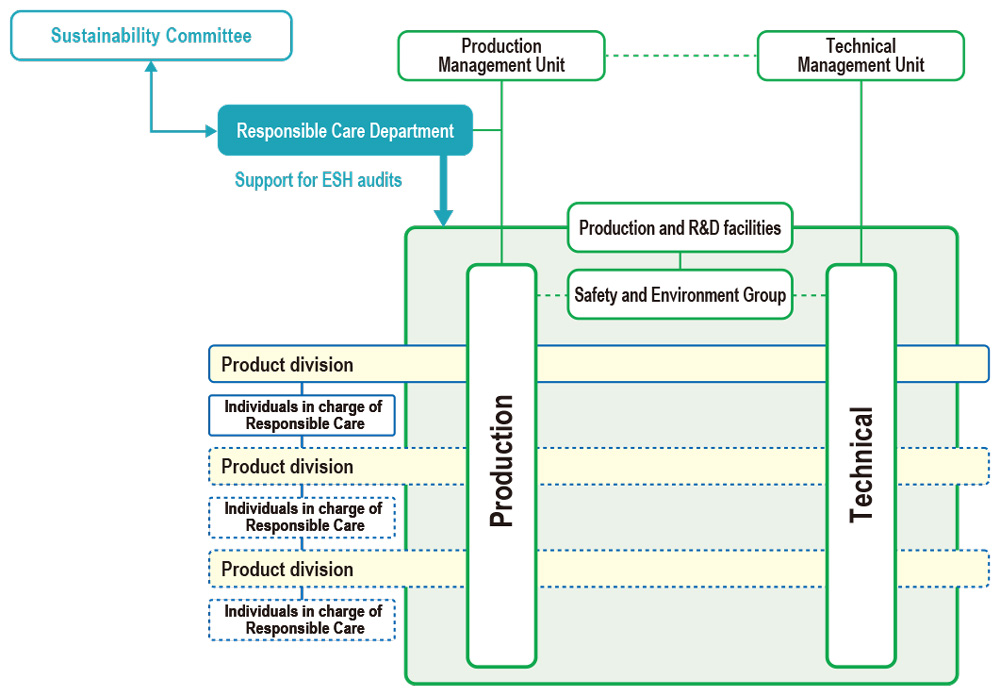
Deployment of Responsible Care Initiatives at Group Companies
The Responsible Care Department provides wide-ranging support to DIC Group companies worldwide, regardless of operating scale, with the goal of enhancing Responsible Care initiatives Groupwide. Of particular note, the department assists regional headquarters in Greater China and the Asia–Pacific region in fostering human resources.
1. Initiatives in Japan
The DIC Group has 16 companies and 39 production and R&D sites in Japan. Safety and Environment groups have been established at each site, which are overseen by the Responsible Care Department. DIC and DIC Graphics hold GM conferences, which are gatherings of group managers from principal sites who have been appointed group managers, four times a year. Other domestic Group companies participate in biennial Responsible Care conferences. These various conferences facilitate the discussion of efforts to prevent accidents and disasters, share information on environmental challenges and ensure common awareness of Groupwide rules.
TOPICS
Responsible Care Department Holds 50th Anniversary Group Safety Conference
To commemorate the 50th anniversary of its Responsible Care Department, in fiscal year 2023 the Company held a celebratory Group safety conference to bolster safety consciousness across the Group. The conference’s opening ceremony was attended by 17 representatives from corporate headquarters, including the president and CEO, the general manager of the Production Management Unit and eight site representatives, and included the handing out of awards to individuals who demonstrated a particularly outstanding performance in the areas of safety and health, and also disaster prevention. This was followed by a lecture on safety given by a guest speaker. A commemorative publication summarizing the history and achievements of the DIC Group in the area of sustainability produced by DIC was distributed to attendees, enabling them to learn more about the Responsible Care Department since its inception.
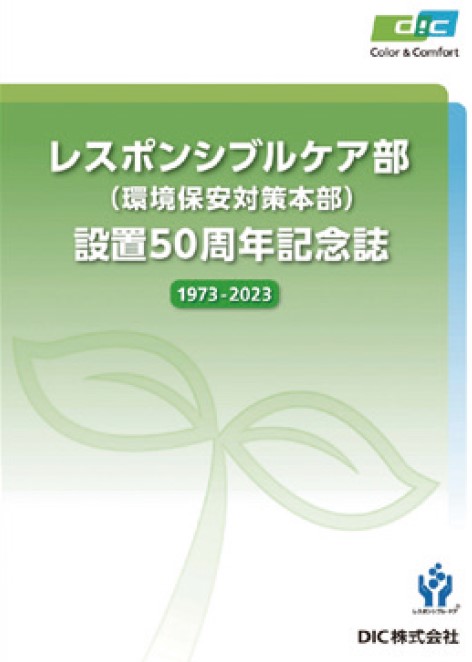
2. Initiatives in the Asia–Pacific Region
The DIC Group has 21 companies and 22 production sites across the Asia–Pacific region. A regional ESH director has been installed at DIC Asia Pacific, the Group’s regional headquarters, in Singapore, who supervises ESH country heads (individuals in charge of ESH initiatives) in key countries and territories in the region. In addition to an annual regional conference that is also attended by the Responsible Care Department, monthly meetings are held with the Chemical Substance Information Management Group, established in fiscal year 2023, to reinforce communication. Country heads hold regular countryand territory-specific meetings, convening representatives to local subsidiaries and sites to discuss initiatives, targets and challenges.
