地球温暖化防止への取り組み(2014年度の主な活動)
2014年度の主な活動
01DICグループのエネルギー使用量とCO2排出量(グローバル)
DICでは、エネルギーの使用効率を示す数値として「原単位(生産数量トンあたりのエネルギー使用量)」を重視しています。2014年度のDICグループは、生産量が前年比7.3%減少する中で、エネルギー使用量を10.5%(原油換算:322,210kℓ⇒288,452kℓ)、エネルギー原単位を3.4%(153リットル/t ⇒148.43リットル/t)それぞれ削減しました。
また、CO2排出量は9.1%(722,955t⇒ 657,457t)の大幅な削減を達成しました。これは世界各国・地域の工場・事業所が、燃料の転換や高効率設備の導入を図るとともに、工程の改善や設備稼働率の向上などエネルギーロスを最小化する地道な省エネ活動に積極的に取り組んだ成果です。
02国内におけるエネルギー使用量とCO2排出量
国内DICグループ(DIC+グループ会社の33事業所)は、生産量が前年比3.6%減少し、エネルギー使用量も1.4%減少しました。しかし、エネルギー原単位は2.3%増加しました。要因は少量多品種化によるエネルギー使用効率の悪化や、品質対策としてクリーンルーム設置によるベースロードの増加が挙げられます。一方、CO2排出量は、2014年度より非エネルギー起源(廃棄物燃焼分)のCO2排出量を含めたことで前年比4.4%増加しましたが、2013 年度と同じベースで比較した場合0.3%の減少となりました。
原単位増加の主な要因
原単位増加の主要因として、一般的な樹脂生産に比べてエネルギー投入を要するPPS樹脂(エンジニアリングプラスチック)を製造する鹿島工場の新プラントが本格稼働したことが挙げられます。
国内DICグループのCO2排出量の増減要因まとめ
主な増減要因 | CO2排出量 (トン) |
ウエイト※ | 備 考 |
---|---|---|---|
省エネ施策取り組み効果 | -6,883 | -2.8% | 国内省エネ施策488件に取り組み、2,677㎘のエネルギーを削減 |
構成要素の変化 | -3,250 | -1.3% | 関係会社の事業譲渡など |
鹿島再生可能エネルギー設備稼働増加 | -3,184 | -1.3% | 再生可能エネルギー(バイオマスボイラー ・ 風力)による熱、電気エネルギー の発生量増加(2014年14,919㎘、前年比11%増) |
生産数量減少 | -1,740 | -0.7% | |
その他要因 | 5,990 | 2.5% | |
鹿島工場PPSニートレジン新プラント本格稼働 | 8,148 | 3.3% | エネルギー原単位が高いプラントの本格稼働 |
非エネルギー起源CO2排出量を2014年から加算 | 11,566 | 4.7% | 2013年度までは千葉工場のみカウントしていたが、 2014年度より国内全事業所対象とした |
合 計 | 10,648 | 4.4% |
03国内における省エネルギー活動
国内DICグループでは、下記のような省エネルギー施策を推進し、顕著な成果をあげました。
各事業所(工場・研究所)では、生産の集約化や蒸気ボイラーの更新などによる熱エネルギーの削減、空調の冷媒や稼働時間の見直しによる電力の節減、圧縮エア向けコンプレッサーの効率運転化や照明設備のLED化などによる電気の削減など多種多様な省エネ活動を488件実施しました。加えて鹿島工場ではボイラー燃料のクリーン化(重油から都市ガスへの転換)を実施しました。これらの活動により2014年度は原油換算で2,677㎘ (CO2排出量6,883t)のエネルギーを節約しました。これは200ℓのドラム缶1万3,385本分に相当し、2013年度の国内DICグループが使用したエネルギー総量の2.8%にあたります。
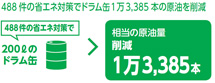
488件の省エネ対策でドラム缶1万3,385本の原油を削減
国内DIC グループの省エネルギー取り組み実績
区 分 | 取り組み件数(件) | エネルギー 削減量(㎘ / 年) |
CO2削減量 (t-co2/ 年) |
---|---|---|---|
DIC単体 | 406 | 2,175 | 5,859 |
国内グループ会社 | 82 | 502 | 1,024 |
国内DICグループ 計 | 488 | 2,677 | 6,883 |
