Seiko PMC Develops STARCEL CNFs and Explores the Future through Eco-Friendly Technology
- Sustainability
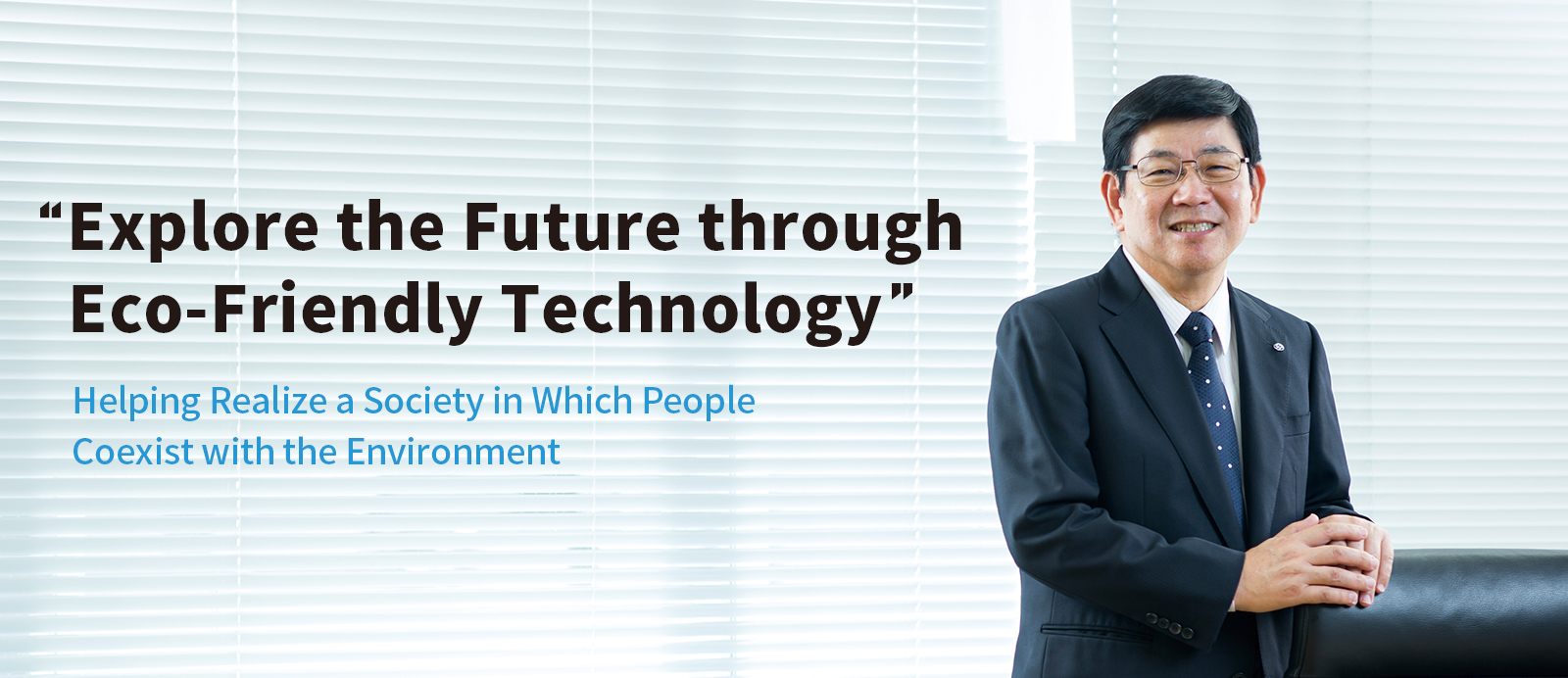
In recent years, companies’ efforts to contribute to the creation of a sustainable society have taken on increasing importance. The DIC Group is working to confront key social imperatives head on while at the same time positioning itself on a new growth trajectory. Group company Seiko PMC Corporation, a leader in the field of chemicals for paper production, has achieved considerable success in the development of innovative, environment-friendly products.
Q : Can you tell us about Seiko PMC’s businesses and your views on contributing to the environment?
Seiko PMC has four core businesses: Papermaking chemicals, resins for printing inks and toners, adhesives and fine chemicals. As far as helping to address environmental issues is concerned, as a company involved in the papermaking industry, which has had to deal with environ-mental issues, reducing the environmental footprint of printing has been a key part of how we do business since our establishment in 1968. In papermaking chemicals, our original business, we primarily manufacture and sell chemicals that add strength and water resistance to paper. Our dry strength agents make it possible to manufacture robust cardboard from paper that has been recycled multiple times. In the area of resins for printing inks, we offer products that realize both beautiful print quality and a lower environmental impact thanks to reduced solvent content, a shift to water-based products and the use of biomass.
