地球温暖化防止への取り組み(2017年度の主な活動)
2017年度の主な活動
01CO2排出量削減の中期目標策定
DICグループは、サステナビリティ活動のキーワードとして「低炭素化」を掲げ、事業活動における省エネルギーと再生可能エネルギーの採用(バイオマス燃料の採用、太陽光・風力発電の導入、低炭素電力の採用など)を推進することでCO2排出量の削減に注力しています。
2016年10月にはサステナビリティ委員会において「CO2の排出量(絶対量)を、2013年度を基準年として2020年時点に7%削減する」という中期目標を策定しました。目標を達成するため、これまで重点を置いてきた「事業所での省エネルギー施策のたゆまぬ実行」とともに、バイオマスボイラや太陽光発電といった「再生可能エネルギーの積極的導入」や「低炭素な電力の購入」といった側面も活動の柱に加えて取り組みを推進しています。
次期中期経営計画においては、2020年以降の目標設定についても取り組みを進めています。
02DICグループのエネルギー使用量とCO2排出量の実績(グローバル)
2017年度の生産数量は前年度比1.1%増加しましたが、エネルギー使用量は2.9%減少(11,379⇒11,053千GJ)し、CO2排出量も3.7%減少(659,378⇒634,741t)しました。
DICグループの生産品はインキ・ポリマ・顔料・液晶・エンジニアリングプラスチック・コンパウンドなど多種多様です。最近の傾向として、生産工程でエネルギーを多く必要とするファインケミカル製品が増加傾向にあり、比較 的エネルギーを必要としない製品が減少傾向にあります。
このような状況の中でCO2排出量を年度目標以上に削減できたのは、国内外で積極的に省エネ・低炭素化施策が実行できたことに尽きます。
一方、生産数量1tあたりに排出するCO2量の指標(CO2排出原単位:kg-CO2/t)は前年度比4.7%減少し(311⇒296kg-CO2/t)、当社が基準年とする2013年度比では9.5%減少しました。この結果から、生産におけるエネルギー使用効率は着実に向上していることが伺えます。
各生産拠点では、今後も高効率設備の導入や工程改善、設備稼働率の向上といった省エネ施策を実施するとともに、クリーンな燃料への転換や太陽光発電の導入などの再生可能エネルギーの推進にも取り組んでいきます。
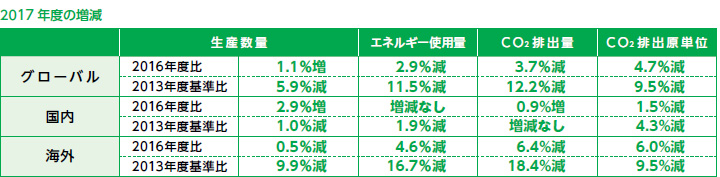
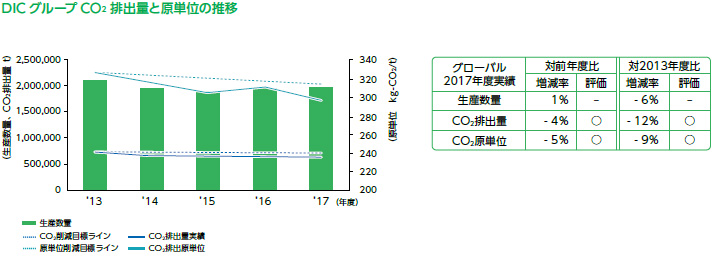
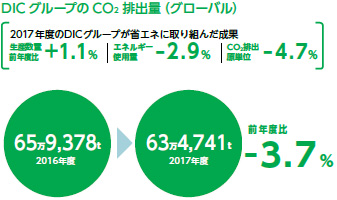
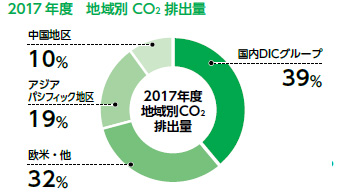
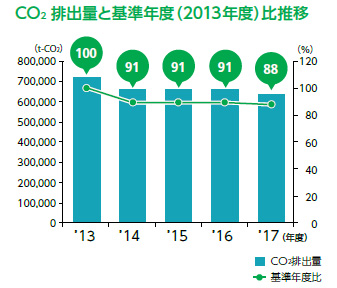
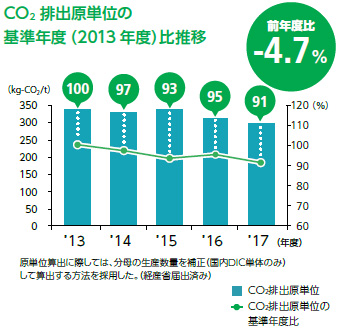
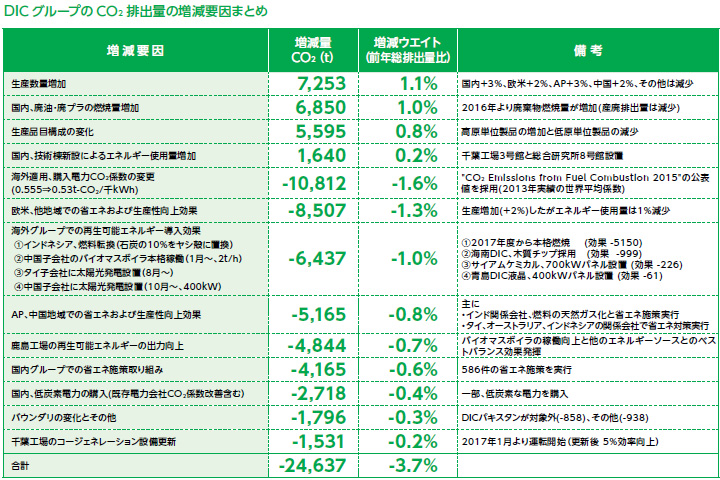
03国内におけるエネルギー使用量とCO2排出量
国内DICグループ(DIC+グループ会社の52事業所)は、生産数量が前年度比2.4%増加しました。
エネルギー使用量は前年度比でほぼ増減なし(4,314 ⇒ 4,314千GJ)でしたが、省エネ法の指標であるエネルギー消費原単位は2.4%減少(4.010 ⇒ 3.915 GJ/t)しました。
一方、CO2排出量は同0.9%増加(242,194 ⇒ 244,395t)しましたが、CO2排出原単位は同1.5%減少(225 ⇒ 222kg-CO2/t)しました。CO2排出量の増加は、エネルギーを多用するファインケミカル製品などの生産増によるものと廃棄物の燃焼量増加が主な要因です。その中で、①鹿島工場の再生可能エネルギー(バイオマスボイラ・風力発電・太陽光発電)の稼働向上と、コージェネレーションシステム(最大発電量1,700kW)を含むエネルギーソースのベストバランス効果がもっとも大きく寄与しました。また、②千葉工場のコージェネレーションシステムの更新(最大発電量3,375kW、蒸気量8t/h)による効率アップ、③各事業所の省エネ取り組み586件実施などでエネルギーの効率化を図ったことにより、その結果、エネルギー消費原単位とCO2排出原単位を改善しました。
また、サプライチェーンを通じたCO2間接排出量(Scope3※)については、15項目中6項目(資本財、輸送・配送上流、事業から出る廃棄物、出張など)を算定しており、その中の「事業から出る廃棄物」については第三者検証を得ています。
- Scope3:製造・輸送・配送・出張・通勤等の際に、企業が間接的に排出するサプライチェーンでのCO2排出量。