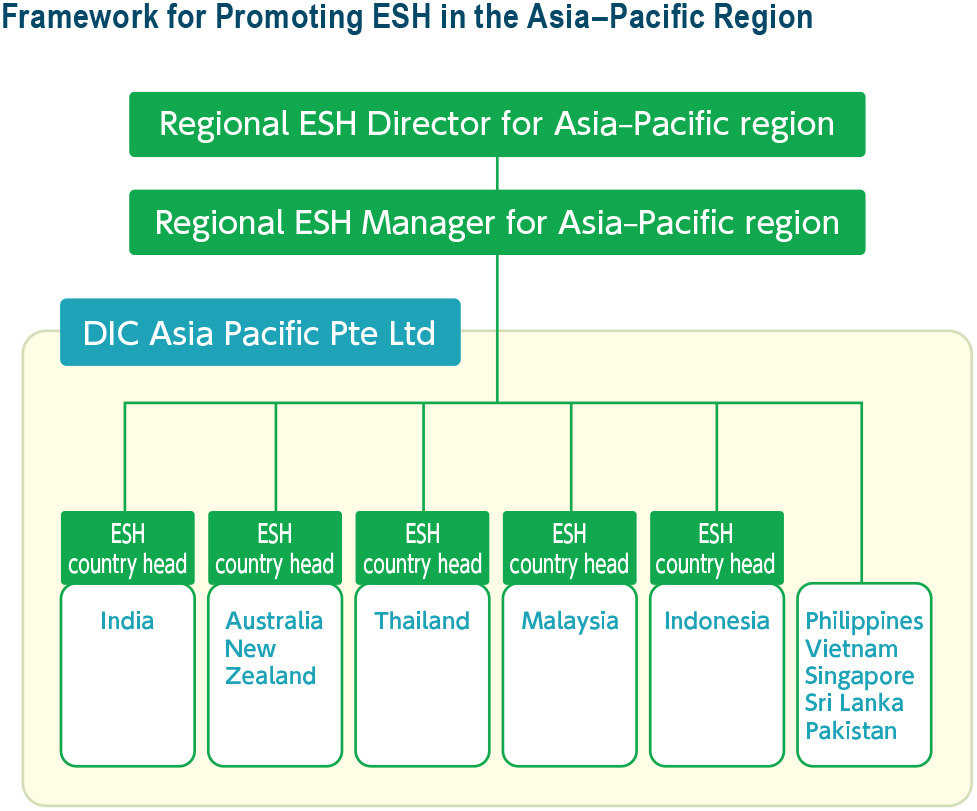
TOPICS
Asia–Pacific Region DIC Group Company Holds Annual Safety Day in 2023
The International Labour Organization (ILO)’s World Day for Safety and Health at Work, part of its campaign to promote occupational safety and health, is celebrated annually on April 28. In line with this initiative, DIC Group companies overseen by DIC Asia Pacific hold their own annual Safety Day events.
