Special Feature
Employing Chemical Recycling to Realize a Closed-Loop
Recycling System for Polystyrene Food Containers
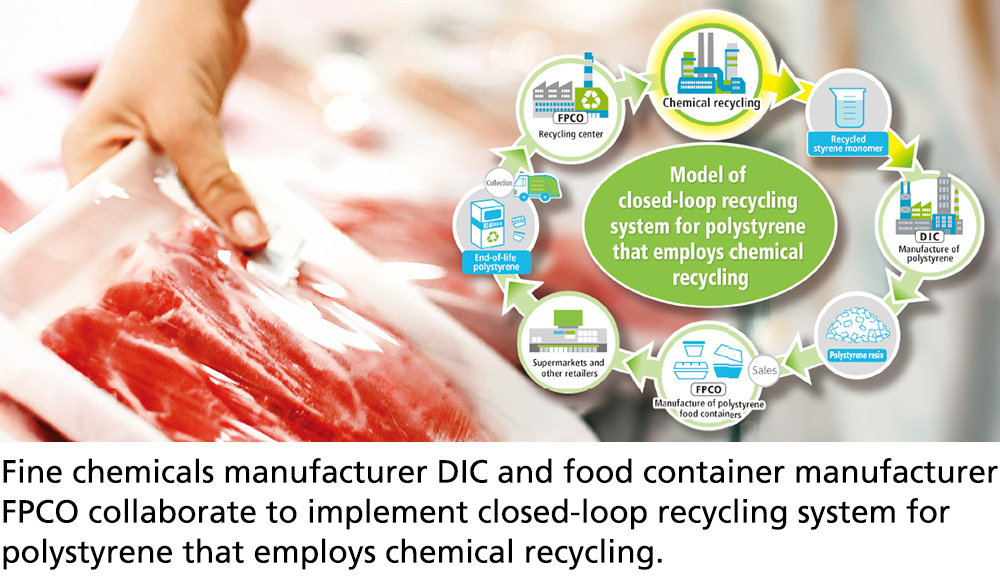
Value Creation Closed-loop recycling of polystyrene to reduce the use of resources and energy, and the discharge of waste
Given the increasingly critical nature of the issue of waste plastic, the need to reinforce recycling systems is an increasingly urgent imperative.
Polystyrene food containers are widely used because they are light and easy
to carry, easy to process and color, and protect food by preventing moisture
ingress. In Japan, municipalities separate and collect appropriately disposed-of
post-consumer polystyrene food containers, turning them over to recycling firms
to be transformed back into raw materials, but a significant amount is discarded
improperly as general waste and ends up being incinerated or sent to landfills.
Another problem is illegally dumped waste plastic, which often ends up in
rivers and the ocean, becoming a major cause of environmental pollution in
rivers and oceans, harming ecosystems, disrupting ship navigation, hindering
tourism and fishing, and damaging coastal areas. A particular cause for concern
is microplastics, fragments of plastics 5mm or less, and superfine nanoplastics,
which are ingested by marine organisms, persisting throughout the food chain
to eventually harm the health of humans.
With countries tightening restrictions on waste plastic imports, exports
are no longer a disposal route for Japan, which had previously exported a
portion of the waste plastic it generates as materials for recycling. Accordingly,
establishing an infrastructure for the recycling of waste plastic within the
country is an increasingly urgent imperative. Critical to addressing this
imperative is reducing the volume of waste plastic generated. To this end, it is
necessary to reconsider single-use plastics, promote the development of new
plastic resource recycling technologies and systems, and pare consumption of
petroleum-derived resources and energy.