When I was in high school, there was a sentence in a magazine I happened to be thumbing through that has stayed with me ever since: “Chemistry is a cause of pollution, but it can also be a solution.” Those words influenced my belief that it is natural to incorporate consideration for the environment. We are working with our own employees and with our colleagues across the DIC Group to promote business-es and conduct R&D with the goal of leveraging the power of chemistry to reduce the environmental impact of our products. This is an ongoing challenge, of course. I am constantly reminded of the power of chemistry and feel a tremendous sense of pride that so many of my colleagues share the same ideals.
Q : Can you tell us what prompted you to revamp your corporate mission last year?
In 2018, we marked our 50th anniversary. We took the opportunity provided by this milestone to reconsider our corporate mission. The decision to do so was prompted by a desire to clarify our direction as a company that leverages technology to contribute to the global environment. With the aim of putting this mission into practice, we solicited opinions and ideas from employees and created a new corporate vision, “Explore the future through eco-friendly technology.” By “eco-friendly technology,” we mean technology that helps protect the environ-ment and contributes to the realization of a sustainable society.
Q : What initiatives are you emphasizing as you strive to achieve the targets of your New Stage 2021 medium-term management plan?
The basic policy of our New Stage 2021 medium-term management plan is to transform Seiko PMC into a global company that contributes to the realization of a sustainable society by reinforcing our domes-tic business base, maintaining a focus on environmental technologies, and promoting the expansion of our overseas operations and the development of new businesses.
Regarding efforts to reinforce our domestic business foundation, we are working to fortify and improve our sales and product develop-ment configurations so that we are better able to meet customer needs. Efforts to promote the expansion of our overseas operations include boosting sales of adhesives sourced from Total Acrylic Polymer Industry Corporation, our base in Taiwan, and expanding our papermaking chemicals business with a focus on the promising markets of Southeast Asia. To build new businesses, we are promoting more active collaboration with customers and working to strengthen systems and create mechanisms to increase our competitiveness.
The key to the success of these efforts is our people. How well do we grasp customer needs and underlying backgrounds and social currents? Are we able to develop, sell and manufacture in markets overseas with different languages and cultures? Can we understand and respond flexibly to custom-ers vis-à-vis new applications and new fields in which we have no experience? The answer to all of these questions boils down to our employees. Accordingly, we plan to take increasingly assertive steps to secure and foster human resources under our New Stage 2021 plan. Another important factor is eco-friendly technology. We have established the Green Index, a proprietary index for sales of products that contribute to the environment (“environmentally strategic products”) and aim to increase sales of such products by more than 26% from the fiscal year 2018 level by fiscal year 2021, the final year of the plan.
Q : Can you tell us about the current status of efforts to develop new products and foster new businesses?
We originally focused on papermaking chemicals and resins for printing inks, but around 2005 we recognized the need to build a new pillar of our operations with a view to the future. Even before I was named president, we invested approximately 7% of our net sales in R&D, but as a mid-tier chemicals company with limited resources it was critical for us to narrow our focus.
At present, we are advancing the develop-ment of next-generation materials such as cellulose nanofiber (CNF), which is attracting attention as a sustainable plant-derived resource, and silver nanowire, which is expected to find application in electrodes for smartphones and solar cells. CNF is expected to be used in automotive components, resin components, housing materials and housings for small household-use electric applianc-es. In 2018, our STARCEL CNF composite materials were chosen by leading Japanese sports shoe manufacturer Asics Corporation for use in new-model running shoes. The high marks given these and other products based on eco-friendly technology reinforced employees’ commit-ment to our new corporate vision and to our corporate culture, which emphasizes taking on challenges. This is a source of tremendous pride for me.
Used in the displays for smartphones and other electronic devices, silver nanowire delivers greater responsiveness than conventional materials. Silver nanowire can also be used in flexible displays and wearable devices. The fact that silver nanowire delivers greater stability than conventional materials containing rare metals is another factor attracting attention from users. We are currently just one step away from commercializing silver nanowire. Conduct ongoing research of high value is important, but unless you succeed in bringing products to market that value will never be communicated to the world. Looking forward, we will plot our next move in the area of CNF and will aim to achieve commercialization of our silver nanowire as swiftly as possible.
Q : What can you tell us about collabo-ration between Seiko PMC and DIC?
We are currently working with DIC on a variety of fronts. For example, we sell DIC resins and purchase raw materials from them. We are also building cooperative relationships with other DIC Group companies including DIC Kitanihon Polymer Co., Ltd., in the area of production consignment. Joint procurement of raw materials and close relations with all parts of the Group, from management units to the labor union, helps compensate for a lack of expertise in certain areas.