04国内DICグループの省エネルギー活動と取り組み実績
各事業所(工場・研究所)では下記のベースロードエネルギーの削減と、生産方法の効率化による低エネルギー化や工程時間短縮を切り口に、PDCAサイクルを回して省エネ活動に取り組むとともに、2017年度からは「低炭素化」の推進にも力点を置き取り組みました。
- 照明や空調の高効率化とムダ排除策
- ポンプやブロアの省エネ制御の導入
- コンプレッサーの高効率化や圧力損失低減策
- 電気設備の力率改善策
- 高COPチラーの採用と冷温水供給のムダ排除策
- 排熱回収によるボイラ燃料等の低減
- 原料類の加温時間や加温温度の適正化
- 条件の見合う事業所への再生可能エネルギーの導入
(太陽光発電、バイオマスボイラなど) - 条件の見合う事業所での低炭素電力の購入
- 鹿島工場の再生可能エネルギーの出力向上
- 国内グループでの省エネ施策取り組み(586件実施)
- 低炭素電力購入(既存電力会社のCO2係数改善含む)
- 千葉工場のコージェネレーション設備更新
2017年度は、これらの活動により約233千GJ(原油換算:約6千㎘)のエネルギーを節減しました。これは200ℓのドラム缶約30,000本分に相当し、国内DICグループが使用したエネルギー総量の5.4%に相当します。
今後も継続して省エネ施策の推進を図るとともに、新たなテーマの発掘や各事業所の優秀事例の水平展開に注力します。加えて、ボイラ・チラー・コンプレッサー等のエネルギー消費主要設備について、最適性能を引き出すための管理マニュアルを強化し、国内はもとよりグローバル拠点にも展開していきます。
2017年度 DICグループ省エネ取り組み実績(計586件の取り組み実績の内の主要テーマ)
工場名 | 実施した省エネ施策 | エネルギー削減量( GJ ) | CO2削減量( t ) |
---|---|---|---|
千葉工場 | ポリマ生産工程のベースロード改善による蒸気使用量削減 | 883 | 53 |
千葉工場 | グリセリン原料タンクの加温方式の変更 | 670 | 40 |
千葉工場 | 不良スチームトラップ更新による省エネ(トラップ診断実施) | 798 | 48 |
千葉工場 | 用水ポンプと熱媒ポンプ更新、反応停止時ポンプ停止処置 | 3,172 | 155 |
千葉工場 | LED照明化 | 1,126 | 55 |
千葉工場 | 千葉工場その他省エネ取り組み | 10,744 | 548 |
鹿島工場 | 顔料生産工程の省エネ対策実施 | 1,535 | 78 |
鹿島工場 | 機能性/添生産工程の省エネ対策実施 | 695 | 35 |
鹿島工場 | EP脱水洗浄工程、熱処理取出工程改善等による熱使用量削減 | 6,488 | 327 |
鹿島工場 | 原動、スチームロス削減、排水攪拌運用改善、LED化等 | 772 | 39 |
鹿島工場 | 鹿島工場その他省エネ取り組み | 186 | 10 |
堺工場 | ヒーターBOX新設 | 699 | 37 |
堺工場 | 湯洗い水量変更 | 467 | 24 |
堺工場 | B、D変電所の電力改善システム設置による電力削減 | 1,240 | 365 |
堺工場 | 炉筒ボイラの蒸気乾き度改善による燃料削減 | 1,194 | 63 |
堺工場 | 技術棟空調更新(ガスヒーポン⇒EHP) | 4,908 | 257 |
堺工場 | 堺工場その他省エネ取り組み | 3,833 | 200 |
北陸工場 | SH現場、生産工程中のベースロード削減 | 941 | 52 |
北陸工場 | J現場、循環ポンプ運用改善・蒸気トラップ改善、等 | 1,482 | 91 |
北陸工場 | E現場、生産工程時短・加温庫改善、等 | 511 | 31 |
北陸工場 | GLM現場、蒸気トラップ改善・照明LED化、等 | 504 | 32 |
北陸工場 | 原動現場、排水ミキサー・井戸水ポンプ運用改善・トランス更新、等 | 991 | 63 |
四日市工場 | E系FCP渦巻きポンプ化 | 397 | 20 |
四日市工場 | ブライン冷凍機使用の1台化 | 1,159 | 59 |
四日市工場 | 熱回収基準化 | 278 | 14 |
四日市工場 | ラインバルブ設置による蒸気ロス削減、他 | 504 | 25 |
小牧工場 | DICG勤務体制の見直しによるエネルギー使用量削減、等 | 580 | 28 |
小牧工場 | SC製造押出機ヒーター保温、その他乾燥条件見直し、等 | 3,161 | 155 |
小牧工場 | 照明のLED化による電力量の削減、等 | 476 | 23 |
小牧工場 | 小牧工場その他省エネ取り組み | 705 | 34 |