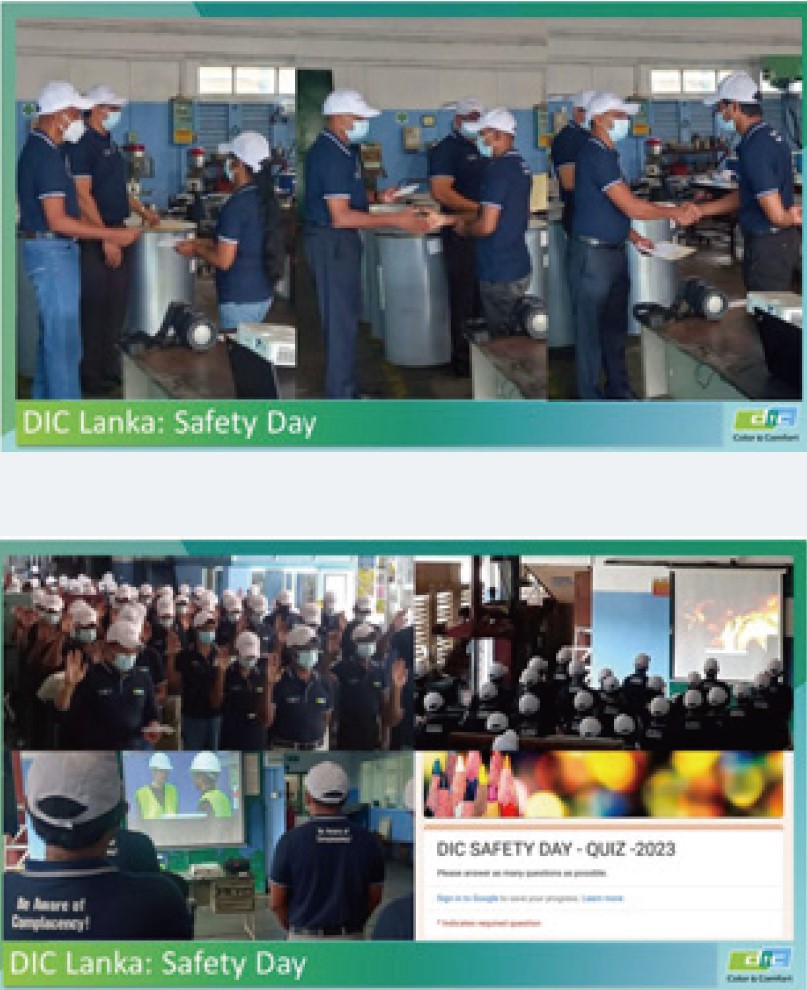
3. Initiatives in Greater China
In Greater China, the DIC Group has 16 companies and 20 sites. To fortify the Group’s regional ESH framework, DIC has assigned a regional ESH director to DIC (China), the Group’s regional headquarters, and ESH coordinators to the southern and eastern parts of the country. In addition to an annual regional conference that is also attended by the Responsible Care Department, monthly meetings are held with the newly established Chemical Substance Information Management Group to reinforce communication.
VOICE
Safety message from the winner of DIC (China)’s 2023 safety knowledge quiz
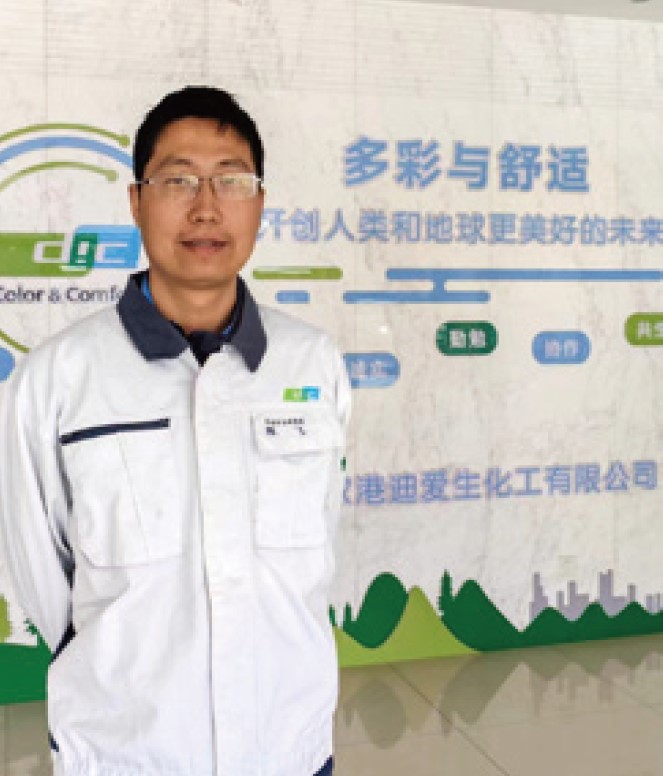
DIC (China) holds an annual safety knowledge quiz for DIC Group employees in the PRC with the goal of improving know-how and encouraging active participation in the effort to maintain a safe work environment. The following is a message from Chen Fei of DIC Zhangjiagang Chemicals Co., Ltd., winner of the 2023 quiz.
—Thoughts on Safety Activities—
When I first became involved in safety-related initiatives, I thought that “safe” was simply a state of being. In other words, as long as we were able to manage things in a way that kept employees and equipment in a safe condition—i.e., as long as people were safe—our workplace was safe. However, as I learned about the safety management policy of the DIC Group, and of DIC Zhangjiagang Chemicals, and as I gained experience in the everyday management of safety and my related skills improved, I came to better understand safety management as a comprehensive system. Today, I recognize that safety is something that can only be achieved by everyone making safe choices. The essence of safety is the creation of a risk-free environment. This entails choosing both safer behavior and safer equipment. Accordingly, the most important thing is to encourage employees to make safe choices. To this end, DIC Zhangjiagang Chemicals has identified five crucial prerequisites.