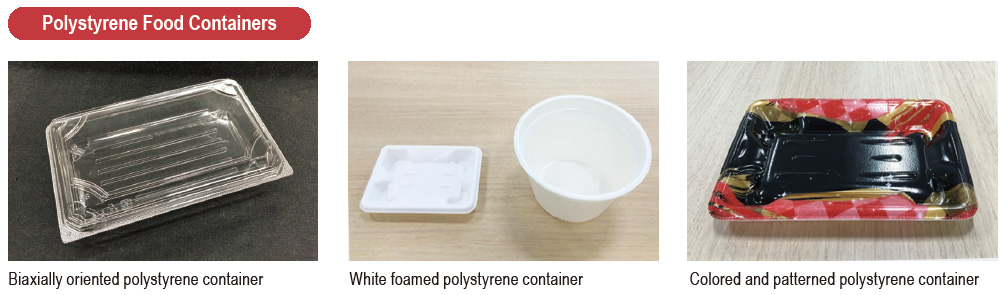
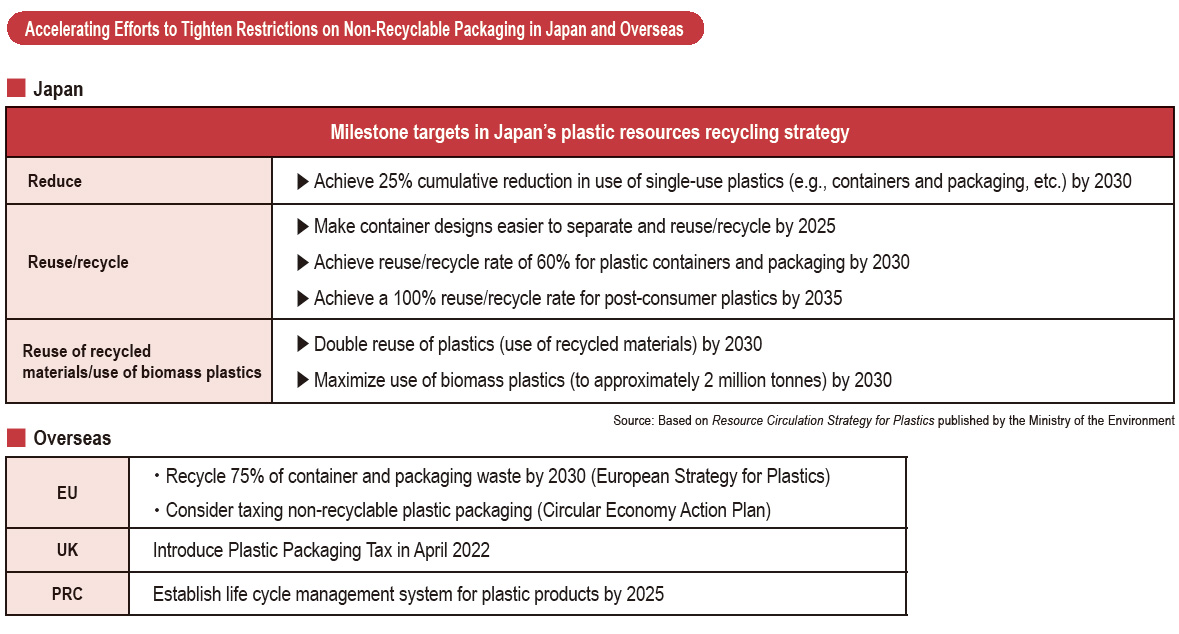
DIC and FPCO: Building a Closed-Loop Recycling System for Polystyrene
DIC was the first company to succeed in developing and mass producing
hyperbranched polystyrene, which it markets in Japan under the name
Hybranch. Approximately 80% of the polystyrene manufactured and sold by
the Company is currently used in the production of food containers. At present,
DIC is participating in a project to realize advanced plastic resource recycling
systems that involves collaboration among industry, government and academia.
The Company also conducts research regarding the infl uence of polystyrene,
films, inks, adhesives and other materials on recyclability in an effort to develop
products that exert less of an impact on the environment.
FP Corporation (FPCO), based in the city of Fukuyama, Hiroshima Prefecture,
is Japan’s largest food container manufacturer and a major destination for DIC
polystyrene. The company boasts a nationwide network of 9,600 collection
centers and three recycling plants, through which it recovers and transforms
post-consumer foamed polystyrene food containers into new food containers
using materials recycling. Currently, the company pulverizes and melts these
containers into polystyrene pellets, with those from white containers recycled
into new environment-friendly Eco Tray containers (“tray-to-tray recycling”) and
those from colored and/or patterned containers recycled into clothes hangers
and other household items.