館林工場 | コンプレッサー更新によるベース電力削減、等 | 661 | 34 |
館林工場 | 照明のLED化による電力量の削減、等 | 355 | 18 |
館林工場 | SC製造工程のおける省エネ対策 | 870 | 45 |
館林工場 | 館林工場その他省エネ取り組み | 680 | 35 |
東京工場 | 照明のLED化による電力量の削減、等 | 875 | 45 |
東京工場 | 東京工場その他省エネ取り組み | 385 | 20 |
群馬工場 | 工場不要制御盤電源断 | 3,061 | 154 |
群馬工場 | D工場窒素発生装置運用変更 | 308 | 16 |
群馬工場 | D工場コンプレッサー更新等 | 951 | 48 |
宇都宮工場 | 圧空コンプレッサー稼働時間短縮+INV | 1,025 | 55 |
宇都宮工場 | 冷却水、冷水、温水ポンプの運転時間短縮 | 3,501 | 193 |
宇都宮工場 | チラー更新、屋外倉庫エアハン夏季停止、その他生産合理化 | 2,469 | 141 |
宇都宮工場 | 生産工程合理化ロールレス | 1,210 | 70 |
宇都宮工場 | インキ生産エリア(非防爆)水銀灯⇒LED化 | 1,395 | 72 |
関西工場 | 照明のLED化による電力量の削減、等 | 522 | 27 |
関西工場 | 関西工場その他省エネ取り組み | 489 | 25 |
その他 | 工程改善、照明LED化、老朽化設備の省エネタイプへの更新 | 8,912 | 506 |
省エネ施策取り組み実施 (計586件) | 78,768 | 4,165 |
「エネルギーの見える化システム」で収率向上
DICでは、設備ごとにエネルギー使用量をリアルタイムで計測・監視し、ムダ・ムラをなくして最適化を図る「見える化システム」を構築。北陸工場(2012年省エネルギーセンター会長賞)をはじめ各事業所に水平展開を図り、2014年度には小牧工場へ導入しました。また、品種やロットごとのエネルギー使用量を工程別に解析できる見える化システムを千葉V現場・鹿島C 現場・堺工場B 現場に導入し、原料の投入量に対して収率の最適化を図る「ゴールデンバッチ」の再現を推進。2016年には、このシステムをさらに高度化して四日市工場に導入しました。
「改善力アップ研修」で省エネ・品質向上などを推進
DICでは、生産に関わる従業員一人ひとりの高い意識や改善スキルの向上こそ現場力の強化に直結すると位置づけ、2008年から「改善力アップ研修」を行っています。ここでは「省エネルギー/収率向上/品質向上/合理化」をテーマに、自ら課題を抽出して解決を図るプロフェッショナル人材の養成を目標に、1年をかけてQC手法と改善活動の進め方を習得。翌年に改善実践を行い、毎年12月に工場長や担当役員が出席する報告会で成 果を披露します。
さらに2012年から改善スキルを他の従業員に指導・教育するインストラクター養成を目的に、研修修了者を対象とする「改善活動インストラクター研修」を開設。2017年度までに関連事業所の参加者を含む450人が修了し、その15%(7人のうち1人)がインストラクターの資格を得て省エネルギー等の改善活動の推進力となっています。
TOPICS
「省エネ分科会」による水平展開とさらなる活性化
DICでは、各事業所の原動グループ(エネルギー供給・用水供給・廃水処理を担う部署)のリーダーが一堂に会して「原動連携ワーキンググループ会議(WG)」を四半期ごとに開催しています。その活動の大きな柱となっているのが「省エネ分科会」です。
ここでは本社の生産管理部員も交え、①省エネ活動のポイントをまとめた「省エネ推進マニュアル」の整備、②「省エネ好事例集」の編纂、③新たな「省エネアイテムの発掘」とトライアル、④低炭素化促進のための「再生可能エネルギーの導入検討」、⑤全事業所を対象にした「省エネ診断」の実施に取り組んでいます。
省エネ推進マニュアルには、エネルギーの見える化、推進体制、計画策定、管理標準の整備、エネルギーパフォーマンス指標の考え方、省エネ投資基準の考え方、PDCA手法による進捗管理などを明記し、全社マニュアルとして各事業所で運用しています。省エネ診断では、まず、「省エネ推進マニュアル」に照らして実態を数値化しレーダーチャートに表します。そこで浮き彫りになった弱点に対して改善提言を行い、対策の具現化までフォローアップしていくもので、この改善提言を担当者だけでなく本社関係部門や工場長にも共有して改善を実行することがポイントです。当面はこの省エネ診断からの省エネ展開を通じて全社の底上げを図っていくとともに、今後はリスクマネジメントに基づくBCP(事業継続計画)の視点も診断項目に取り入れ、海外生産拠点にも展開していきます。
