Preventing Global Warming(2018)
Principal Initiatives in Fiscal Year 2018
01Setting a New Long-Term Target for the Reduction of CO₂ Emissions
The DIC Group has declared “decarbonization” as a key theme of its sustainability program and is working to lower emissions of CO₂ by reducing energy consumed by its businesses, as well as by advancing the use of energy from renewable sources by, among others, adopting biomass fuel, introducing solar and wind power, and purchasing low-carbon electric power. In October 2016, the Sustainability Committee set a medium-term target for reducing absolute emissions of CO₂ across global DIC Group sites by 7.0% from the fiscal year 2013 level by fiscal year 2020. To this end, the Group added promoting the use of electric power generated from renewable energy, including by biomass boilers and solar power systems, as well as by the purchase of low-carbon electric power, to core energy-saving initiatives at sites.
In line with its commitment to ESG management, in February 2019 the Group set a new long-term target its new medium-term management plan, DIC111—which will guide its efforts from fiscal year 2019 through fiscal year 2021—of a 30% reduction in CO₂ emissions from the fiscal year 2013 level by fiscal year 2030. By achieving this target, which exceeds the 26.0% reduction pledged by Japan under the Paris Agreement, DIC aims to show its strong commitment to being a socially responsible manufacturer of fine chemicals. Looking ahead, the DIC Group will work to achieve these targets by promoting a two-pronged strategy centered on promoting energy-saving initiatives at sites and actively advancing the use of renewable energy.

02Energy Consumption and CO₂ Emissions by the Global DIC Group
Although production volume by the global DIC Group was essentially level in fiscal year 2018, energy consumption was down 1.4% from fiscal year 2017 and 12.7% from the fiscal year 2013 base year. The Group’s global CO₂ emissions declined 2.6% from fiscal year 2017, or 14.5% from fiscal year 2013, while emissions per unit of production, expressed in terms of kilograms of CO₂ per metric tonne, were down 2.3%, or 11.5% from fiscal year 2013.
The DIC Group’s diverse product portfolio encompasses printing inks, polymers, pigments, LCs, engineering plastics and compounds. Recent years have seen an uptrend in the output of energy-intensive fine chemicals and a downtrend in the output of items the production of which is comparatively energy efficient. Against this backdrop, the Group’s success in achieving a reduction in the volume of CO₂ emitted worldwide that exceeded its target for the year was due in large part to the decisive implementation of energy-saving and carbon-reduction initiatives worldwide, with efforts by Group companies in Japan playing a particularly significant role. Principal factors behind these results included the start-up of a megasolar power system with a generating capacity of 1.6 MW at the Kashima Plant and a biomass boiler with an evaporation rate of 2.5 metric tonnes/hour at the Hokuriku Plant, and the purchase of lowcarbon electric power at several sites in Japan. Going forward, the DIC Group will continue to take steps to reduce energy consumption, as well as to further advance its use of renewable energy by shifting to clean fuels and solar power.
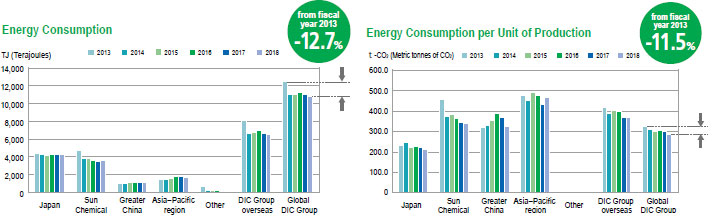
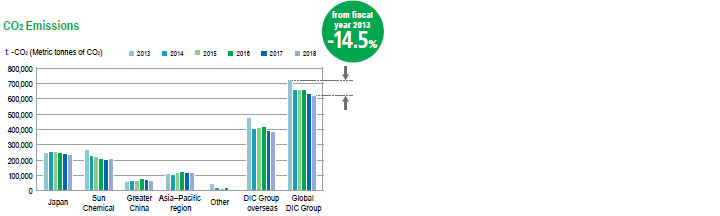
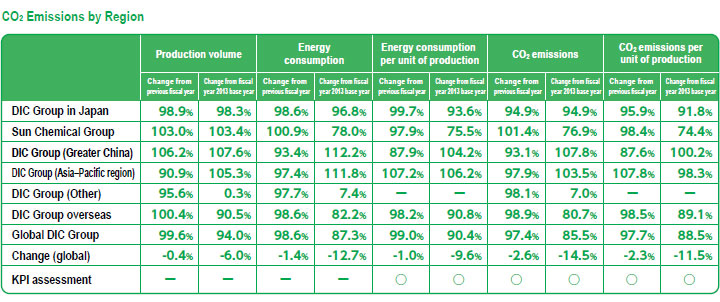
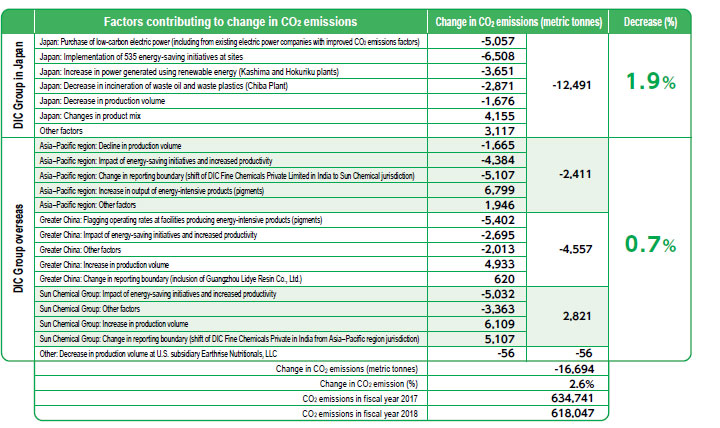
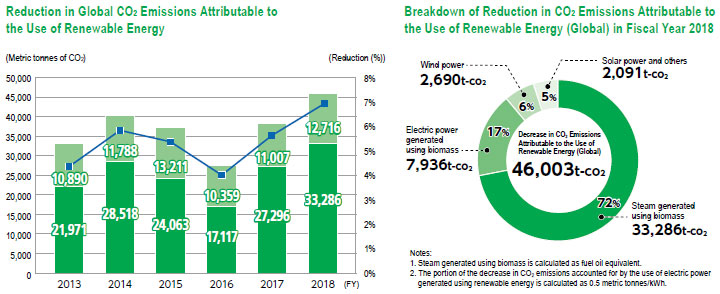
03Energy Consumption and CO₂ Emissions by the DIC Group in Japan
With production volume by the DIC Group in Japan—the 52 sites operated by DIC and domestic Group companies—down 1.1% in fiscal year 2018, energy consumption declined 1.4% and energy consumption per unit of production edged down 0.3%. CO₂ emissions fell 5.1%, to 231,820 metric tonnes, from 244,359 metric tonnes in fiscal year 2017, and CO₂ emissions per unit of production decreased 4.1%, to 212.7 kg CO₂/metric tonne, from 221.8kg CO₂/metric tonne. The sharp decline in CO₂ emissions reflected, among others, the revision of standards used to evaluate potential environmental facility investments to include factors such as balance between environmental value and depreciation, making it easier to install solar power systems, among others, and the implementation of energy-saving initiatives at individual sites.