In November 2020, DIC and FPCO announced a new model of circular
recycling system that will maximize the two companies’ technologies, and
collection and recycling configurations, with the aim of achieving the practical
implementation of advanced resource recycling. This initiative also seeks to
facilitate the use of chemical recycling to transform colored and/or patterned
polystyrene, which to date could not be recycled into food containers, facilitating
fully closed-loop recycling of all types of polystyrene products.
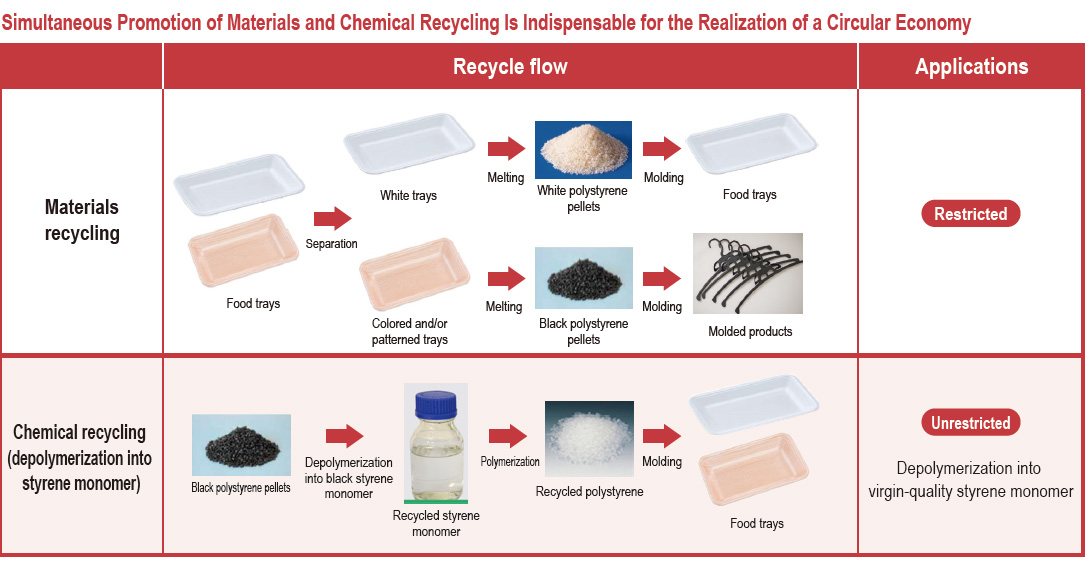
A Distinctively DIC Response Using depolymerization through chemical recycling to realize closed-loop recycling of polystyrene food containers
Introducing third-party technologies and launching a testing plant in 2022
In addition to polystyrene, colored and/or patterned food trays contain ink
and adhesives. As a result, using materials recycling, which pulverizes
and melts the entire tray, yields black pellets and causes the deterioration
of physical properties, so the commercial value thereof is significantly
reduced. Such pellets also cannot be used for food-contact surfaces. In
contrast, polystyrene is suited to chemical recycling because it can be easily
depolymerized back into its precursor—styrene monomer—with only minimal
energy using pyrolysis, also known as thermal degradation. Because
polystyrene made with chemically recycled styrene monomer delivers the
same performance and safety levels as that made with petroleum-derived
virgin raw material, there are no limits to potential applications.
DIC thus plans to introduce third-party technologies and equipment for
depolymerizing polystyrene back into styrene monomer and to build a testing
facility at its Yokkaichi Plant, in Mie Prefecture, the Company’s principal
polystyrene production facility. The testing facility is expected to begin
operations in 2022. Through this, the Company aims to establish control
technologies that increase yields by evaluating depolymerization efficiency,
energy consumption and cost, among other factors, at annual production
levels of several thousand tonnes.