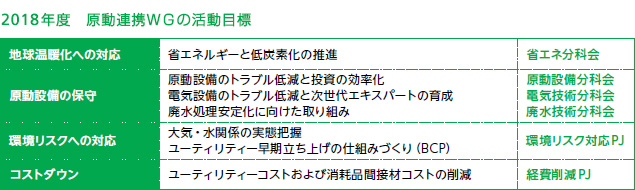
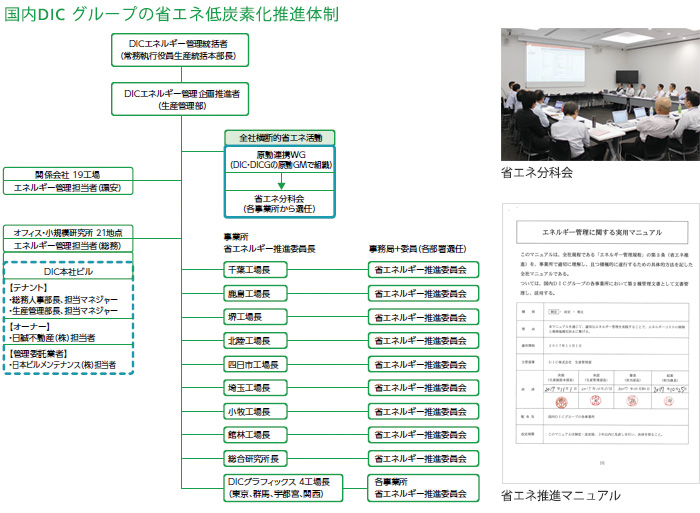
【診断と対策事例】 熱画像による「熱漏れ点検」でムダな放熱を削減
ボイラの蒸気バルブなどは保温対策が施されていない場合が多く、ムダな熱放散があります。そこで、赤外線サーモグラフィを使って熱漏れを見える化。着脱可能な保温ジャケットを取りつけるなどすれば熱エネルギーの損失を防げます。
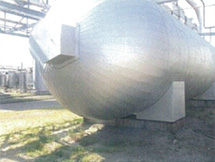
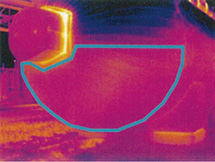
【省エネ診断】 強み・弱みを見える化して改善をアドバイス
省エネ診断では、分科会のチームが工場に出向いて入念にチェックし、レーダーチャートで強み・弱みを見える化し、改善のヒントを提示します。その際に、その現場ならではの優れた取り組みを発見することも多く、好事例として水平展開しています。
VOICE
我が職場のあたり前が、他工場の先進事例に
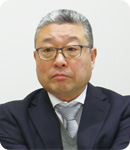
「省エネ診断」で様々な工場を訪問しますが、ある工場があたり前に行っている取り組みが、他の工場から見ると非常に斬新な視点であったりします。診断は粗探しではなく、新たな気づきやヒントを得る宝探しのような活動です。優れた事例を水平展開することで省エネ・コストダウン・リスク低減という成果に直結するため、それが分科会メンバーの大きなモチベーションとなっています。
工場のエネルギーを管轄する原動部門は、目立たない縁の下の力持ち的な存在でしたが、省エネ分科会の活動によってグループ内で存在感を増しています。これまでに蓄えた知見は、海外の工場でも温暖化防止の切り札の一つになると確信しています。
生産管理部 エネルギー管理担当マネジャー 阿部 智
05再生可能エネルギーの導入推進による化石エネルギーの消費削減
国内DICグループにおける再生可能エネルギーの殆どすべてが、鹿島工場の再生可能エネルギー設備(バイオマスボイラ、風力発電、太陽光発電)から生み出された自然エネルギーです。国内DIC グループで消費するエネルギー(熱・電気)のうち、10.3%は再生可能エネルギーで賄っており、2017年度の実績は497千GJ(原油換算量12,818㎘)と前年度比で21%増加しました。
再生可能エネルギーが前年より増加した要因は、バイオマスボイラの安定運転とエネルギーソース(バイオマスボイラ、風力 発電、太陽光発電、CGS、買電)のこまめなベストミックス運転が奏功した結果です。
今後もCO2排出量削減の有効な手段の一つとして、再生可能エネルギーを積極的に導入してまいります。
国内消費エネルギーの10.3%を再生可能エネルギーで
DICグループでは、条件の適した事業所で自家消費用に再生可能エネルギーを積極的に導入しています。もっとも寄与率が高い鹿島工場の木質チップ燃料によるバイオマスボイラ(発電能力4,000kW+発生蒸気30t/h)と、風力発電(能力:2,300kW×2基)、太陽光発電(100kW)を合わせ、購入電力・コージェネレーションシステム(CGS)・再生可能エネルギーによる電源構成のベストミックスに取り組んでいます。
この結果、2017年度の再生可能エネルギー利用量は前年度比21%増加し497千GJ(国内DIC グループエネルギー消費量の10.3%)となり、再生可能エネルギーによるCO2排出量の削減効果は30,791tとなりました。
2018年1月、鹿島工場では新たに出力1,600kWのメガソーラー(面積13,772㎡に278Wの太陽光パネル5,588枚設置)が竣工し、稼働を開始しました。
また、合成樹脂を生産する北陸工場(石川県)では、2018年1月に新規に木質チップを燃料とするバイオマスボイラを導入し、液化天然ガスボイラの一部をこれに切り替え、工場のCO2排出量を約12%削減します。
なお、前述のCGSを含む自家発電量は7,014万kW(前年度比9.0%増)に達し、DIC国内グループの全消費電力量の25.6%を占めるまでになりました。
さらに購入電力についても、調達先の見直しに着手し、CO2排出係数の低い電力を供給する事業者から優先的に電力を調達する「購入電力のグリーン化」にも取り組んでいます。
06コージェネレーションと再生可能エネルギーによる自家発電力の向上国内消費電力の23%をコージェネレーションシステムで
