Special
Feature
Fast-Curing Solvent-Free Adhesive DUALAM™
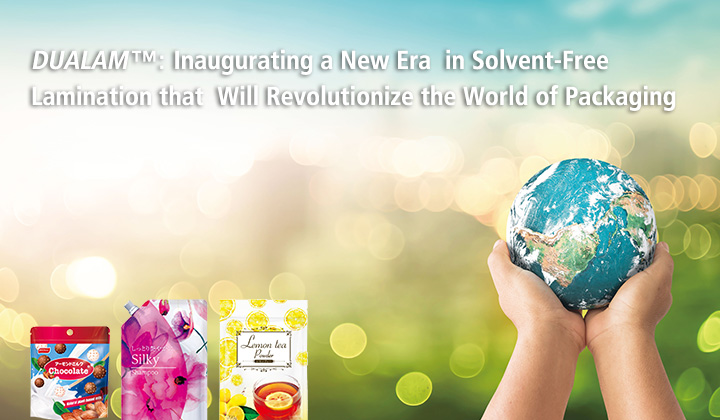
Value Creation Reduced emissions of VOCs and CO₂ attributable to lamination
Issues with conventional solvent-free adhesives, which boast a low environmental impact but have limited applications
The fabrication process for multilayer packaging films—which involves laminating two or three layers of film together, printing artwork on the reverse side of the top layer, coating to impart moisture, light, gas and other barrier properties, and sealing— has come into widespread use worldwide. The common approach to lamination is to coat the surface of one layer with an adhesive substance dissolved in solvent and then pressure bond it to another layer after thermally evaporating the adhesive’s solvent
component. Nonetheless, the use of solvent-based adhesives is not without problems, notably negative environmental impacts such as emissions of pollution-causing volatile organic compounds (VOCs) and CO₂, the latter caused by the burning of fossil fuels.
Solvent-free adhesives are also popular, but present issues such as poor designability after lamination and incompatibility with continuous lamination—key to high productivity—due to slow curing speeds, which limits possible packaging applications. DIC recognized that resolving such issues would both facilitate the expansion of applications and help reduce the environmental impact of the packaging industry.
Development of the versatile fast-curing solvent-free adhesive DUALAM™
Having created a project aimed at surmounting the issues associated with solvent-free adhesives, DIC hit on the idea of coating the main agent and curing agent on the film surface separately, rather than the conventional approach of mixing the two component agents of the adhesive together prior to laminating, and began development of a new adhesive. Through trial and error with various component combinations and coating amounts, in 2019 the project succeeded in developing DUALAM™, an innovative solvent-free adhesive boasting a curing speed several times higher than existing offerings.
Partnering with a leading laminating machine manufacturer, DIC also developed a dedicated supply unit for DUALAM™, which was launched as a lamination system that can be retrofitted onto existing laminators.
DUALAM™ enjoys a number of key performance advantages. These include facilitating the production of previously impossible two-layer laminates and the continuous processing of laminated structures with three or more layers; rapid curing, which shortens aging time; a longer adhesive pot life (the length of time an adhesive remains processable); and significantly improved designability. Lamination using DUALAM™ and existing machines retrofitted with the new lamination system also substantially reduces emissions of VOCs and CO₂ compared with lamination using solvent-based adhesives and the same equipment.