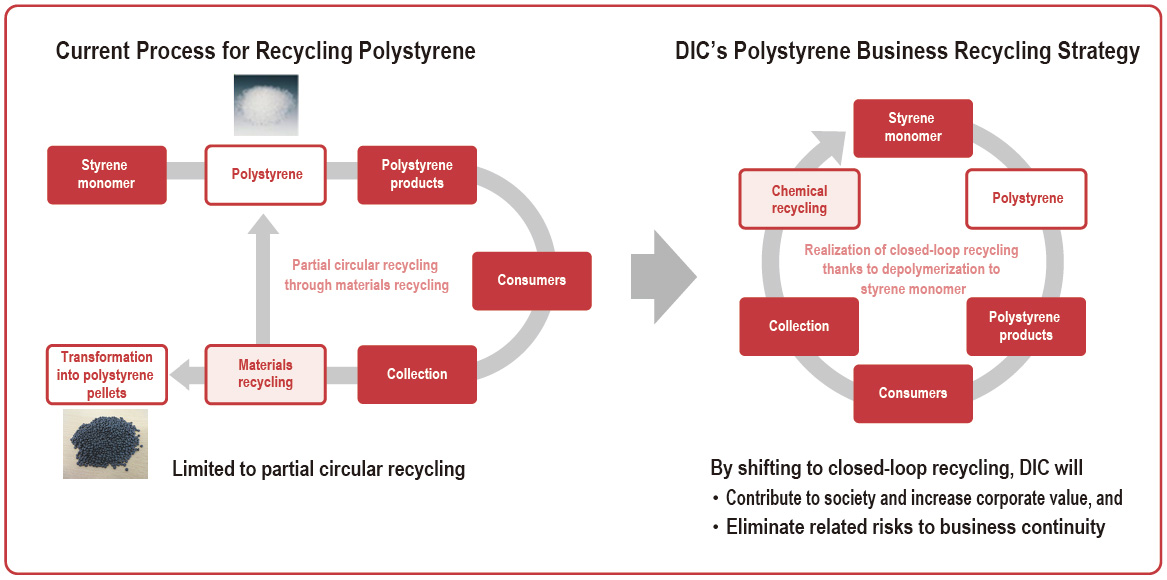
The challenge of chemical recycling: A process with outstanding potential
Materials recycling is the principal method used to recycle plastics in
Japan. The use of chemical recycling, which leverages a chemical reaction
to recycle resources, remains rare. However, given the limits of materials
recycling, the progress and expansion of chemical recycling is essential
to realizing the sort of advanced recycling-oriented society envisioned by
people around the world. The new closed-loop recycling system launched
by DIC and FPCO can be said to be a litmus test of the potential of chemical
recycling in the future. The DIC team expects the establishment of new
technologies for depolymerizing polystyrene into styrene monomer to
facilitate expansion of the initiative’s focus to include biomass inks and
adhesives and is thus committed to boldly taking the steps necessary to
ensure commercialization as quickly as possible.
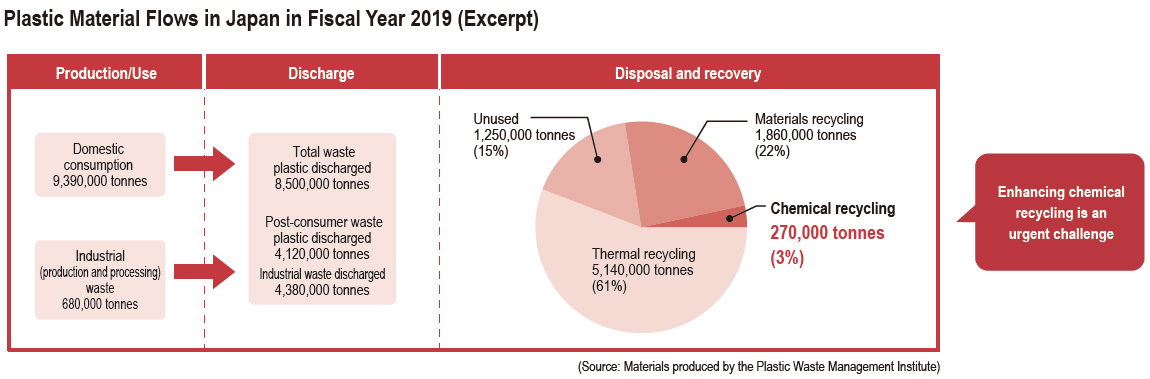
KEY PERSON from DIC
A sense of crisis shared by both DIC and FPCO led to this initiative.