国内DICグループでは、エネルギーの効率化と自然災害などのリスクに備えるため、コージェネレーションシステム(CGS)の計画的な導入と再生可能エネルギーの活用による「自家発電力の向上」に努めています。
コージェネレーションは燃料を燃やしてタービンを回し、発電と同時に廃熱(蒸気・温水)を回収利用してエネルギー効率を高めるシステムです。国内DICグループでは、千葉工場・埼玉工場・群馬工場に続いて、2015年に鹿島工場(茨城県)に天然ガスタービン方式のCGS(1,700kW)を導入しています。
また、2017年4月に千葉工場のCGSを高効率型に更新(5,300⇒3,375kW)して現状に見合った最適容量化と省エネ化(約5%効率向上)を実現しました。
これらの施策により国内におけるCGSの最大発電能力は計1.4万kWとなり、2017年度の発電量実績は4,427万kWで国内消費電力の約16%を賄いました。前述の再生可能エネルギーで発電した電力量を含めると、国内DICグループで消費する電力の23%を自家発電で賄っています。
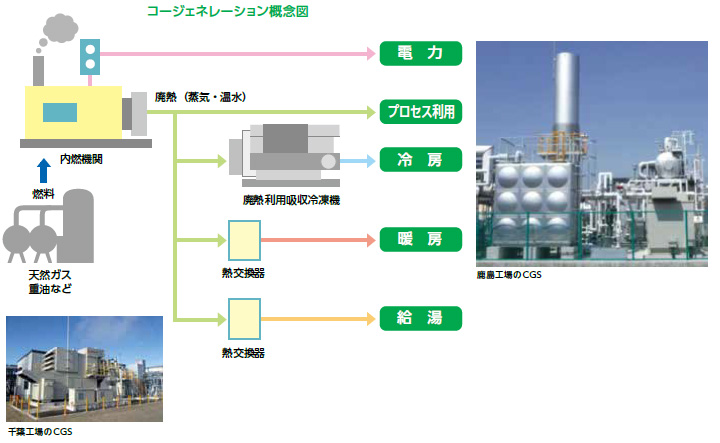
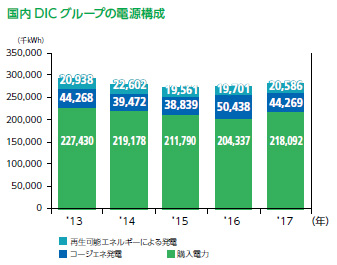
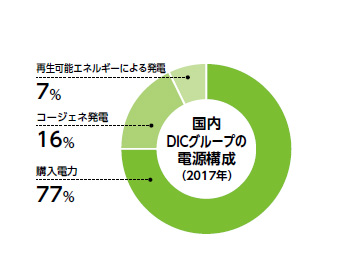
07海外DICグループにおけるCO2排出量とCO2排出原単位
2017年度の海外DICグループは、生産数量が前年度比0.5%減少しました。その中でエネルギー使用量は同4.6%減少(7,065⇒6,740千GJ)し、エネルギー消費原単位も同4.1%減少(6.746⇒6.469GJ/t)しました。
また、CO2排出量も同6.4%減少(417,184⇒390,346t)し、CO2排出原単位も同6.0%減少(398.4⇒374.6kg-CO2/t)しました。
CO2排出量が減少した要因は、①各社がDICグループのCO2排出量削減目標をブレークダウンして省エネ低炭素化活動を推進したこと。②中国においては「海南DICのバイオマスボイラ」と「青島DIC精細化学の太陽光発電設備」の稼働が寄与したこと。③アジアパシフィックにおいてはPT DIC Graphicsカラワン工場(インドネシア)での「石炭燃料の一部をヤシ殻燃料に置換」したこと。④欧米では「太陽光発電設備の追加導入や生産効率化のさらなる取り組み」などが大きく寄与しました。
海外における省エネルギー活動の推進
海外DICグループでは、各国・地域のインフラ事情や法規制が異なる中で、化学工業界の先進的な事例となるようエネルギーの削減・効率的な運用に取り組んでいます。
海外DICグループの事業所では徐々に省エネ活動が醸成してきており、①生産効率化、②ベースロードの削減、③設備更新時における高効率機種の選定、④照明のLED化推進など、省エネ活動が活発化しています。
加えて、前述したように再生可能エネルギーの導入も徐々に進展し、2018年度以降の新規案件も現在数件検討中です。
例えば発電効率の高い地域での太陽光発電設備の設置、石炭燃料のヤシ殻燃料への転換率の向上が2018年度の主要項目です。
今後もDIC本社と海外DICグループ会社の連携をさらに強化し、地球温暖化防止に注力していきます。
海外における省エネルギー活動
アジアパシフィック
アジアパシフィック(AP)地区には23事業所があり、DICグループCO2総排出量の19%のウエイトを占めています。AP地区における2017年度のCO2排出量実績(前年度比)は、生産数量が3%増加した中で6%減少しました。その主要因は、①インドネシアの顔料生産事業所での燃料転換率向上(石炭の10%をバイオマス燃料であるヤシ殻に転換)と省エネプロジェクトの実施②インドのインキ生産事業所での燃料転換(軽油⇒天然ガス)および省エネ活動③インドネシアのソリッドコンパウンド生産事業所やオーストラリアのインキ生産事業所などでの省エネ活動の効果です。
なお、基準年(2013年度)対比では、生産数量が16%増加した中でCO2排出量は6%の増加にとどまりました。
AP地区では毎年シンガポール(DIC-APオフィス)で、各国のESH代表者と本社担当者(RC部、生産管理部)によるAP地区ESHカントリーヘッド会議を開催しています。この会議では、主に安全・環境面の次年度活動方針の説明と具体的な活動計画のすり合わせを行います。
その中で、2018年度の地球温暖化防止の取り組み方針(省エネ・低炭素化の削減目標)について説明し、具体的な活動計画を決定しました。DIC本社はCO2排出量削減目標達成に向けてAP地区に対して①各事業所省エネ計画の立案と実行、②省エネ診断の継続実施(省エネテーマの発掘と実行支援)、③エネルギー管理の実用マニュアルと省エネ事例集の展開(管理定着と水平展開が当面の目標)、④条件の適した事業所を対象にした省エネ・低炭素化プロジェクトの立ち上げを促し、その支援を行っていきます。