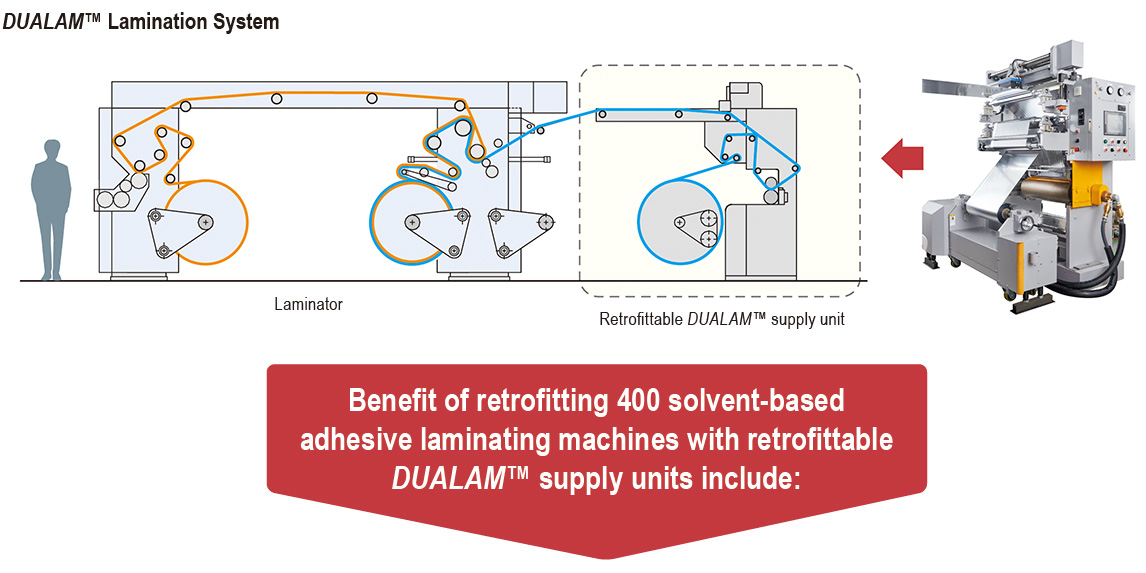
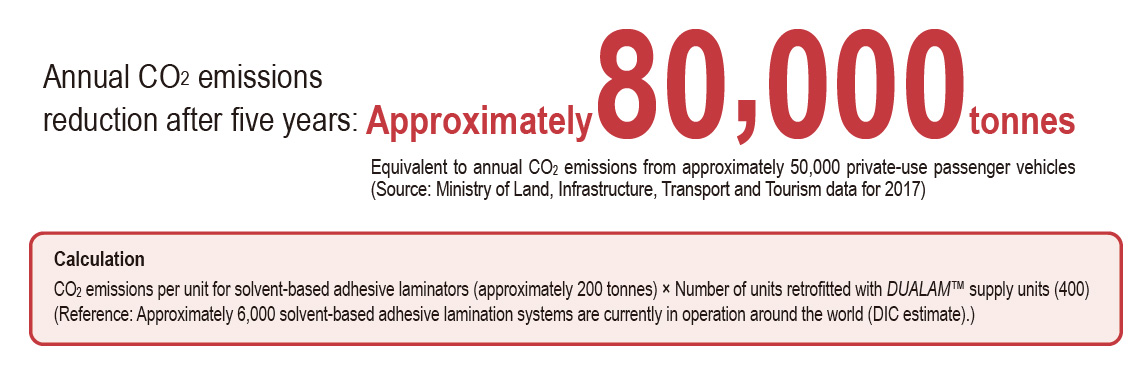
A Distinctively
DIC Response
Providing packaging solutions that contribute to sustainability for the global environment
An innovative solvent-free adhesive that contributes to reduced air pollution and improved work environments
It was a DIC adhesives marketing manager in the PRC who first noted a slowdown in sales of solvent-free adhesives for film lamination, the adoption of which had risen sharply during the second decade of the 21st century against a backdrop of tighter environmental regulations. Examining contributing factors, he determined that the principal causes were that designability after processing was inferior to film laminated with solvent-based adhesives and curing was too slow to support continuous lamination. This, together with rising pressure to reduce environmental impact, convinced him that if performance could be improved then demand for environment-friendly solvent-free adhesives would increase and so he proposed the creation of a dedicated project.
Refusing to be constrained by the conventional notion of premixing the adhesive’s components, the project’s technical team experimented with various approaches, arriving at the idea of coating the two components of the adhesive separately onto each film layer to be bonded and initiating curing only after the layers come together. However, a number of obstacles to the realization of a viable product were still ahead.
The quest to control curing speed and find the optimum combination of adhesive components
Features demanded of new adhesives include a softness that makes coating easy, curability that does not impair designability and a curing speed compatible with continuous lamination. Moreover, these features must be demonstrated in a thin film weighing only a few grams per square meter. The technical team marshaled accumulated expertise, testing a wide range of new materials in a bid to find the optimum combination of adhesive components. It proved particularly difficult to control curing speed and adjusting the delicate composition was tricky, but these efforts eventually yielded DUALAM™, a solvent-free adhesive that cures several times faster
than comparable conventional adhesives.
The challenge did not end there. Developing a supply unit that made it possible to use DUALAM™ with existing laminating machines was crucial. DIC partnered with a leading
laminating machine manufacturer to perfect a unit that thinly and evenly coats the new adhesive onto film surfaces. With this achievement, the Company was finally ready to launch DUALAM™, thereby fulfilling its pledge of providing packaging solutions that contribute to sustainability for the global environment.