Principal factors behind these results and the resulting reductions included the start-up of a megasolar power system, an increase in know-how regarding the operational management of wind power systems, an increase in biomass boiler operating rates attributable to a shift to independent maintenance and management, and an improvement in heating medium pump combustion efficiency at the Kashima Plant, which accounted for decreases of 900 metric tonnes, 400 metric tonnes, 800 metric tonnes and 400 metric tonnes, respectively; the full-scale start-up of a biomass boiler at the Hokuriku Plant, which supported a reduction of 1,600 metric tonnes; the implementation of 535 energy-saving initiatives at sites, which were responsible for a decline of 6,500 metric tonnes; and the purchase of low-carbon electric power with a low CO₂ emissions factor, which accounted for a decrease of 5,000 metric tonnes. These factors were sufficient to offset an increase arising from changes in product mix, yielding a net reduction in CO₂ emissions of approximately 12,500 metric tonnes, equivalent to 5.1% of total emissions by the DIC Group in Japan.
Regarding CO₂ emissions across its supply chain, in fiscal year 2017 DIC participated in a lecture on science-based targets (SBTs) organized by Japan’s Ministry of the Environment. As a result, DIC now reports data for all categories of Scope 3*. The Company obtains third-party verification for “waste generated in operations.”
- Scope 3 emissions are indirect emissions from production, transport, shipment, commuting and other activities in the supply chain.
04Energy-Saving Initiatives by the DIC Group in Japan
DIC Group sites (plants and R&D facilities) in Japan endeavor to conserve energy by promoting the following initiatives, which target the reduction of base load energy consumption, and by applying the PDCA cycle to improve the efficiency of production methods—thereby reducing energy used—and shorten process times. Since fiscal year 2017, sites also promote carbon-reduction initiatives.
- Employed highly efficient lighting and air conditioning measures to eliminate waste
- Introduced energy-saving controls on pumps and blowers
- Used more efficient compressors and implemented measures to reduce pressure losses
- Implemented measures to improve the power factors of electric equipment
- Adopted high coefficient of performance chillers and promoted measures to prevent cold and hot water supply waste
- Reduced use of boiler fuel, among others, through the recovery of waste heat
- Ensured optimal warming times and temperatures for raw materials
- Implemented 544 energy-saving initiatives at domestic production sites
- Actively promoted the use of renewable energy at suitable sites (installation of megasolar power system at the Kashima Plant and biomass boiler at the Hokuriku Plant)
- Purchased low-carbon power at suitable sites
- Increased output of electric power generated using renewable energy (biomass boiler and wind power generating facilities at the Kashima Plant)
In fiscal year 2018, these initiatives reduced energy consumption by approximately 279,000 GJ (equivalent to approximately 7,000 kl of crude oil). This corresponds to approximately 35,000 200-liter drums of crude oil, or 6.6% of the total energy consumed by the DIC Group in Japan in the period under review.
Going forward, the DIC Group will continue working to reduce its consumption of energy, as well as to identify new themes and share best practices across Group sites. In addition, the Group will reinforce operating manuals to optimize the performance of key energy-consuming equipment, including boilers, chillers and compressors, and expand the deployment of initiatives at sites both in Japan and overseas.
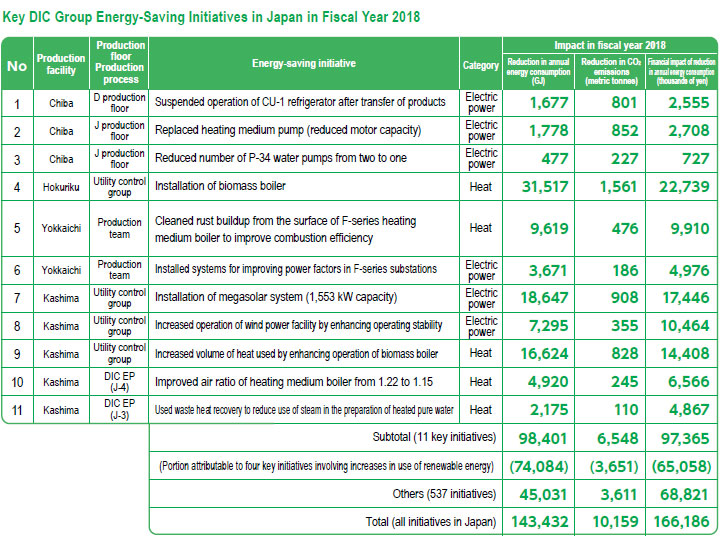
Horizontal Deployment and Further Strengthening of Energy-Saving Working Groups
In Japan, leaders of domestic site Utility Control Groups, which oversee energy and water supplies and wastewater treatment, hold quarterly Utility Control Liaison Working Group conferences. A central focus of conferences is Energy-Saving working groups. Here, Utility Control Group managers are joined by representatives of the Production Management Department, who are currently assisting with efforts to prepare a manual outlining key energy-saving measures, compile best practice case studies, discover and test new methods for reducing energy consumption, consider the use of renewable energy as a way to reduce carbon, and conduct energy-saving analyses at sites nationwide.