「エネルギーの見える化システム」を導入拡大
DICでは、設備ごとにエネルギー使用量をリアルタイムで計測・監視し、ムダ・ムラをなくして最適化を図る「見える化システム」を構築。北陸工場(2012年省エネルギーセンター会長賞)をはじめ各事業所に水平展開を図っており、2014年度はさらに小牧工場へ水平展開を図りました。また、前年に引き続き品種やロット毎のエネルギー使用量を工程別に解析できる見える化システムを堺工場B現場に導入(昨年は千葉V現場、鹿島C現場導入)し、エネルギーのさらなる合理化を推進しました。(現在、四日市工場でも導入検討中)
また、サプライチェーンを通じたCO2間接排出量(Scope3)※については、2012年度に1項目(輸送、配送(上流))から取り組みを進め、2013年度から資本財、事業から出る廃棄物、出張などの項目を加え、調査回答範囲を6項目に広げて対応しています。
- Scope3:製造、輸送、出張、通勤等の際に、企業が間接的に排出する、サプライチェーンでの温室効果ガスの排出量。
TOPICS1
「改善力アップ研修」で省エネ・品質向上などを推進
DICでは、生産に関わる従業員一人ひとりの高い意識や改善スキルの向上こそ現場力の強化に直結すると位置づけ、2008年から「改善力アップ研修」を行っています。ここでは「省エネルギー/収率向上/品質向上/合理化」をテーマに、自ら課題を抽出して解決を図るプロフェッショナル人材の養成を目標に、1年をかけてQC手法と改善活動の進め方を習得。翌年に改善実践を行い、毎年12月に工場長や担当役員が出席する報告会で成果を披露します。
さらに2012年から、習得したスキルを他の従業員に指導・教育するインストラクターの養成を目指し、研修を修了した受講生を対象とする「改善活動インストラクター研修」を開設しました。2014年度までに関連事業所の参加者を含めて332名が研修を修了し、このうち2割がインストラクターの資格を得て省エネルギー等の改善活動の推進力となっています。
「問題を読み取る力」の重要性を再認識
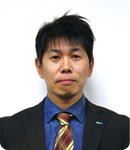
研究報告会で分かりやすいデータ分析には説得力があると感じました。独創的な観点からの解析を活かした発表内容には思わず引き込まれ、改めて「問題を読み取る力」の重要性を再認識しました。今回の経験を踏まえ、さらに改善活動の向上に取り組んでいきます。
小牧工場 ソリッドコンパウンド製造部 製造課班長 内藤 浩一
TOPICS2
空調機の新たな省エネ対策で消費電力量を約20%削減
生産部門研究発表会で注目された2つの取り組み
省エネ法改正により電力需要の平準化が求められるようになり、最大電力を押し上げる大きな要因である空調機器の省エネルギー化が重要課題となっています。しかし、従来の方法では限界があり、各事業所では新たな施策を模索していました。そんな時、千葉工場(千葉県)で試験導入した「冷媒ガス」の能力向上に着眼した2つの手法が大きな効果をあげ、毎年1月に開催している「生産部門研究発表会」で関心を集めました。
① フロンから自然冷媒へ入れ替え
1つは、現在使っているフロンガス(R-22)を抜き取り、エネルギー効率の高い自然冷媒のプロパン(イソブタンと同類)に入れ替える方法です。プロパンは「オゾン層への影響がなく温暖化係数も低い」という特性の一方で可燃性という欠点があります。そのため「化学工場へ導入するにはリスクが高い」と敬遠されてきましたが「家庭用ノンフロン冷蔵庫の冷媒にイソブタン採用されている」という事実に注目。部署によっては導入も可能と判断し、2014 年に堺工場で試験稼働したところ消費電力量を約20~30%削減できました。
国が2020年にR22など温暖化係数の高いフロンガスの生産・消費を全廃という目標を掲げ、空調機器の自然冷媒化を模索していることもあり、試験導入の検証をもとに鹿島工場にも部分的に導入しました。今後は各事業所で条件の合う場所への水平展開を図っていく計画です。
② 気泡を除去して効率アップ
もう1つは、既存冷媒の能力を活性化する方法です。冷媒は圧縮・膨張を繰り返す過程で熱交換によって冷暖房を行いますが、経年劣 化のため圧縮時に気泡が発生し、冷媒能力が低下します。そこで、この気泡を分離・除去することで本来の冷媒能力を取り戻す仕組みです。千葉工場の空調機に気泡分離装置を取り付けて運転したところ、空調能力が大幅に改善され、電力のデマンド制御によるピークカットが推進でき、消費電力量を約20%削減しました。2015年度は小牧工場をはじめ複数の事業所に水平展開する計画です。国内DICグループの各事業所は、 今後この2種類の方式を併用して生産部門の省エ ネルギー活動をさらに加速する計画です。