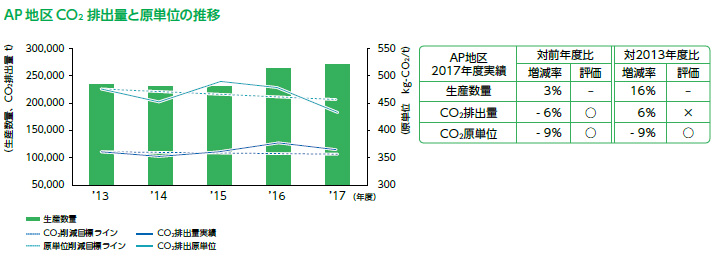
中国
中国地区には18事業所(研究所含む)があり、DICグループCO₂総排出量の10%のウエイトを占めています。中国地区における2017年度のCO2排出量実績(前年度比)は、生産数量が2%増加した中で3%減少しました。その主要因は、①スピルリナを製造する海南DIC微藻でのバイオマスボイラの稼働効果、②青島DIC精細化学での太陽光発電導入(400kW)、③中山DIC色料等の事業所における省エネ活動の効果です。
なお、基準年(2013年度)対比では、生産数量が1%増加した中でCO2排出量は16%と増加しました。増加の主原因は、①この数年でエネルギー多消費型製品(液晶材料等)が増加②研究施設の増床やクリーンルーム稼働など生産に寄与しないベースロードエネルギー消費の増加③エンジニアリングプラスチック製品の新プラント稼働などが大きく影響しました。
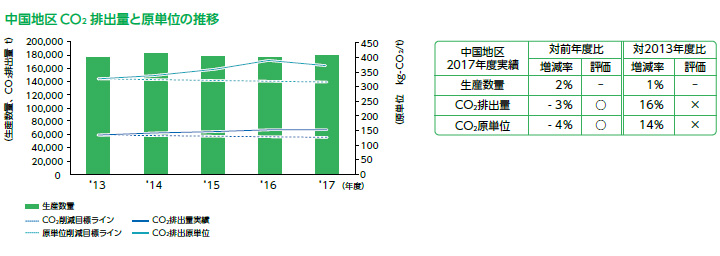
AP・中国地区の事業所でも導入が進む再生可能エネルギー
世界的な脱炭素社会への潮流を背景に、アジアパシフィックや中国においても再生可能エネルギーの普及に力を注いでいます。この地域に展開するDICグループ各社は、各国の助成・支援制度も活用しながらバイオマスボイラや太陽光発電などの導入に取り組んでいます。
インドネシア PT. DICGraphics
石炭に代わる燃料でCO2を削減する「ヤシ殻プロジェクト」
PT. DICGraphicsカラワン工場は、食品パッケージ用インキや塗料・プラスチック等に多用される顔料の主力工場で、多くの熱エネルギー(ボイラ)と洗浄水を使用しています。主な燃料は石炭で、これは経済性(重油価格の1/5、天然ガスの1/3)と入手しやすさによるものです。しかし、カラワン工場だけでDICグループ全体のCO2排出量の1割を占め、生産数量も上昇し続けているため省エネ・低炭素化が重要課題でした。
そこでDIC本社とカラワン工場はCO2排出量削減プロジェクトを発足し、石炭に代わる燃料として「ヤシ殻」に着目しました。インドネシアは世界第二のパームオイル生産国で、オイル抽出後のヤシ殻が豊富にあり、日本にも輸入されて石炭火力発電所やバイオマス発電の燃料として活用されています。プロジェクトチームがヤシ殻を調べてみると、1kgあたりの熱量は約5,000kcalと、カラワン工場で使う石炭のカロリーと同等なことが分かりました。そこで2016年12月、ヤシ殻を粉砕した石炭に混ぜて燃焼テストをしてみると、2割程度の混合であればボイラの運転や燃焼灰の品質(燃焼灰はセメント骨材に再利用)に影響がないことを確認できました。
2017年1月から、使用する石炭の1割をヤシ殻に置換して本格燃焼を継続しました。その結果カラワン工場の生産数量が前年比1.3%増加した中で、CO2排出量は8.5%減少したことが確認されました。ヤシ殻燃焼の効果を検証した結果、2017年度は5,000tのCO2を削減したことになります。この削減量は前年度DICグループの、CO2総排出量の0.8%減に相当します。2018年度はヤシ殻燃焼量を1割から2割に増やす計画で、現在、燃焼調整などに取り組んでいます。
タイ サイアムケミカル社
太陽光発電設備を新設してCO2を削減
サイアムケミカル社は、合成樹脂など多様なポリマ製品を製造し、特に塗料用アクリル樹脂は自動車の生産増加に伴い需要が高まっています。また、タイでは天然ガス火力発電から電源の多様化を図るため、税制優遇措置を設けて再生可能エネルギーの普及に力を注いでいます。こうした中で、同社はサムットプラカーン県の工場建屋・倉庫に発電能力704kW(年間発電量:1,049MWh)の太陽光パネルを設置。2017年7月から稼働を開始し、電力を製造現場やオフィス用に活用しています。これにより2017年度は電力使用量の16%を太陽光発電で賄い、年間換算580tのCO2排出量を削減しています。
中国 DIC海南迪愛生微藻
軽油からバイオマスボイラに切り替え
海南DICは、藻の一種「スピルリナ」を生産し、栄養補助食品(スーパーフード)や天然着色料として加工しています。その製造工程で必要な蒸気を得るため、従来は軽油によるボイラを使用していましたが、2016年10月、ゴムの木の間伐材を燃料とするバイオマスボイラに切り替えました。
2017年には年間を通じてフル稼働し、工場のCO2排出量1,000t/年を削減し(年間CO2排出量の40%)、中国地区全体のCO2排出量の1.5%分の削減に寄与しました。