The first is that management, including general managers, must place an emphasis on safe operations and encourage all employees to improve their safety awareness. The second is that we must teach employees the risks of making unsafe choices through risk management training and educational programs dealing with occupational accidents conducted by external providers. Third, we must teach safe behavior by developing systems, standard operating procedures and processes. Fourth, through training and other initiatives we must educate employees so that making safe choices becomes second nature. Last, we must correct unsafe choices through safety inspections, behavioral observations and other measures.
In closing, I want to ask all employees to always check that what they are about to do is safe before they start! Consider whether there is not a safe and rational approach that could possibly be deployed across the workplace, thereby making it even safer for everyone.
DIC Zhangjiagang Chemicals Co., Ltd. Chen Fei
Thoughts on Daily Efforts to Ensure Safety
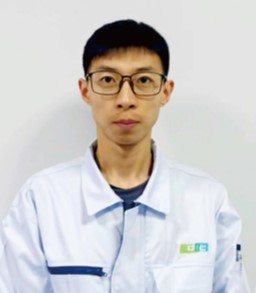
What does “safety” mean? At my previous company, it was endless classes, protective gear to change into before starting work, frontline risks to comprehend, safety notices on the walls and written rules. At DIC, it is the education and training I attend, the protective gear I put on, the risks I identify, the safety notices that I am consistently aware of and the rules that I observe without fail. These may sound pretty much the same on the surface, but in fact the safety culture of the two companies is really very different.
From Companywide emergency drills to itemized emergency response plans, the monthly sharing of case studies and meticulous on-site work processes, DIC’s approach reflects the people-first philosophy that underscores its safety culture. All around us, there are protective guards on sharp-cornered control panels and fluorescent labels on stairs to prevent falls. Every day at our morning meeting, key passages from Principles of Safe Conduct are read aloud. An effective safety culture is a result of the daily accumulation of experience and know-how. In this environment, my mindset changed. I began to see safety not as something being forced on me, but rather something that I do of my own accord. This is the sentiment conveyed in DIC’s safety slogan, “Safety is one’s own responsibility.”
Qingdao DIC Finechemicals Co., Ltd. Yu Hezhi
4. Initiatives in the Americas, Europe and Africa
The Sun Chemical Group oversees all Responsible Care initiatives by DIC Group companies in the Americas, Europe and Africa. Periodic regional conferences and online meetings are held between local ESH staff and the Responsible Care Department to ensure the DIC Group’s ESH policy and its values are shared by all.
Annual Activity Plans
The DIC Group formulates an annual Responsible Care Activity Plan and oversees Groupwide initiatives. Based on the Group’s annual plan, which is prepared by the Responsible Care Department, regional headquarters develop their own region-specific activity plans, while individual Group companies, in line with the concept of management by objectives (MBO), translate these plans into reality by promoting a variety of Responsible Care initiatives.
The DIC Group’s Annual Responsible Care Activity Plan for Fiscal Year 2023
-
Occupational safety and health
- The DIC Group’s fundamental objective remains the achievement of accident-free workplaces. With this in mind, set regional targets for total recordable incident rate (TRIR) in fiscal year 2023 and implement related initiatives.
- Encourage safety and health awareness among all employees.
-
Disaster prevention
- Encourage the horizontal deployment of measures based on the lessons learned from past major accidents and take steps to prevent their recurrence.
- Conduct risk assessments with the aim of reducing process risks.
- With the aim of reducing process safety accidents, continue calculating such accidents in accordance with the ICCA guidelines.
-
Environmental protection
- Maintain/lower the impact of production activities on air and wastewater quality.
- Reduce the generation of and maintain/increase the resource recycling rate* for industrial waste.
- Continue to assess water risks affecting production activities. Consider approaches to managing targets for the reduction of water consumption.
- Implement initiatives aimed at improving environmental compliance.
-
Safety in logistics
- Continue to provide information pertinent to the safe transport of chemicals.
-
Ensuring the safety of chemical substances
- Promote the creation of a new global system for managing chemical substance information.
- Further expand deployment of the Wercs and Atrion at DIC Group companies overseas.
- Increase understanding of domestic and overseas laws and regulations governing chemical substances and prevent violations thereof by further enhancing in-house legal and regulatory training, including at overseas Group companies.
-
Engaging with society
- Continue to publicize the results of Responsible Care activities.
-
Management systems
- Make use of the ESH data collection system.
- Reinforce relations between corporate headquarters and regional headquarters to prevent accidents/disasters in Greater China and the Asia–Pacific region.
- Promote environment- and safety-related education.
- Resource recycling rate is calculated as (Volume of industrial waste recycled (material recycling) + Waste heat recovered (thermal recycling) / Volume of industrial waste generated