Special Feature Lithium Ion Batteries : Materials for Lithium-Ion Batteries
Contributing to the evolution of high-performance batteries is essential in a smart technology-based society
Social Imperative Increase the energy density and reliability of LiBs
Lithium-ion batteries (LiBs) are batteries that discharge and charge thanks to the movement of lithium ions between the cathode and the anode. In addition to being smaller and lighter than other secondary batteries, LiBs charge quickly. For these reasons, LiBs are expected to play an important role in the years ahead in everything from smartphones, tablet computers and PCs to emergency batteries for electric vehicles and aircraft, as well as in smart cities—which make use of decentralized energy systems and information and communications capabilities—and other energy-conscious infrastructures of the future. Challenges facing battery manufacturers include making LiBs thinner and lighter by achieving higher energy density with the aim of accommodating increasing device functionality, as well as prolonging battery lifespan, shortening charge time and increasing safety.
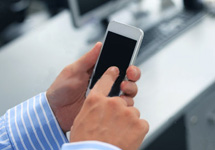
DIC’s Response(1) Develop active materials that increase lithium-ion storage capacity



One of the key concerns with smartphones and electronic vehicles is the short use time/driving range per charge. LiB charges drain quickly because of the limited ion absorption capacity of the active material (graphite) used for the anode, to which lithium ions move from the cathode during discharge. To date, this has prevented further increases in energy density.
Employing its distinctive synthesis technologies for nanolevel composites, DIC is currently developing an advanced high-capacity alternative material for anodes. This carbon-based material contains particles of silicon and tin, which alloy easily with lithium ions, in a stable dispersion. Because active materials expand and contract during the charge and discharge cycles of an LiB, increases in capacity can cause the materials to break, the resin binder used to hold the particles together to tear and the conductive path to be disrupted. DIC addressed this difficulty by dispersing particles into the carbon, thereby minimizing expansion and contraction of the active material, and by employing a binder developed in-house. If commercialized, this new active material will contribute to the realization of more compact mobile devices, as well as make it possible to use mobile devices longer and drive electric vehicles further on a single charge.
KEY PERSON of DIC
We are maximizing key DIC Group synergies to revolutionize LiB technologies.
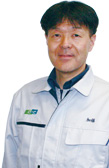
Although there is plenty of research being conducted into the use of silicon and tin as active materials to increase the capacity of LiBs, the fact is that it is difficult to control expansion and contraction. By leveraging its core technologies, DIC has succeeded in precisely controlling nanoparticle distribution, a potential solution to this issue. Going forward, we will strive to contribute to technological innovation in this area by maximizing synergies with our multiple other core technologies.
Principal Researcher, Functional Materials Group 3, Core Value Research Center, Corporate R&D Div. Shinji Kato
Bringing the “Dream, Inspire, Create” concept to life
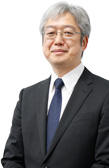
Recent years have brought astonishing progress in the area of LiBs, which is spurring innovation in a wide range of areas, from mobile devices to automobiles and stationary fuel cell power systems. By playing a key role in this field, DIC seeks to help reduce the negative environmental impact of equipment in which LiBs are used, as well as to create new value by inspiring and delighting people everywhere. I expect exciting things from DIC in the years ahead.
Manager, High-Performance Chemicals Development and Sales Dept., Advanced Polymer Sales Div. Hiroyuki Mariko
DIC’s Response(2) Develop an adhesive for LiB packs that offer outstanding electrolyte resistance




Laminated multilayer film is steadily replacing conventional metal as the preferred material for the containers used to hold LiB packs. One reason for this is the need for packs to be able to endure heavy current. Other requirements include low electrical resistance, high heat dissipation and formability, and ease of disposal.
In 2013, DIC drew on the vast pool of technologies it has accumulated in the area of food packaging to develop a new adhesive for laminated LiB packs. Adhesives used to bond multilayer films to aluminum foil substrates must remain strong, even when immersed in highly acidic electrolyte solution. DIC responded by greatly enhancing adhesiveness, thereby realizing excellent shielding properties and productivity.