中国 青島迪愛生精細化学
太陽光発電で大幅に省エネ&CO2削減
計画的・継続的に設備更新や工程改善を推進
設備の最適化で冷凍機の消費電力を大幅に節減 【DIC合成樹脂(中山)】
中山DICの金属石鹸製造工場では、冷凍機の消費電力が工場全体の3割を占めています。その内訳は、距離の離れた原動機によって供給する冷却水、冷凍機の稼働時に全開作動する給水ポンプです。
これらを効率的に稼働させるため、2015年5月にプロジェクトを立ち上げ、工程・設備の見直しと改善策を検討しました。そして、冷凍機の近くに冷却水を循環再利用するクーリングタワーと冷却水の給水ポンプを新設し、冷凍機のコンプレッサーと冷凍水の給水ポンプを連動させて、冷凍水の温度調整を自動化。こうして2016年1月から本格運用を開始し、約32万kWh/年の消費電力を約12万kWh/年へ大幅に節電しました。
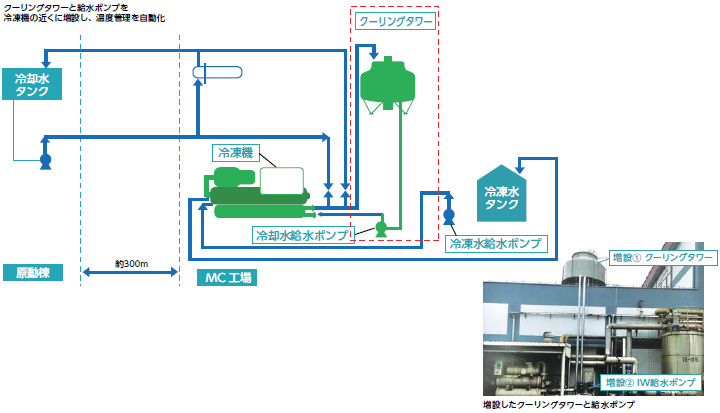
樹脂ワニス工場廃液の燃焼処理の余熱を有効利用【南通DIC色料】
樹脂ワニス廃液は場内焼却炉で燃焼させ、発生する排ガスは700~800℃に達します。南通DIC色料では、この熱源を有効利用するため新たに熱交換器を導入し、シャワー用温水や顔料製造工程で使う温水に再利用。電気代換算で約16.8万元/年を節約しています。
VOICE
社会の動きやリスクを見通して低炭素化に投資を
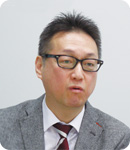
新興国の温室効果ガスの排出抑制策は、2015年の「パリ協定」採択を契機に一段と加速しています。顕著な例が優遇税制や補助金制度によって再生可能エネルギーの導入を支援し、化石燃料からの転換(脱炭素化)や資源枯渇リスクを回避するため電源の多様化に注力していることです。インドネシア政府はアジア初のグリーンボンド国債を発行して温暖化対策や環境プロジェクトの資金を調達すると表明していますが、こうした動きは企業の設備更新にも少なからず影響を与えます。
例えば工場の重要設備であるボイラを更新する場合でも、性能・コストはもちろん環境配慮・投資回収期間・助成制度の有無なども精査し、耐用年数を迎える頃に社会がどのように変化しているかまで想定して、更新のタイミングや機種を決めることが必要です。
私たちは「省エネ診断」や「省エネ推進会議」で現地法人の工場を訪問する際、経営層とこうしたテーマでも話し合います。
環境投資の回収リスクより投資しないリスクの方が大きくなりつつあるとの視点に立ち、規制強化される前に先手を打って低炭素化社会に適合する企業を目指すことがともに成長する原動力となります。そのために日本国内で培った省エネマネジメントと優良事例を海外事業所に展開する活動に一層力を注いでいきます。
生産管理部 効率化担当マネジャー(エネルギー管理企画推進者) 川口 和男
欧米
欧米(アフリカ含む) 地区には113事業所があり、DICグループCO2総排出量の32%のウエイトを占めています。欧米地区における2017年度のCO2排出量実績(前年度比)は、生産数量が2%増加した中で3%減少しました。CO2排出量が減少した主要因は、①さらなる生産集約化や生産効率化が奏功、②太陽光発電設備の追加導入、③その他省エネコストダウン活動の実施、といった施策の効果と言えます。
なお、基準年(2013年度)対比では、生産数量が± 0%でCO2 排出量は24%も減少しました。減少の主原因は、①事業の大規模な再構築による生産効率化が大きく寄与、②省エネコンサルティングなどアウトソーシング手法を用いた省エネ推進が奏功、③太陽光発電・小水力発電・ランドフィルのバイオガス活用といった再生可能エネルギーの積極導入、といったことが大きく寄与しました。
米国 サンケミカル社
着々と進む再生可能エネルギーの取り組み
サンケミカル社はOnyx Renewable Partners 社とPPA(電力購入協定) を締結し、同社のカールスタット(米国)にある研究所の駐車場の屋根およびカーポートを利用して、2,500枚以上の太陽光パネルを設置しました。Onyx社は今後20年間にわたり、916kWの太陽光発電設備を所有・維持していきます。サンケミカル社では今回設置した太陽光パネルで発電した電力を市場価格の約50%相当額で購入し、自社のコストダウン(年間100ドル/k以上)に役立てます。また「クリーンエネルギー」を使用することで、同時にカーボンフットプリントの削減を実行していきます。
太陽光パネルの設置は、2017年秋から作業を開始しました。建設工事は2018年1月に完了し、2018年3月に稼働しました。
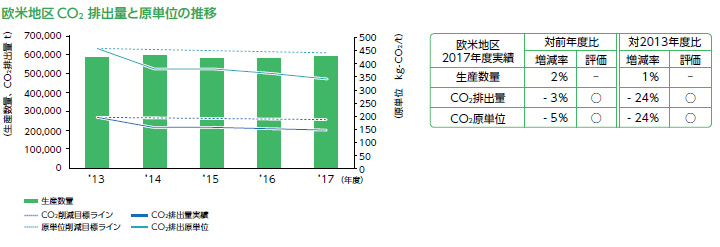