The Energy-Saving Promotion Manual sets forth measures for, among others, enhancing the visibility of energy consumption, the framework for promoting energy-saving initiatives, procedures for formulating energy-saving plans, creating energy management standards, approaches to benchmarks for gauging energy performance and to investments in energy-saving initiatives, and use of the PDCA cycle to measure the progress of initiatives. The manual is distributed for use across the domestic DIC Group. Energy-saving analysis begins with comparing initiatives against the manual, creating a numerical expression of findings and plotting the results on a radar chart. Subsequent steps are to formulate proposals for addressing weaknesses identified through this process, implement remedial measures and follow up on results. Efforts to formulate proposals are not limited to individuals directly responsible, but also include pertinent department and plant general managers. DIC will continue to use these energy-saving analysis activities to raise the level of efforts at sites nationwide, in addition to which it will add risk management–based BCP to the list of assessment criteria used and begin deployment at overseas Group production facilities.
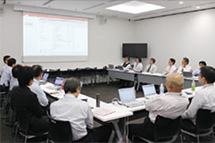
Energy-Saving Working Group meeting
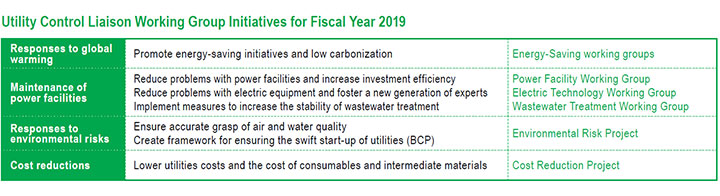
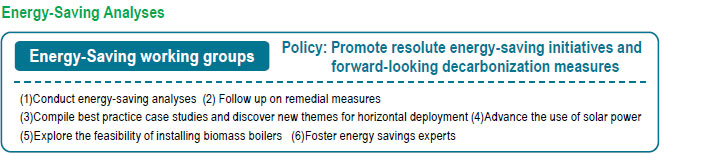
In fiscal year 2018, energy-saving analyses were conducted at four DIC Group sites in Japan (DIC EP Corp.’s Sodegaura Plant, Seiko PMC’s Harima Plant, DIC’s Chiba Plant and DIC Graphics’ Tokyo Plant). Analyses focused on improving the performance of energy conversion equipment, including compressors, chillers, boilers and substations; decreasing energy losses by energy-consuming equipment; improving energy conservation; and enhancing energy management; and deploying best practices at other sites. Analysis teams consisting of members of Energy-Saving working groups from across the country are dispatched to sites to conduct audits. This process is also used as a training opportunity for site energy managers, young mid-career individuals in charge of energy management at their respective sites. These audits comprise a key pillar of the DIC Group’s energy-saving and decarbonization framework in Japan. The Group will continue to conduct audits in fiscal year 2019 to ensure that all Group companies are on the same wavelength regarding energy-saving initiatives.
Reducing Energy Consumption and Enhancing Product Quality through Kaizen Skill Improvement Training
Having recognized that enhancing the awareness of employees in production and providing them with the tools to continuously improve their work are crucial to strengthening front-line capabilities, in 2008 DIC began offering the Kaizen Skill Improvement Training Program. This program—which is structured around four themes, namely, reducing energy consumption, increasing yields, enhancing product quality and rationalizing operations—seeks to foster professionals who can identify and resolve issues on their own initiative. Participants spend one year participating in initiatives aimed at improving quality control methods and the following year putting their findings into practice. Each December, achievements are presented at a briefing attended by pertinent plant general managers and executives.
Having recognized that enhancing the awareness of employees in production and providing them with the tools to continuously improve their work are crucial to strengthening front-line capabilities, in 2008 DIC began offering the Kaizen Skill Improvement Training Program. This program—which is structured around four themes, namely, reducing energy consumption, increasing yields, enhancing product quality and rationalizing operations—seeks to foster professionals who can identify and resolve issues on their own initiative. Participants spend one year participating in initiatives aimed at improving quality control methods and the following year putting their findings into practice. Each December, achievements are presented at a briefing attended by pertinent plant general managers and executives.
Improving Yields by Expanding Use of a System to Enhance the Visibility of Energy Consumption
With the aim of optimizing energy use on a facility-by-facility basis, DIC developed a system that measures, monitors and verifies waste and irregularities in use in real time, thereby enhancing the visibility of energy consumption. The system is also useful for verifying the benefits of energy-saving initiatives implemented, underscoring its role as an essential tool for promoting the reduction of energy consumption. At present, DIC is gradually introducing a visibility-enhancing system that also analyzes process-specific energy consumption for individual products and lots. The Company has installed the system on the V production floor of the Chiba Plant, the C production floor of the Kashima Plant and the B production floor of the Sakai Plant and is using it to promote the reproduction optimum yields for materials inputs. In fiscal year 2016, a more advanced version of the system was installed at the Yokkaichi Plant. Looking ahead, the Company will continue to promote adoption at other sites.
05Reducing Fossil Fuel Use by Promoting the Use of Renewable Energy
Renewable Energy as a Percentage of Total Energy Used by the DIC Group in Japan: 12.1%
The bulk of renewable energy used by DIC Group companies in Japan is natural energy generated by a biomass boiler and wind and solar power facilities at the Kashima Plant. In fiscal year 2018, DIC Group companies in Japan used 586,000 GJ of renewable energy (equivalent to 15,123 kl of crude oil), up 18.0% from fiscal year 2017 and representing 12.1% of total energy (steam and electric power) consumption by these companies. This increase was attributable to the stable operation of an existing biomass boiler, efforts to achieve an optimal mix of power sources (biomass boiler, wind power, solar power, a cogeneration system and purchased electric power) and the start-up of a megasolar power system (comprising 5,588 278-watt panels with a total surface area of 13,772 m2) with a generating capacity of 1.6 MW (January 2018) at the Kashima Plant (January 2018), and the full-scale start-up of a biomass boiler with an evaporation rate of 2.5 metric tonnes/hour at the Hokuriku Plant (January 2018). The use of renewable energy accounted for a 36,530-metric tonne reduction of CO₂ emissions in Japan from the fiscal year 2017 level, accounting for 13.6% of the total reduction achieved by the Group in the period.
Early in fiscal year 2019, DIC completed the installation of solar power systems at five sites. These facilities, which will produce a combined total of 1.5 MW of electric power annually, began operating in January 2019. Particularly notable is the system established at the Tatebayashi Plant, which boasts an annual generating capacity of 1.3 MW—second only to the Kashima Plant’s megasolar power system—and accounts for approximately 20% of the electric power used annually by the plant. Going forward, DIC will continue to take decisive steps to advance its use of renewable energy with the aim of achieving its long-term target for reducing emissions of CO₂ emissions across global DIC Group sites by 30% from the fiscal year 2013 level by fiscal year 2030.