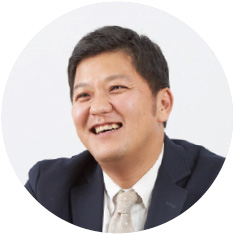
Over many years working together, DIC and FPCO have come to share an awareness of key imperatives. We launched this initiative because of a shared sense of crisis derived from the recognition that given the overall trend toward resource recycling, the survival of related businesses in the future depends on moving away from single-use food containers. Depolymerization back to styrene monomer is key to the closed-loop recycling of polystyrene. The ability to achieve closed-loop recycling will be a critical measure of fine chemical manufacturers’ corporate value. We look forward to building an optimal chemical recycling–based model system that contributes to a substantial reduction of waste and CO₂ emissions by choosing and integrating superior basic technologies.
Manager, Polystyrene Sales Group, Packaging Material Products Division, DIC Corporation Ken suke Shinya
We are working to make the best use of the existing collection and recycling infrastructure to achieve early commercialization.
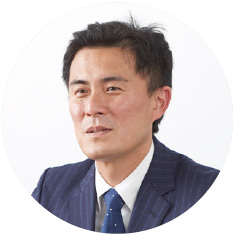
A number of chemicals manufacturers have begun to explore chemical recycling of polystyrene. The fully closed-loop model that we are working on makes the best use of the infrastructure built by FPCO in 1990 for what it calls “FPCO-method” circular recycling, which involves the collection and transformation of post-consumer containers using materials recycling. We are enhancing this already essentially complete recycling system by adding chemical recycling. Decomposing colored and/or patterned polystyrene into styrene monomer to facilitate the efficient recovery of resources is not an easy proposition, but we are committed to mobilizing DIC’s extensive know-how to facilitate the practical implementation of a system that helps resolve plastics-related environmental issues.
Manager, Polystyrene Sales Group, Packaging Material Products Division, DIC Corporation Ryou Minakuchi
Stakeholder Perspective
COMMENT
We look forward to the early establishment of chemical recycling technologies that balance greenhouse gas emissions reduction and economic efficiency.
Using “FPCO-method” circular recycling, we collect post-consumer foamed polystyrene containers and transform
them into new food containers. We also recycle colored and/or patterned foamed polystyrene into a variety of
other items. Our desire to be able to recycle these latter containers inspired efforts to begin research in the area
of chemical recycling.
The challenge with chemical recycling technologies is that they will not be sustainable unless they help reduce
greenhouse gas emissions as well as make sense economically. We are confident that DIC will be able to clear
both of these hurdles to swiftly establish the best and most appropriate technologies.
Currently, colored and/or patterned polystyrene food containers are not the only type currently in use that
cannot be recycled into food containers. With this in mind, we look forward to increasing the range of input
materials we can recycle to bolster consumer recognition of the fact that polystyrene is an easy-to-recycle,
environment-friendly plastic and in so doing to expand the market for such containers.