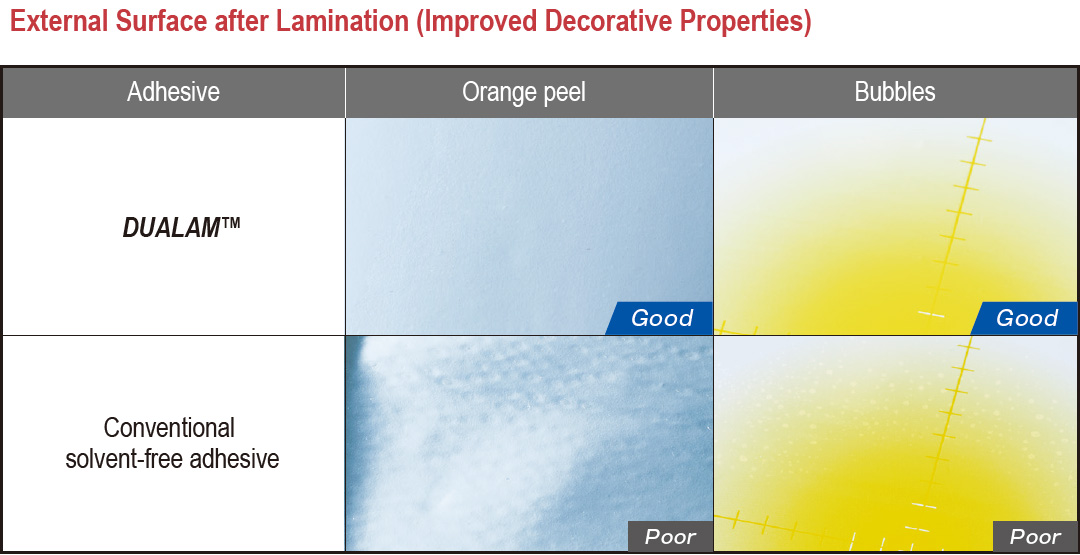
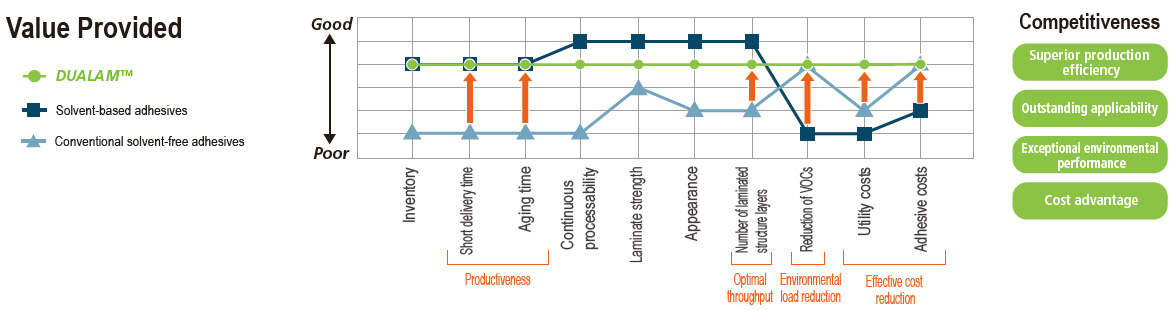
KEY PERSON from DIC
This is worthwhile for DIC precisely because it’s something no other company is doing.
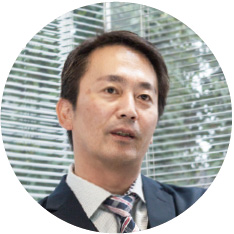
When I was working in the PRC, I recognized that there were issues with solvent-free adhesives for film lamination and proposed that we develop a new adhesive. In particular, the lamination of structures with three or more layers was extremely inefficient, but there were no companies looking to fix this problem. Precisely for this reason, I thought it was a worthwhile challenge for DIC to take on. Solvent-free adhesives are essential to reduce the environmental impact of packaging film production, so we were confident that demand would increase if applications could be expanded. Many breakthroughs were needed to realize a viable product, but thanks to the assistance of many people we succeeded in bringing DUALAM™ into being. It was definitely a proud moment!
Manager, Packaging & Graphic Business Development Group, Packaging & Graphic Business Group, DIC Corporation Chouichi Takada
We are working to provide more value to customers by developing new technologies.