KEY PERSON of DIC
Our success is due to close collaboration among expert teams both inside and outside of DIC.
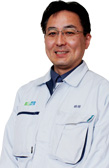
The success of this project reflected our ability to leverage our know-how in both adhesives and resins, as well as to collaborate with related materials manufacturers. Such broad-based cooperation was made easier by last year’s corporate reorganization. Looking ahead, we will continue to promote organic collaboration with expert teams in various fields with the aim of expanding into the area of materials for LiBs used in Automotive.
Group Manager, Dispersion Technical Group 2, Dispersion Technical Div.1 Masami Hozumi
DIC’s greatest strength is its sophisticated laminating technologies.
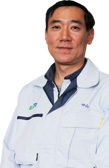
These laminated films were not created simply by bonding together aluminum foil substrates and films. We dramatically increased electrolyte resistance by interposing a newly developed adhesive between two substrates with significantly different properties. Made possible by our proprietary resin mixing technologies, this adhesive is a solution that we can offer with confidence.
Head Researcher, Dispersion Technical Group 2, Dispersion Technical Div.1 Tatsuya Koyama
Our goal is to become a valued partner in the production of LiBs in markets worldwide.
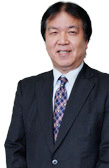
Countries around the world are working actively to cultivate national LiB industries. At the same time, plastics and aluminum manufacturers, among others, are seeking to enter the market for LiB pack materials. With the aim of being a principal supplier of such materials to LiB manufacturers, DIC is focusing efforts on the development of adhesives for laminated LiB packs and other related materials.