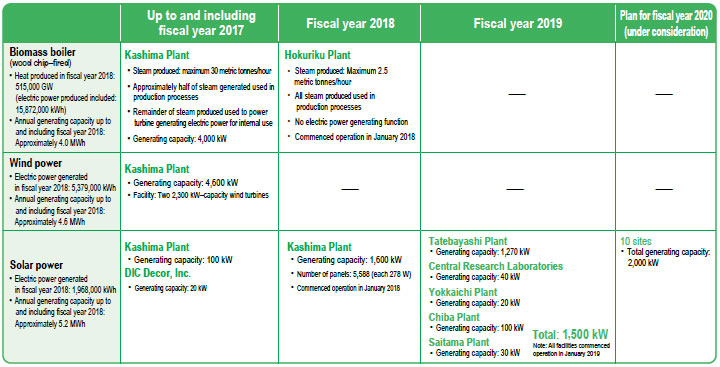
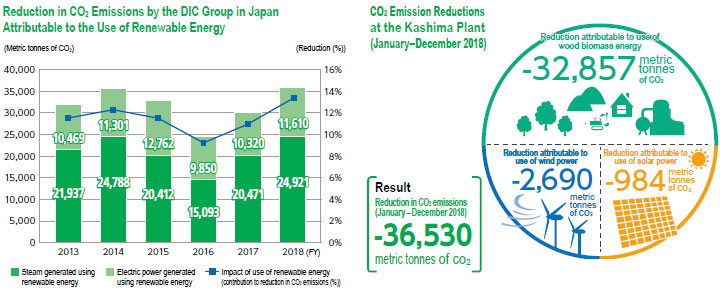
Independent Electric Power Generation: 24.0% of Total Consumption in Japan
Electric power consumption by the DIC Group in Japan in fiscal year 2018 rose 1.7% from the previous fiscal year, to 287,870,000kWh, approximately 24.0% of which was generated independently, with electric power generated using renewable energy accounting for 8.0% and electric power generated using cogeneration systems representing 16.0%. Independently generated electric power was up 5.0% from the previous fiscal year, owing to an increase in solar power.
Portion of Purchased Electric Power Replaced with Low-Carbon Alternative
Owing to an increase in consumption, electric power purchased by DIC Group companies in Japan rose approximately 1.0% in fiscal year 2018. Because purchased electric power accounts for around 76% of the electric power it uses, the Company sought to reduce the CO₂ footprint of its purchased electric power by replacing a portion thereof with a low-carbon alternative. This accounted for a reduction in CO₂ emissions of 6,508 metric tonnes, or 2.7%, from fiscal year 2017. DIC will continue to promote the procurement of green electric power by reviewing the companies from which it purchases electric power and prioritizing those with a low CO₂ emissions factor.
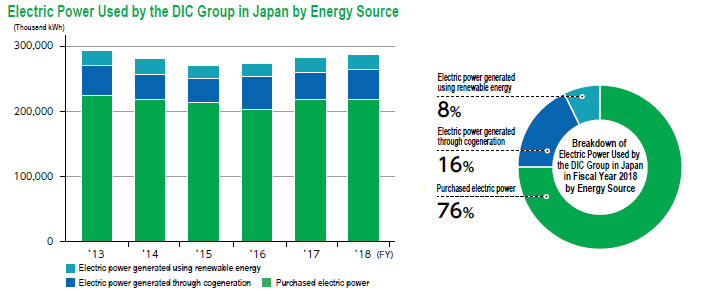
06Development of a Weather Forecast Data–Based Renewable Energy Solution
Renewable energy sources are highly dependent on the weather. For this reason, maximizing use and at the same time ensuring a balance with purchased electric power and electric power generated using cogeneration is a major challenge. At the Kashima Plant, such adjustments were previously made by a small team of operators. In fiscal year 2018, the facility began developing a system that uses weather forecast data to automatically adjust supplies in accordance with weather conditions. In collaboration with the Corporate Engineering Department’s Process Automation Engineering Group, the plant also developed a proprietary software program. The new system sends key forecast data, including sunlight, temperature and wind speed, from the Japan Weather Association up to three days in advance, to a computer that is linked to renewable energy generation facilities (including solar and mind power facilities and biomass and methanegas boilers), cogeneration systems and purchased electric power facilities, facilitating automatic adjustment to optimize energy use. The system was introduced on a trial basis later in the year and benefits are currently being verified. DIC also hopes to see the system used as a case study of a striking improvement in operating efficiency achieved using information and communications technologies (ICT).
VOICE
DIC has switched from manual to automatic control for adjusting supplies of electric power.
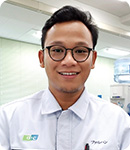
DIC had never before used a system that adjusts electric power supplies based on weather forecast data and there was very little in the way of helpful information, so the whole development process—from selecting a company to provide weather-related information to developing a proprietary program—was pretty fraught.
I built the program’s monitoring and management functions primarily using Microsoft Excel Visual Basic for Applications (VBA) macros. I had to teach myself how to program using VBA, which was entirely new to me. I also did not know enough about the equipment on the Kashima Plant’s utility floor, so unfamiliar technical terms made communicating in Japanese with colleagues on the front lines more difficult. Nonetheless, I pushed ahead with the goal of helping create a highly reliable program for the Kashima Plant that meets its needs, suits its equipment and can be easily modified at any time.
Working at DIC has given me the opportunity to become familiar with a wide range of advanced technologies and gain broad experience. I look forward to using my position as an engineer with global credentials to act as bridge between my home country of Malaysia and Japan, as well as to contributing to both countries and the world at large.
Process Automation Engineering Group, Corporate Engineering Department, Chiba Plant Mohammad Farhan Bin Mohd Fauzi
We were tasked with developing a weather forecast data-based system for using renewable energy.
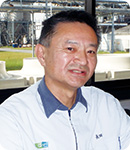
This project was quite challenging for someone who had joined DIC only two years earlier, but Mr. Farhan’s energetic nature and communications skills served him well. The system he has built for us will both reduce CO₂ emissions and increase our operating efficiency. While there were many hurdles, particularly in selecting a company to provide weather-related information that satisfied our requirements, developing logic and creating a method for importing website weather data, I was impressed by his ability to resolve any issues that cropped up, seeking the assistance of the Utility Control Group and his more experienced colleagues when necessary, and press on with the task at hand.