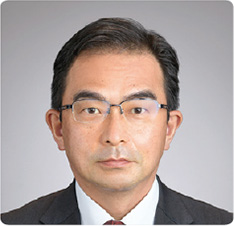
Executive Director,
Executive General Manager of
Purchasing Division, FP Corporation
Hiroshi Ogawa
Special topics 2021
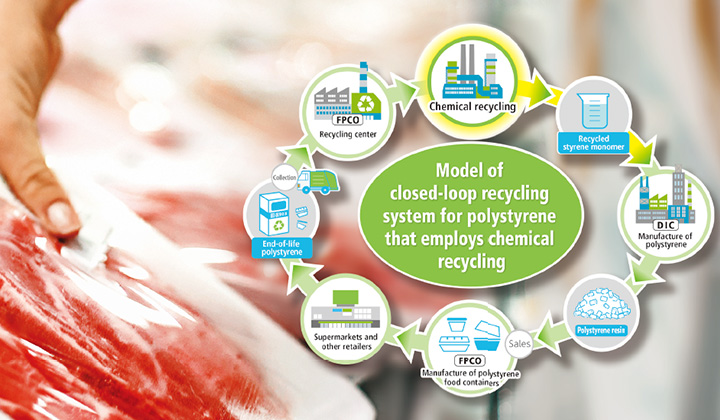
Employing Chemical Recycling to Realize a Closed-Loop Recycling System for Polystyrene Food Containers
Fine chemicals manufacturer DIC and food container manufacturer FPCO collaborate to implement closed-loop recycling system for polystyrene that employs chemical recycling.
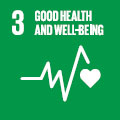
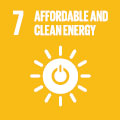
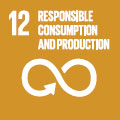
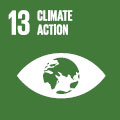
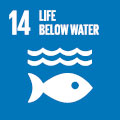
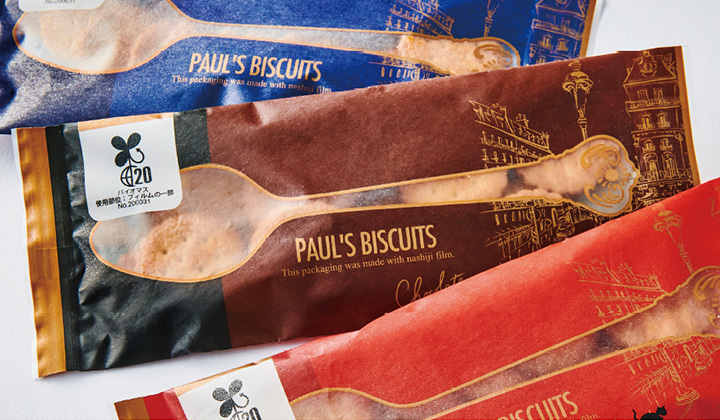
Nashiji Film Made with Biomass Plastic (DIFAREN® A7440Bio)
DIC has developed a new food packaging film that is refined and visually appealing while at the same time reduces CO₂ emissions.
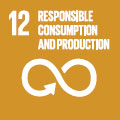
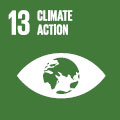
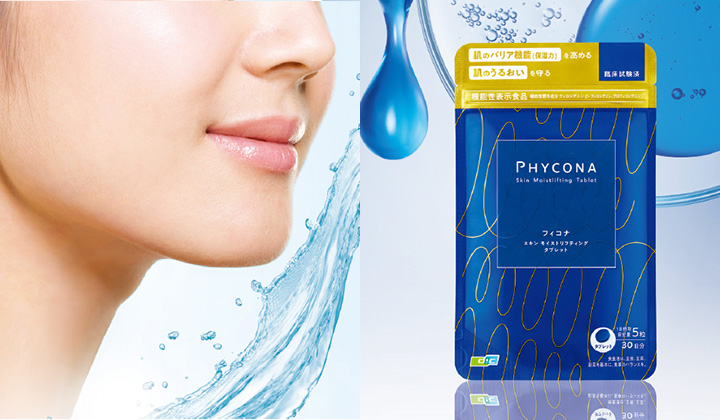
An FFC that Improves the Skin’s Barrier Function from the Inside Out (PHYCONA Skin Moistlifting Tablets)
DIC has developed a new “edible” skin-care product, made with phycocyanin extracted from Spirulina blue-green algae, that addresses various skin problems.
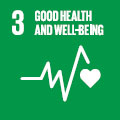
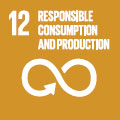