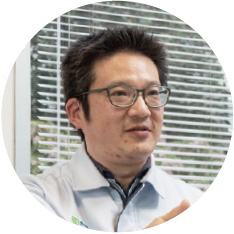
Performance features required of adhesives are diverse and include ease of application, rapid bonding and strong adhesion. The defining characteristic of DUALAM™ is that it cures rapidly, which helps increase customers’ productivity. However, if it bonds too quickly the quality of the finish will be poor and the quality will deteriorate. For this reason, we tested repeatedly to determine the optimum bonding speed, a process of trial and error through which we eventually achieved our goal. Going forward, we will continue taking bold steps to address the challenge of reducing environmental impact by developing innovative laminating adhesives like DUALAM™.
Manager, Adhesives Technical Group 1, Adhesives Technical Division, DIC Corporation Koji Akita
Since the launch of DUALAM™, many customers from Japan and overseas have come to see us.
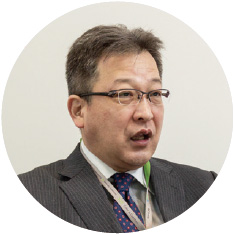
Since the launch of DUALAM™ in 2019, we have received many inquiries from customers both in Japan and overseas and a steady stream of requests to tour our facilities. Promotional efforts currently center on Japan and Asian markets, but we plan to expand our focus to include Europe early in summer 2020. By fiscal year 2025, we aim to achieve annual global sales of ¥9.0 billion. We will also work to expand the range of packaging applications for DUALAM™ and our lineup of lamination systems, with the aim of realizing innovative packaging materials that contribute to safety and peace of mind, as set forth in DIC111.
Project Manager, P-2 Project, Next-Generation Packaging Business Unit , New Business Development Headquarters, DIC Corporation Susumu Nishimura
Special Topics 2020
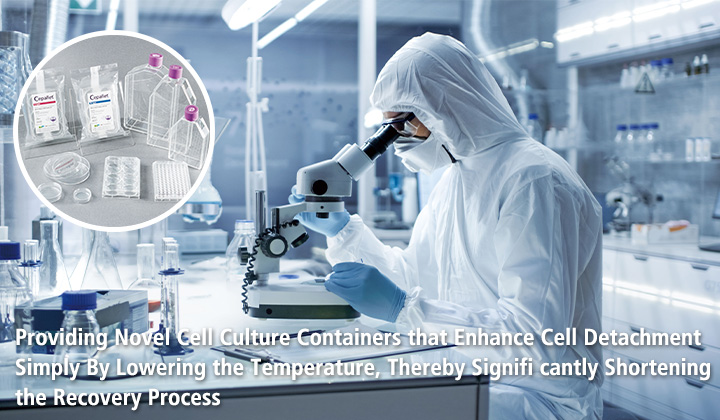
Thermoresponsive Cell Cultureware that Facilitates the Harvest of Cells Without Enzyme Treatment or Damage (Cepallet®)
Providing Novel Cell Cultureware that Enhances Cell Detachment Simply by Lowering the Temperature, Thereby Significantly Shortening the Harvest Process
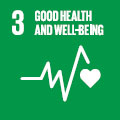
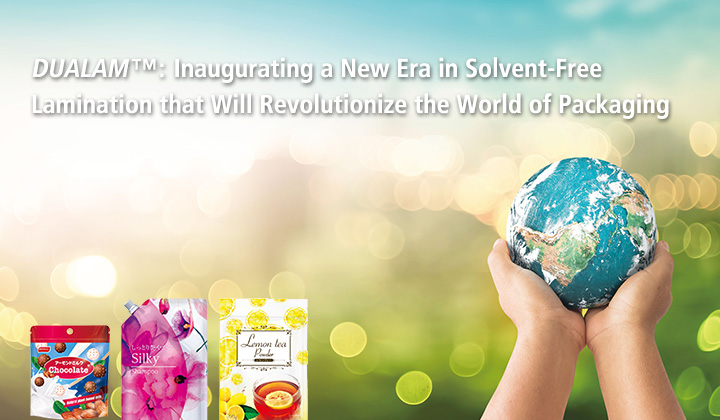
Fast-Curing Solvent-Free Adhesive DUALAM™
DUALAM™: Inaugurating a New Era in Solvent-Free Lamination that Will Revolutionize the World of Packaging
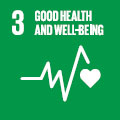
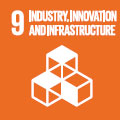
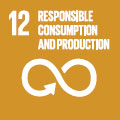
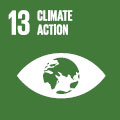