I look forward to seeing Mr. Faran take on new challenges and achieve outstanding results, and am confident t hat his t alent for creative execution will ensure he grows and thrive in the years ahead.
General Manager, Process Automation Engineering Group, Corporate Engineering Department, Chiba Plant Kazuyuki Nagata
TOPICS
DIC Wins New Energy Foundation Chairman’s Award in the Adoption and Application Category of the 2018 New Energy Awards
In December 2018, DIC won a New Energy Foundation Chairman’s Award in the Adoption and Application Category of the 2018 New Energy Awards in recognition of the expanded use of renewable energy at the Kashima Plant. The awards program, which was presented by the New Energy Foundation, was established with the aim of encouraging the introduction of new energy and promoting awareness by commending particularly excellent initiatives.
The Kashima Plant has installed multiple renewable energy–powered generating facilities, including biomass and methane gas boilers, as well as wind power and solar power systems. As a consequence, 50% of electric power and 80% of heat consumed annually by the site is generated by using renewable energy. These facilities also contributed to a reduction in annual CO₂ emissions in fiscal year 2018 of 35,000 metric tonnes. Looking ahead, the department responsible for the plant’s energy supply will continue working to enhance the combustion efficiency of generating facilities, including biomass and methane gas boilers, by upgrading maintenance and management technologies and accumulating know-how.
The Chairman’s Award recognizes the positive results of these steadfast efforts. DIC will deploy know-how accumulated by the Kashima Plant at sites both in Japan and overseas with the aim of increasing its use of renewable energy and reducing its emissions of greenhouse gases around the world.
Reductions in Annual CO₂ Emissions Attributable to the Use of Renewable Energy at the Kashima Plant
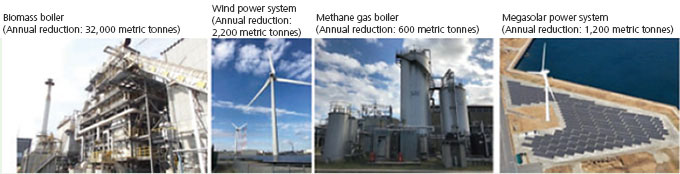
VOICE
Our goal was to optimize the Kashima Plant’s energy supplies.
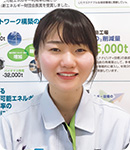
My duties include managing data related to the various types of energy used by the Kashima Plant, promoting energy-saving measures and assisting with the management of utility floor equipment operations. The Kashima Plant is a unique facility in that it consumes more energy than any other DIC Group site in Japan and has wide range of electric power generating facilities and boilers. It is necessary for us to select the best mix of energy for the operating status of production floors. Operational management at the Kashima Plant is not something you can experience at any other site. In addition, because energy consumption and energy usage vary from one production floor to another, we must promote rationalization in a manner that takes into account the equipment and operating methods employed on each floor. My job is challenging, but many aspects of it are rewarding. Looking ahead, we aim to leverage IoT and AI technologies, as well as to flatten out energy demand, with the aim of building a more robust energy network.
Utility Control Group, Kashima Plant Rina Kawano
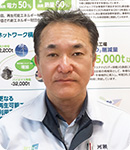
Ms. Kawano is the Kashima Plant Utility Control Group’s first female employee and recently celebrated here second year here. Her principal responsibility is data management for the group. The Kashima Plant was one of the earliest DIC sites in Japan to address the challenge of optimizing its energy mix. Unless you understand the status of other sites, it is difficult to understand the Kashima Plant’s unique nature. I look forward to seeing her grow as one of DIC’s first female energy managers by capitalizing on her optimistic personality and gaining a wide range of experience.
General Manager, Utility Control Group, Kashima Plant Ichirou Kawase
07Protecting the Ozone Layer
Hydrofluorocarbons (HFCs) are used widely as refrigerants in equipment and facilities. While not an ozone depleting substance, HFCs have a global warming potential 100–10,000 times that of CO₂ and their use is expected to account for a 0.5° C increase in the global average temperature by the end of the 21st century. At the 28th Meeting of the Parties in Kigali, Rwanda, held in October 2016, the Parties to the Montreal Protocol on Substances that Deplete the Ozone Layer reached an agreement to phase down production and use of HFCs (the Kigali Amendment). Japan subsequently amended its Act on the Protection of the Ozone Layer Through the Control of Specified Substances and Other Measures in line with the amendment, which as of January 10, 2019, had been ratified by 65 Parties. Having surpassed the condition of ratification by at least 20 Parties, the Kigali Amendment entered into force on January 1, 2019.
In April 2015, Japan revised the Fluorocarbons Recovery and Destruction Law. The same month, the Act on Rational Use and Proper Management of Fluorocarbons entered into force, compelling stakeholders to ascertain and report leaks of fluorocarbons from commercial equipment and facilities.
In fiscal year 2008, DIC reported leaks of fluorocarbons equivalent to 356 metric tonnes of CO₂. (Companies are obliged to report leaks in excess of 1,000 metric tonnes to the Japanese authorities.) This represents a 37.0% decline from 566 metric tonnes in fiscal year 2015, the year the Act on Rational Use and Proper Management of Fluorocarbons entered into force. The DIC Group will continue to select air conditioning and other equipment using nonfluorocarbons and other refrigerants that do not negatively impact the environment with the aim of reducing the volume of fluorocarbon leakage for which it is responsible.
08Energy Consumption and CO₂ Emissions by the DIC Group Overseas
While production volume by the DIC Group overseas in fiscal year 2018 edged up 0.4% from fiscal year 2017, energy consumption slipped 1.4%—a 17.8% decline from the fiscal year 2013 base year—and energy consumption per unit of production declined 1.8%, or 9.2% from fiscal year 2013. CO₂ emissions by overseas Group companies in fiscal year 2018 decreased 1.1%, or 19.3% from the base year, and CO₂ emissions per unit of production were down 1.5%, or 10.9% from fiscal .2013.