General Manager, High-Performance Chemicals Development Dept.,Advanced Polymer Sales Div. Masaru Imai
Special Topics 2014
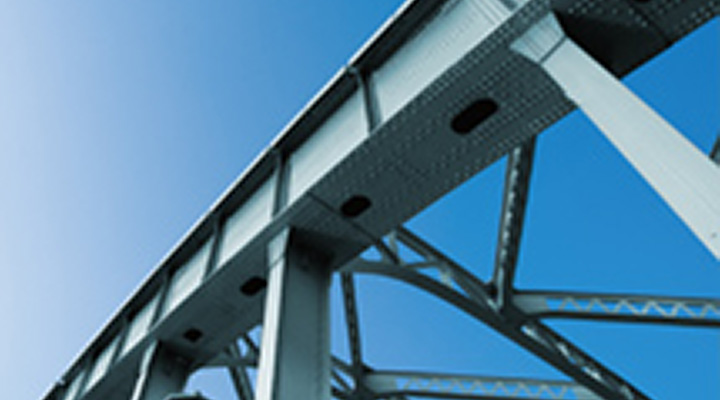
Ceranate® : Hybrid Resin for Coatings
Seeking to shield houses and other structures from UV rays and air pollution
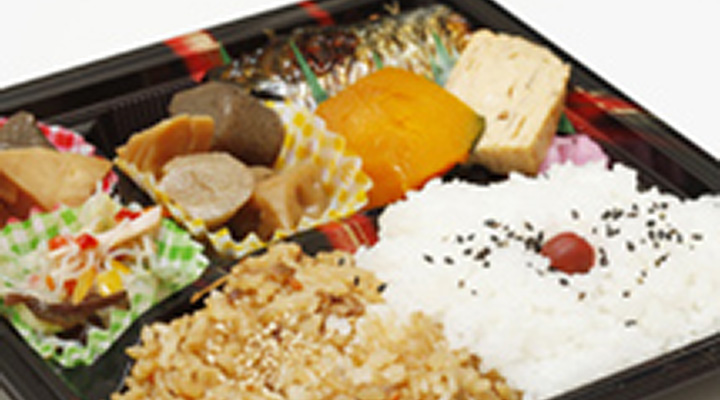
Hybranch® : Hyperbranched Polystyrene
Enhancing the environmental performance of food containers, electrical appliance components and insulating materials
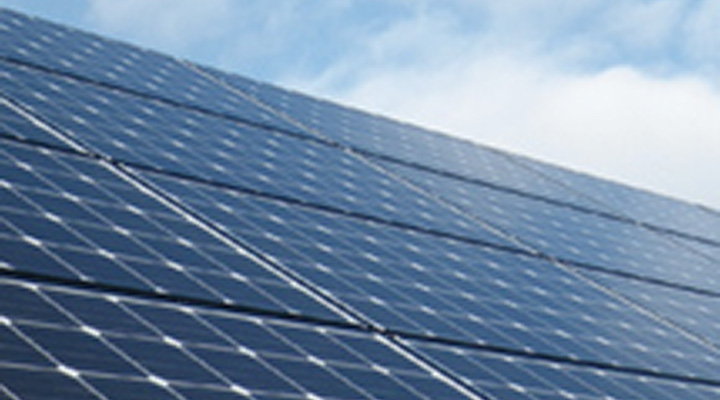
Solar Cells : Materials for Solar Cells
Seeking to extend the lives of solar cell modules
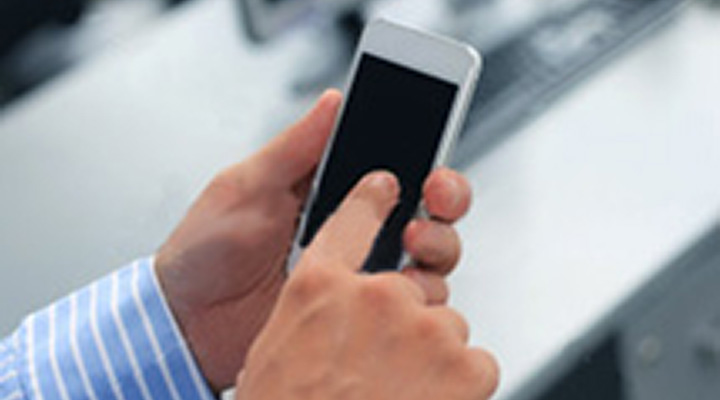
Lithium Ion Batteries : Materials for Lithium-Ion Batteries
Contributing to the evolution of high-performance batteries is essential in a smart technology-based society
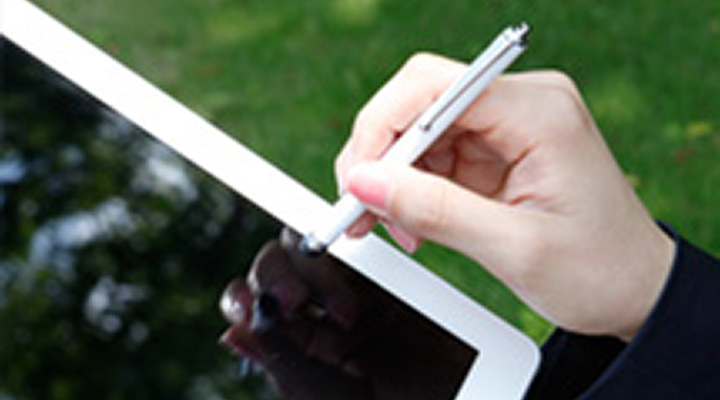
Printed Electronics : Materials for Printed Electronics
Making today’s advanced information society easier to navigate and more environment-friendly
TOPICS
Sun Chemical Revamps its Website
The Sun Chemical Group, a core member of the DIC Group with operations in North America and Europe, recently revamped its website, improving search capability and simplifying navigation.
DIC Expands Supply Capabilities for Linablue® Natural Blue Food Coloring
Rising concern for the health benefits and safety of food is accelerating a shift toward using natural, rather than synthetic, colorings in the food products industry. As the world’s largest manufacturer of one of the few natural blue colorants in existence, the DIC Group intends to bolster its supply capabilities by building a new plant in the United States.