04コージェネレーションと再生可能エネルギーによる自家発電力の向上
コージェネレーションシステム(CGS)による自家発電
国内DICグループでは、エネルギーの効率化と自然災害などのリスクに備えるため、コージェネレーションの計画的な導入と再生可能エネルギーの活用による自家発電力の向上に努めています。コージェネレーションは燃料を燃やしてタービンを回し、発電と同時に廃熱(蒸気・温水)を回収利用してエネルギー効率を高めるシステムです。
現在、国内DICグループでは千葉・滋賀・埼玉・群馬・東京の5工場に計1.9万kW(最大能力)のCGS を擁し、2014年度は国内消費電力の14%をまかないました。今後、2015年秋に鹿島工場(茨城県)に天然ガスによるガスタービン方式のCGS(1,700kWh)を増設し、2016年は千葉工場でもCGS(6,000kWh)の設備更新を検討しています。
再生可能エネルギーの活用
国内DICグループでは、条件の適した事業所で再生可能エネルギーの積極的な導入(バイオマスボイラー、風力発電、太陽光発電)を図っています。
2014年度は、鹿島工場におけるバイオマスボイラー(能力:発電電力4,000kW+発生蒸気30トン/h)の燃料となる木質チップの品質向上とメンテナンス強化により稼働率を大幅に向上させ、蒸気発生量(熱エネルギー)と発電電力量が増加しました。また、風力発電設備(能力:2,300kW×2基)の稼働向上や小規模ながら太陽光発電(100kW)も寄与したため、再生可能エネルギー発電量を前年比7.9%増加させました(国内DICグループ消費電力量の8%)。この結果、2014 年の再生可能エネルギーによるCO2排出量を3万9,735トン削減 (前年比11%向上) しました。
今後は鹿島工場で培ったバイオマスボイラーの運転管理技術を活かし、2016年に北陸工場(石川県)への導入拡大を計画しています。
国内DIC グループ |
消費電力量 | コージェネレーション 発電量 |
コージェネレーション 発電構成比 |
再生可能 エネルギー発電量 |
再生電力構成比 |
---|---|---|---|---|---|
2013年度 | 292,637千kWh | 44,268千kWh | -15.1% | 20,938千kWh | 7.2% |
2014年度 | 281,257千kWh | 39,472千kWh | -14.0% | 22,602千kWh | 8.0% |
前年差 | -11,380千kWh | -4,796千kWh | -1.1% | 1,664千kWh | + 0.8% |
前年比 | - 3.9% | -10.8% | + 7.9% |
TOPICS3
環境負荷低減に配慮した生産プロセス「マイクロリアクター」
化学合成品の多くは原料投入・反応・副生成物や不純物の回収を順に行うバッチ式のタンク型反応容器を使って生産してきました。この方式は熱交換効率が低いために加熱・冷却に大量のエネルギーが必要で、また、精密な温度制御が難しく、反応効率や品質を制御する上で課題がありました。これを克服するため研究されているのが「マイクロリアクター」という革新的な生産プロセスです。
「マイクロリアクター」は、 熱交換効率の高い微細な流路の中で、原料投入・反応・副生成物や不純物の回収を同時に行う連続フロー式の装置で、エネルギー消費を大幅に抑え、精密な温度制御による反応収率アップや品質の向上が図れ、廃棄物も削減できます。また、安全性などの点からバッチ式タンク型反応容器では困難だった物質の反応・合成も行いやすく、プラント建設の短期化をはじめとした様々な効果が期待できます。
DICでは、「マイクロリアクター」の可能性に早くから注目し、実用化の研究を進めてきました。2013年9月に北陸工場(石川県)において、フッ素系界面活性剤の生産プロセスに採用し、反応効率アップにより生産時間を1/9に短縮し、エネルギー消費量を削減するとともに、工程廃棄物発生をゼロにするなど大きな成果を得ています。
多種多様な化学合成品を開発・製造するDICにとって、品質向上と環境負荷低減の両立を図る生産プロセスの革新は重要なテーマと考えています。今後もサステナビリティの実現に向けて、DICは環境負荷低減に配慮した生産プロセスへの取り組みを積極的に進めていきます。