Factors contributing to the decline in CO₂ emissions included efforts by individual companies to break down the Group’s emissions reduction targets and promote decarbonization initiatives; the start-up of a biomass boiler at Hainan DIC Microalgae Co., Ltd., and a solar power system at Qingdao DIC Finechemicals Co., Ltd. in the PRC; the start-up of a solar power system at Siam Chemical Industry Co., Ltd. (Thailand) and the replacement of a portion of the coal used to fire boilers with palm kernel shells (PKS) at PT. DIC Graphics’ Karawang Plant (Indonesia) in the Asia–Pacific region; and the installation of additional solar power systems and initiatives aimed at improving production efficiency in the Americas and Europe.
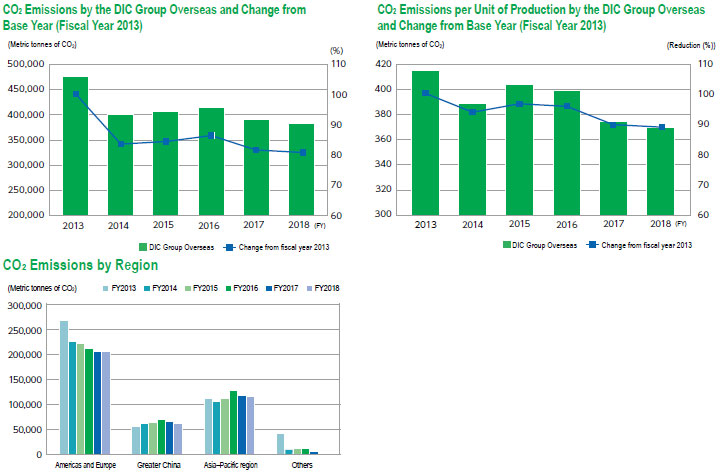
Promoting Energy Savings Overseas
Laws and regulations, as well as infrastructure, differ between countries and regions. The DIC Group strives to promote energy savings and efficient operations wherever it is active and in so doing sets precedents for the global chemicals industry.
DIC Group companies overseas continue to implement a broad range of energy-saving initiatives, including improving production efficiency, reducing base load energy consumption, choosing high-efficiency models when replacing equipment and switching to LED lighting. The Group is also promoting the use of renewable energy and has several new projects currently under consideration for implementation in fiscal year 2019 and beyond. Corporate headquarters is stepping up collaboration with overseas Group companies through energy-saving analyses and support for individual projects. In fiscal year 2018, energy-saving analyses were conducted at five sites in the Asia–Pacific region and Greater China (PT. DIC Graphics’ Karawang Plant in Indonesia, Siam Chemical Industry, DIC Colorants Taiwan Co., Ltd.; and Nantong DIC Color and Changzhou Huari New Material in the PRC. At the same time, a project was also launched whereby effective initiatives proposed by overseas sites are given “Good Job” accreditation and deployed horizontally at Group companies in Japan. This initiative also includes using the process of introducing best practices at production facilities as an opportunity to foster young human resources.
Asia–Pacific Region
The DIC Group has 22 sites in the Asia–Pacific region, which account for around 19.0% of the Group’s total global CO₂ emissions. Regional production volume in fiscal year 2018 was down 9.1% from fiscal year 2017, although it was up 5.3% from the fiscal year 2013 base year. Principal factors behind this result were a change in the reporting boundary from the shift of one site to another reporting jurisdiction. Energy consumption by Group companies across the region decreased 2.6% from the previous fiscal year, but was 11.8% higher than in the base year, while CO₂ emissions declined 2.1% from fiscal year 2017, but were up 3.5% from fiscal year 2013. Indonesia is home to the Group’s mother plant for pigments, production of which is comparatively energy-intensive and continues to rise. This pigments business accounts for more than 50% of energy consumption and CO₂ emissions in the Asia–Pacific region, underscoring its influence on results for the region as a whole. Accordingly, the Group promoted a variety of energy-saving and carbon-reducing initiatives, including replacing a portion of the fossil fuel (coal) used to fire boilers with palm kernel shells (PKS), a biomass fuel. In addition, the region is undergoing Energy-Saving Working Group energy-saving analyses by promoting use of external consultants such as the TEPCO Group. Successful energy-saving initiatives in India (at four sites belonging to DIC India Ltd.) also contributed significantly to the reduction in energy consumption.
A regional ESH country head meeting is held annually at the office of DIC Asia Pacific in Singapore, with participants including country heads, the executive in charge of regional operations and pertinent individuals from the Responsible Care Department and the Production Management Department. The principal purposes of the meeting are to explain safety and environmental policies and discuss concrete action plans for the region in the subsequent fiscal year. This includes providing an explanation of the Group’s policies for combating global warming, including its targets for the reduction of energy consumption and decarbonization, and determining related action plans. As part of its effort to ensure achievement of the CO₂ emissions target set for the global DIC Group, corporate headquarters assists local Group companies by formulating and implementing energy-saving plans; promoting ongoing energy-saving analyses to support the identification of energy-saving themes and the implementation of remedial measures; deploying a practical energy management manual and best practice case study materials to establish management practices and promote horizontal deployment; and launching and providing support for energy-saving and carbon-reduction projects at suitable sites.
Greater China
The DIC Group’s 18 sites in Greater China, which include R&D facilities, account for approximately 10% of the Group’s total CO₂ emissions. While production volume in fiscal year 2018 was up 6.2% from the previous fiscal year and 7.6% from the fiscal year 2013 base year, CO₂ emissions across the region were down 6.9% from fiscal year 2017, but up 7.8% from the base year. Among factors contributing to the decline in CO₂ emissions were lower operating rates at plants responsible for energy-intensive products, including pigments; a change in the reporting boundary resulting from the inclusion of Guangzou Lidye Resin and steadfast energy-saving initiatives and increased productivity at production facilities. Regional CO₂ emissions were negatively impacted by higher production volume; increased output of energy-intensive products such as pigments and LC materials; and factors not related to production, including an increase in base load energy consumption attributable to the expansion of floor space at research facilities and higher operating rates for clean rooms.
Once annually, regional energy officers and ESH officers hold a joint ESH conference that is also attended by the executive in charge of regional operations and pertinent individuals from the Responsible Care Department and the Production Management Department. The conference includes providing an explanation of the Group’s policies for combating global warming, including its targets for the reduction of energy consumption and decarbonization, setting a target for regional CO₂ emissions reductions and determining action plans. The conference also includes presentations introducing case studies and plans for future initiatives. The objective of the conference is to provide information on the status of regional energy management and energy-saving initiatives to help individual companies to enhance their performance
Other efforts include promoting energy-saving analyses to gauge the status of energy management and the performance of energy -related equipment. This includes having local employees designated “energy masters” assess energy-saving promotion frameworks, actual energy consumption, the formulation of policies and management of targets, and the performance of key equipment. Findings are plotted on a radar chart to identify strengths and weaknesses and encourage remedial measures.