オーストリア サンケミカル社
地球エネルギー賞「水」部門で優秀賞を受賞
オーストリアのヌスドルフにあるサンケミカル社のベンダ・ルッツ工場は、トライセン川沿いの運河で2ヶ所の小水力発電所を運営しています。この2つの水力発電所は、河川沿いにある52の水力発電所のコンソーシアムの一部であり、いずれも地域のエネルギー使用量を削減することを目的として稼働しています。
オーストリアで開催された地球エネルギー賞選考において、このコンソーシアムは持続可能な水力発電の使用の観点から評価され、「水」部門で地球エネルギー賞(オーストリア南部部門)「Energy Globe Award Lower Austria」を受賞しました。サンケミカル社はコンソーシアムのメンバーとともに、表彰式で「The Ecological, Compatible Usage of Hydrodynamic Power in the Lower Part of the Traisen」(環境に配慮したトライセン川下流における水力発電の使用)と題したプレゼンテーションを行いました。今回オーストリア南部部門での賞を受賞したことで、今後は「地球エネルギーオーストリア大賞」や、さらには177ヶ国が参加する世界でもっとも名高い環境大賞である「地球エネルギー大賞」に推薦される可能性も高まっています。
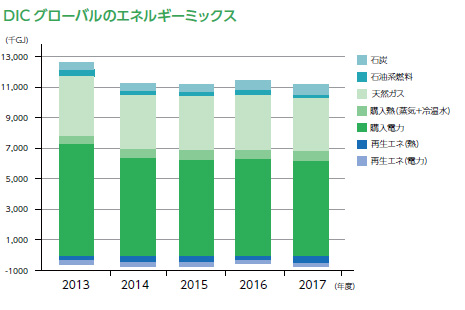
08生産活動以外の取り組み
2017年度もクールビズ・ウォームビズを励行しました。また、オフィス・事業所では古くなった照明器具や空調機器をトップランナー基準に準拠した高効率タイプにリプレイスする一方、照明の不要時消灯やエアコンの温度設定を夏28℃・冬22℃に徹底するなど、社員の省エネ意識向上にも継続的に取り組みました。
09CDPへの情報開示
CDPは国際的な非営利団体で、気候変動の抑制を目的に、機関投資家を代表して企業の気候変動に対する取り組みや重要な環境情報の開示を求め、回答を分析・評価して投資家に公表しています。グローバル大手企業約6,200社(日本は大手企業500社)がその対象で、①戦略、②温室効果ガスの排出量、③削減目標と計画、④具体的な削減活動の取り組み内容に応じて評価され、企業価値を測る重要指標となりつつあります。
DICは2010年からCDPに回答し、2017年調査で温室効果ガスの排出削減や情報開示の活動が高く評価され、2016年に続いて最上位の“リーダーシップレベル”に位置づけられる最高スコアのAに次ぐ「A-」と認定されました。今回は特にグローバルに拡大する生産活動の中で温室効果ガスの排出量削減に努めたことや情報開示の活動が高く評価されました。なお、DICではグローバルに水資源リスクへの意識が高まっていることを認識し、2017年度からCDPの「水資源管理」に関する調査への回答も開始しています。
日本企業では73社(A=13社、A-=60社)がリーダーシップに位置づけられ、素材セクターの最高スコアは「A-」(6社)でした。
今後の取り組み
今後さらにグループ全体で幅広く深くエネルギーの効率化を推進するため、新たな取り組みをスタートしています。例えば、国内グループでは原動連携WG活動の中に省エネ分科会を設置し、各生産拠点のエネルギー担当者が定期的に話し合う場を設けました。2017年度は具体的に4つの重要テーマ「①省エネマニュアルに基づく省エネルギーの推進と定着、 ②低炭素化の推進(再生可能エネルギーの積極増進)、 ③新たな省エネアイテムの探求とデモによる検証実施(小水力発電・バイナリー発電・地中熱利用等)、 ④省エネ診断実施による省エネ施策の発掘とPDCA支援」を設定し、活動を行っています。各テーマの進捗は四半期ごとに行うWG会合で確認します。こうした活動を次世代メンバーを交えて取り組みながら、省エネの専門家を育成し、グループ全体の対応力を底上げしていく計画です。
VOICE
低炭素化に向けて、点から線へ、線から面へ
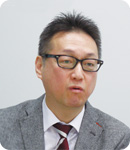
DICグループのエネルギー使用量(=CO2 排出量)の約6割は海外事業所が占め、アジアパシフィック・中国においては今後も生産拡大が予想される中で、一層の生産の効率化とエネルギーバランスの最適化が求められます。こうした中で低炭素化を推進するには、設備投資でも省エネ活動でも戦略的な視点がますます重要になってきます。好事例の水平展開はもちろん、関連部署との連携強化、各国政府の支援制度や外部ブレーンなど、人・組織・制度のリソースをフルに活用して点から線へ、さらに面へと広げ、グローバルな化学企業として、あるべき姿を追求していきます。
生産管理部 部長 向後 勇一