05海外におけるエネルギー使用量とCO2排出量
2014年度の海外DICグループのエネルギー使用量は原油換算で176.6千㎘(前年度比15.4%減)となり、CO2排出量は40万2,343t(前年度比15.9%減)となりました。大幅な減少要因は、バウンダリーの変化(約5%減)による減少要因もあげられますが、エネルギー原単位の改善(前年比5.7%削減)が物語るように、グループを挙げた省エネ活動の強化や高効率を考慮した設備更新に注力し、生産におけるエネルギー効率を高めた成果だといえます。
06海外における省エネルギー活動の推進
海外DICグループでは、各国・地域のインフラ事情や法規制が異なる中で、化学工業界の先進的な事例となるようエネルギーの削減・効率的な運用に取り組んでいます。2014年度は、海外における生産量が前年比10.3%減少する中で、多様な省エネ施策の取り組み推進によってエネルギー使用量を15.4%削減し、エネルギー原単位を5.7%改善しました。この結果、CO2排出量を15.9%(76,235t)と大幅に削減しました。
2015年度もDICと海外DICグループ会社は、さらに連携を密にして地球温暖化防止に取り組みます。
海外における省エネルギー活動実績
地 域 | 取り組み件数(件) | エネルギー削減量(㎘ / 年) | CO2削減量(t-co2/ 年) |
---|---|---|---|
中 国 | 26 | 374 | 842 |
アジアパシフィック地区 | 61 | 885 | 1,960 |
合 計 | 87 | 1,259 | 2,802 |
中国
2014年11月、中国地区16事業所のエネルギー担当者など26名が合成樹脂の生産拠点「張家港迪愛生化工」(江蘇省張家港市)に一堂に会し、「省エネルギーと排水処理」をテーマに、取り組み事例の紹介や課題の共有、今後の計画について話し合いました。DIC生産管理部からは日本におけるLED照明や圧縮エアー用コンプレッサーの効率運転などの事例を発表し、高い関心を集めました。
また、中国では環境対策の一環として、軽油から都市ガスへの転換や植物から精製したバイオディーゼルの活用を企業に促しています。こうした中で、DIC中国ではインフラや立地条件などを見極めながら化石燃料由来のエネルギー削減を図っており、2013年には印刷インキを生産する「上海DIC油墨」(上海市)がバイオディーゼル(植物由来含有率2%)の使用を開始し、2014年度にはボイラー燃料の90%をバイオディーゼルに置き換えました。
その他の主な取り組み
中山DIC色料有限公司
深圳深日油墨有限公司
ボイラー燃料を軽油から天然ガスに置換
南通迪愛生色料有限公司
シャワー水の熱源(電気ヒーター)を排ガスボイラーの排熱回収に変更
張家港迪愛生化工有限公司
冷凍機と循環ポンプの効率向上
アジアパシフィック
2013年9月、アジア地区11ヶ国19事業所のエネルギー担当者25名が一堂に会して、エネルギー管理に関する課題や対策などを話し合う会議を開催。経済発展に伴う新興国のエネルギー消費量が増加する中で、地域固有の課題から有用な対策の水平展開などを幅広く議論しました。
2013年度からM&Aにより新たな生産会社が加わり、生産量全体としては増大していますが、2014年度は各拠点で積極的に省エネの取り組みを進め、1,960t-CO2/年を削減しました。
2015年度は主要なエネルギー消費拠点に焦点を当てた戦略を実施し、CO2を排出するエネルギー源からの依存低減に向け、条件の適した生産拠点では再生可能エネルギー発電の設置を行い、アジアパシフィック全体で目標設定を設けて取り組んでいきます。
その他の主な取り組み
Siam Chemical Industry Co., Ltd.(タイ)
① 冷却水ポンプを高効率型に更新
② 照明機器の更新(LED灯採用)
PT DIC ASTRA Chemicals(インドネシア)
① 工場全箇所に電気監視システムを設置
② 照明機器の更新(LED灯採用)
DIC Epoxy (Malaysia) Sdn. Bhd.(マレーシア)
冷水ポンプ(計5台)のインバータ制御化
DIC Graphics (Thailand)(タイ)
① 冷却水ポンプのインバータ制御化
② 照明機器の更新(LED灯採用)