Adoption of Renewable Energy by DIC Group Companies Overseas
Against a global trend toward decarbonization, including by popularizing the use of renewable energy, DIC Group companies in the Asia– Pacific region, Greater China and the Americas and Europe are making use of government subsidies and support to, for example, install biomass boilers and solar power systems. In fiscal year 2018, renewable energy used by DIC Group companies overseas amounted to 728,183 GJ, up 19.7% from 608,502 GJ in the previous fiscal year.
PT. DIC Graphics (Karawang Plant) (Indonesia)
Project Launched to Reduce CO₂ Emissions by Switching from Coal to PKS
PT. DIC Graphics’ Karawang Plant is a crucial facility for the production of pigments for inks and coatings for packaging, plastics and other applications, the production of which uses a significant amount of energy for boilers and water for washing. To date, the facility has primarily used coal, the combustion of which is extremely economical (approximately 1/5 the cost of heavy oil and 1/3 the cost of natural gas) and easy to obtain in Indonesia. Because the Karawang Plant accounts for a tenth of the DIC Group’s global CO₂ emissions, and because its production volume continues to expand, reducing the facility’s energy consumption and finding low-carbon energy sources is a critical challenge. To this end, the plant kicked off a CO₂ emissions reduction project focused on exploring low-carbon alternatives to coal that identified PKS.
Because Indonesia is the world’s second-largest producer of palm oil, PKS, a palm oil mill residue, are easy to secure in large quantities. Japan imports PKS for use as fuel for coal-fired electric power production facilities and biomass boilers. The project team determined that the calorific value of PKS, at approximately 4,000 kCal/kg, is comparable to that of coal used at the Karawang Plant.
In fiscal year 2017, the Karawang Plant earned certification under ISO 50001, the global standard for energy management systems. At the same time, the plant began replacing approximately 12% of the coal it used with PKS, realizing a reduction in annual CO₂ emissions of approximately 5,000 metric tonnes. In fiscal year 2018, the plant increased the percentage of PKS in its fuel mix to 25%, as a result of which annual CO₂ emissions declined by 10,000 metric tonnes, 15.0% lower than in fiscal year 2016, contributing to a decrease in global DIC group CO₂ emissions of approximately 2.0%.
Coal and PKS are difficult to combine because they combust at different speeds. In addition, considerable effort is required to remove the clinker (waste) after combustion. Corporate headquarters plans to verify the effectiveness of a chemical that can be used to easily remove clinker at production facilities in Japan, after which it will deploy the chemical at the Karawang Plant. A consulting firm affiliated with a major Japanese electric power company has also been dispatched to the plant to conduct a multifaceted analysis including the energy situation and fuel costs in Indonesia and propose a long-term plan for reducing CO₂ emissions from independent electric power generation.
Siam Chemical Industry (Thailand)
Installation of Solar Panels Reduces CO₂ Emissions
Siam Chemical Industry, which manufactures a broad range of polymer products, including synthetic resins, continues to see rising demand for acrylic coating resins, underpinned by increases in automobile production. Thailand is seeking to diversify energy sources to reduce the country’s dependence on natural gas to generate electric power. Energy from renewable sources is attracting considerable attention thanks to tax breaks offered by the Thai government. Against this backdrop, Siam Chemical Industry installed solar panels with a total generating capacity of 704 kW (annual output: 1,049 MWh) on the roofs of production buildings and warehouses at its plant in Samut Prakan Province. The solar panels commenced operation in July 2017. Electric power generated using these facilities is used on production lines and in offices.
VOICE
We continue to actively promote the use of renewable energy.
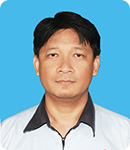
I have been part of Siam Chemical Industry’s maintenance team at for approximately 13 years. In fiscal year 2017, I supervised our solar panel installation project. Examples of production facilities in Thailand adopting solar power are few, so determining how and where panels should be installed was challenging, but thanks to the help of many people we succeeded in completing the project. In fiscal year 2018, solar power accounted for 14% of the electric power we used, while our CO₂ emissions were down 500 metric tonnes from the fiscal year 2017 level.
Thanks to abundant sunshine, Thailand is highly suited to solar power. Under Thailand’s current Power Development Plan, the company plans to boost its annual capacity for generating electric power generated using renewable energy to 18,176 MW by 2037. While solar power was initially to account for 10,000 MW, its weighting is increasing. Siam Chemical Industry will continue to monitor this trend, as well as explore further initiatives to expand our use of renewable energy.
Solar Cell Project Engineer and Maintenance Chief, Siam Chemical Industry Co., Ltd. Kiatisak Malasita
Hainan DIC Microalgae (PRC)
Biomass Boiler Replaces Diesel-Fired Unit
Hainan DIC Microalgae, DIC Lifetec Co., Ltd.’s production base in the PRC, cultivates Spirulina, an edible blue–green algae that is attracting attention as a superfood, which it processes into nutritional supplements and natural food colorings. Until recently, the facility used a dieselfired boiler to produce the steam necessary for its production processes, but in October 2016 it switched to a biomass boiler that uses waste rubber tree wood from the thinning of rubber forests as fuel. The new boiler was in operation for the duration of fiscal year 2018, resulting in a reduction of 680 metric tonnes in the facility’s CO₂ emissions for the year, equivalent to 30.0% of its emissions in the previous year. This also accounted for 1.1% of the overall decrease in CO₂ emissions achieved by the DIC Group in Greater China in fiscal year 2018.
Qingdao DIC Finechemicals (PRC)
Solar Power System Installation Helps Reduce Energy Consumption and CO₂ Emissions
Subsidiary Qingdao DIC Finechemicals, a manufacturer of base materials for TFT LCs, which it supplies to local customers, installed a solar power system that features panels on the roof of the company’s plant building. The new system, which has a generating capacity of 440 kW, began operating in September 2017. Thanks to this installation, in fiscal year 2018 Qingdao DIC Finechemicals’ output of solar power reached 490 MWh, largely in line with expectations, which was equivalent to approximately 15% of its energy consumption, and its annual CO₂ emissions declined by around 5.5%.
VOICE
We take a bottom-up approach to fostering the next generation of energy managers.
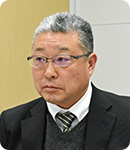
The success of energy-saving initiatives demands a true understanding of production floors and a willingness to implement remedial measures together with colleagues on the front lines. Our belief in the importance of a bottom-up approach is reflected not only in the activities of the Production Management Department but also in how we foster the next generation of energy managers, who will be responsible for energy-saving initiatives in the future. When conducting energy-saving analyses at a site in the Asia–Pacific region, we always involve young members of the site’s working group. We also consciously seek to involve members of the project overseeing the horizontal deployment of the Good Job accreditation system. Because production processes at sites vary widely depending on the business, the horizontal deployment of initiatives is not always easy. This is especially true for overseas sites because the energy situation is different in every country and territory. However, the satisfaction of achieving a goal in collaboration with site staff is immense. Being a part of successful initiatives can completely change one’s outlook.
Energy Manager, Production Management Department Satoshi Abe
Europe and the Americas
The DIC Group has 113 sites in Europe and the Americas (this category also includes sites in Africa), which account for around 33% of the Group’s total CO₂ emissions. Despite an increase in production volume of 3.0% from the previous fiscal year and 3.4% from the fiscal year 2013 base year, the Group’s CO₂ emissions in Europe and the Americas in fiscal year 2018 were held to a 1.4% increase from fiscal year 2017 and were down 23.1% from the base year. Factors behind this result included the further integration of production facilities and execution of measures to raise production efficiency, the installation of additional solar power facilities and the implementation of energy-saving initiatives and measures to improve productivity.
With the aim of lowering regional CO₂ emissions, the DIC Group not only implements key measures such as making use of biomass energy (landfill biogas), solar and small hydroelectric power, and employing outsourcing, including contracting energy-efficiency consultants to advance the reduction of energy consumption, but also continues to promote the integration of its production facilities worldwide. In fiscal year 2018, regional CO₂ emissions were down 23.1% from the fiscal year 2013 base year, contributing significantly to the reduction of the Group’s global emissions. Going forward, the Group will continue to implement ambitious energy-saving and decarbonization initiatives across Europe and the Americas.
Initiatives in Areas Other than Production
In fiscal year 2017, DIC once again promoted efforts in Japan in line with the country’s Cool Biz and Warm Biz campaigns, official efforts to reduce electric power consumption by limiting the use of air conditioning in summer and winter through measures such as the introduction of more relaxed office dress codes. The Company also continued to promote initiatives aimed at reinforcing employees’ awareness of the importance of lowering energy consumption, including replacing aging light fixtures and air conditioning equipment with newer, high-efficiency models that satisfy standards set by the ECCJ for its Top Runner program, turning off lights when not needed and implementing mandatory 22º C and 28º C summer air conditioning settings.
Support for the TCFD
The DIC Group is highly conscious of the international community’s accelerated efforts to promote decarbonization since the adoption of the Paris Agreement. As a manufacturer of fine chemicals, the Group works to help curb CO₂ emissions through its manufacturing activities and at the same time to effectively assess risks and opportunities associated with climate change while promoting Groupwide efforts to address related challenges, including through the development of products that contribute to decarbonization. In May 2019, DIC declared its support for the Task Force on Climate-related Disclosures (TCFD)*, pledging to disclose climate-related information in line with TCFD recommendations going forward.
- The TCFD was established under the auspices of the Financial Stability Board (FSB) and announced in July 2017.
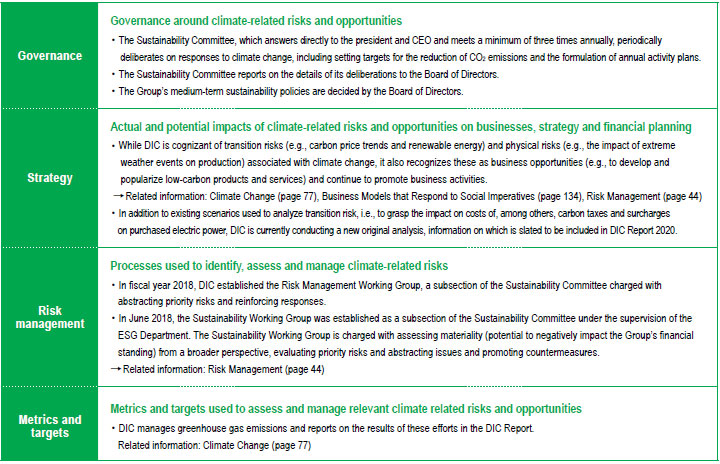
VOICE
We are promoting efforts to reduce greenhouse gas emissions based on our vision of the future role of energy in society.
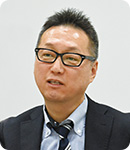
The energy situation facing companies today is changing at a dizzying pace. Further complicating matters, approaches to decarbonization vary considerably. While the obvious solution to the need to reduce greenhouse gas emissions is to move away from fossil fuels and toward electrification, CO₂ emissions factors differ depending on the energy source, i.e., whether the electric power is generated using natural gas or renewable energy. For this reason, ensuring an optimal fuel mix is not an easy task. Moreover, strategies for introducing renewable energy will change as technologies related to hydrogen energy advance. DIC has set a target for reducing CO₂ emissions across the global DIC Group of 30% from the fiscal year 2013 level by fiscal year 2030. Our mission over the next decade is to determine the most rational and efficient approach to achieving this target. To this end, we have taken a long-term, objective perspective on the future role of energy in society. We will incorporate this perspective into our strategies, while at the same time keeping a close eye on technological progress and national energy policies.
Efficiency Manager, Production Management Department (Energy Management Planning and Promotion Officer) Kazuo Kawaguchi
Back number
- Principal Initiatives in Fiscal Year 2022
- Principal Initiatives in Fiscal Year 2021
- Principal Initiatives in Fiscal Year 2020
- Principal Initiatives in Fiscal Year 2019
- Principal Initiatives in Fiscal Year 2018
- Principal Initiatives in Fiscal Year 2017
- Principal Initiatives in Fiscal Year 2016
- Principal Initiatives in Fiscal Year 2015
- Principal Initiatives in Fiscal Year 2014
- Principal Initiatives in Fiscal Year 2013