DIC Compounds (Malaysia) Sdn. Bhd.(マレーシア)
照明機器の更新(LED灯採用)
DIC Fine Chemicals Private Limited(インド)
エリアを全対象に照明機器の更新(LED灯採用)
米 国 ・ 欧 州
北米・中南米13ヶ国、欧州43ヶ国で事業展開するサンケミカルグループは、2013年10月にWeb ベースの環境データ収集システム「Eco Track」を構築し、153拠点のエネルギー・水・廃棄物・安全に関するデータの一元管理をスタート。各所の生産情報・省エネ等の取り組み施策・CO2排出量などの見える化を図り、情報の共有化と有効施策の水平展開を推進しています。2014年度は、このシステムの本格運用によって、データの見える化⇒解析⇒改善策の創出⇒水平展開のサイクルが加速し、省エネ活動もめざましい進展をみせました。
中でも、2ヶ所の生産拠点で各種製造装置にセンサーを取り付けてソフトウェアで解析し、工程ごとにムダのない電力供給量や稼働時間を割り出すなどして生産の最適化を図りました。この結果、生産量が増加する中で最大電力消費量が大幅に抑制でき、省エネルギーとコスト削減で大きな成果をあげました。
VOICE
モチベーションを高める新たな仕組みづくりを検討
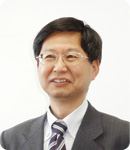
これまでエネルギーの効率化を促すため、製品生産量あたりのエネルギー投入量を示す「原単位」を重要な指標としてきました。しかし、化学品業界では製品の高付加価値化や多品種少量生産が当たり前になり、原単位だけでは生産現場の努力を評価しづらくなっています。そのため、2015年に策定する次の3ヶ年計画では、コスト低減に直結する省エネ活動の重みづけを再評価し、従業員のモチベーションを高めるような新たな仕組みづくりを検討します。
生産管理部 部長 内山 三智男
7.輸送時に関わる温室効果ガス排出量の削減
上流においては、輸送拠点における輸送調査に基づき、効率の悪い拠点の洗い出しと比較的短距離の地場配送の改善策を実施しました。 その結果、輸送量は前年比で4.2%増加する中でエネルギー使用量は2.0%減少、CO2排出量は5.0%減少しました。
減少した要因の1つにモーダルシフト(船舶・鉄道・航空機)の増加(前年比23.2%増加)があげられます。モーダルシフトの内訳としては、船舶の輸送量が同7.1%増加に対して鉄道が40.4%と大きく増加しました。
モーダルシフト化率は前年の9.1%から10.7%に向上しました。
08生産活動以外の取り組み
2014年度もクールビズ・ウォームビズを励行しました。また、オフィス・事業所においては、古くなった照明器具や空調機器をトップラ ンナー基準に準拠した高効率タイプのものにリプレイスする一方、照明の不要時停止やエアコンの温度設定を夏場28℃・冬場22℃に徹 底するなど、社員の省エネ意識向上にも継続的に取り組みました。
09カーボン・ディスクロージャー・プロジェクト(CDP)への情報開示
CDPは国際的な非営利団体で、気候変動の抑制を目的に、機関投資家を代表して企業の気候変動に対する取り組みや重要な環境情報の開示を求め、回答を分析・評価して投資家に公表しています。世界のトップ企業約6,000社(日本は大手企業500社)がその対象で、① 戦略 ② 温室効果ガスの排出量 ③ 削減目標と計画 ④ 具体的な削減活動の取り組み内容に応じて評価され、企業価値を測る重要指標となりつつあります。
DICは2010年からCDPに回答し、2014年度は情報開示度・パフォーマンス(取り組み実績)とも日本のマテリアル企業の平均評価(78B)を大幅に上る「89B」(情報開示度89点、パフォーマンスBクラス)と評価されました。
VOICE
エネルギーの本格的な自由化を見据えて
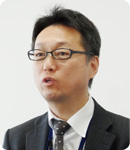
日本では2015年3月に電力の発送電分離(2020年実施予定)・都市ガスの小売り自由化(2017年実施)が閣議決定され、エネルギー供給の選択肢が広がりつつあります。国内の一部の事業所では、電力会社との契約を見直しガス会社と併用することでコスト削減につなげたケースもあります。エネルギー業界が大きく転換する中で、各事業所が立地する地域のインフラも見据え、自家発電設備も含めた多様なエネルギーによる効率的な運用を追求していきます。
生産管理部 効率化担当課長 川口 和男