From the early stages of research for STARCEL CNF composite materials, Seiko PMC and DIC participated in a related project coordinated by the New Energy and Industrial Technology Development Organi-zation (NEDO). This is one reason for our success in achieving the swift commercial-ization of STARCEL.
DIC and Seiko PMC share a common goal of nurturing new businesses and contribut-ing to sustainability. We look forward to reinforcing collaboration in the years ahead to bring together the technologies of our two companies to realize new businesses that contribute to the environment.
Seiko PMC Corporation Website
The creation of innovative businesses is opening new doors to the future for the DIC Group. Seiko PMC’s groundbreaking STARCEL CNF com-posite materials have been adopted by Asics for use in a new model of running shoes, attracting considerable attention. The development of these unique materials was marked by a number of interesting episodes.
What are CNFs?
CNFs consist of nanosized fibrils of cellulose, the primary component of plant cell walls. CNFs are only 1/5 the weight of steel, despite being five times stronger. They also boast a low environmental impact and are easy to recycle. While CNFs are used currently in ink for ballpoint pens and deodorizing agents for disposable diapers, to date applications have been limited. Looking ahead, further research is expected to yield applications in areas such as building materials and transportation equipment, including automobiles, and the market is expected to expand worldwide. Japan’s Ministry of Economy, Trade and Industry (METI) estimates that the annual global market for CNFs will reach ¥1 trillion in 2030.
Seiko PMC’s STARCEL CNFs
STARCEL is manufactured using the “Kyoto Process,” a proprietary production process developed as a result of research conducted as part of a NEDO project involving academic and industrial concerns and further modified by Seiko PMC. At present, applications for
STARCEL exceed those for the gel-form CNFs that have been commercialized to date and range from electronic devices to automotive components. The name STARCEL derives from the first character of “Seiko,” which is the character for “star,” and the first three letters of “cellulose.”
Note: STARCEL is a registered trademark of Seiko PMC. The ® designation is abbreviated herein.
1. The Kyoto Process: An efficient manufacturing process
The high costs of production is one reason next-generation materials often fail to gain wide popularity. In addition to not requiring the dispersion of CNFs, the Kyoto Process, used in the manufacture of STARCEL, does not use water, thereby eliminating the need for dehydration. This significantly reduces manufacturing time and cost.
2. Applications are broad and include automobiles, home electronics and building materials
Many CNF products put into practical use to date are highly hydrophilic. Accordingly, their use in hard materials and disentangle-ment to facilitate uniform dispersion in resin is difficult. STARCEL is hydrophobic and thus does not mix easily with water, facilitating uniform dispersion in resin and ensuring high strength and durability and suitability for applications such as automobiles, home electronics and building materials.
3. Use plant-based raw materials, so that impact on the environment is minimal
Because CNFs are made with cellulose derived made from woods, sustainable use and management of forests eliminate concerns regarding resource depletion. The procurement of raw materials is particularly easy in Japan, where trees are abundant. At present, glass fibers are used widely in automobiles and home electronics, but because glass fibers cannot be recycled there is a movement to restrict their use in European countries and elsewhere where environmental awareness is high. CNFs, in contrast, can be incinerated and are easy to recycle.
4. A highly promising “post–carbon fiber” material
CNFs are light and durable and can be mixed with resin for use in components for automobiles and home electronics, among others. Carbon fibers are currently the favored material in such areas, but the performance and low environmental impact of CNFs has led to them being dubbed a “post–carbon fiber” material. Used in automo-biles and aircraft, CNFs will contribute to the reduction of body weight,thereby helping improve fuel efficiency and reduce emissions of carbon dioxide (CO2).
Exhibition at the Tokyo Motor Show
At the 2019 Tokyo Motor Show, Toyota Motor Corporation displayed a concept car, brought about as part of the Nano Cellulose Vehicle (NCV) Project, manufactured using STARCEL.
STARCEL has attracted considerable attention since its adoption for use in Asics sports shoes. Director Satoru Iwata, general manager of the Technology Division, shares some episodes from the development of this groundbreaking new product.
In 2006, an article appeared in the Nikkei Shimbun, Japan’s leading business daily, about the development of CNF by Professor Hiroyuki Yano of Kyoto Univer-sity. Seiko PMC’s president Satoshi Takizawa was inspired, believing that this was something to which the company could contribute.
President Takizawa had conducted research in the area of cellulose since his university days. He immediately contact-ed Professor Yano. This led to Seiko PMC and DIC becoming involved in a NEDO project led by Professor Yano and the start of a drive toward commercialization.
Research continued for six years after Seiko PMC joined the NEDO project in 2007. In 2013, the project was selected under a METI project that seeks to foster centers of innovation, as a result of which we were able to install a CNF production plant. Since our technology is unique, there is nothing in the world to serve as a model for such a plant. The work of determining specifications from nothing was truly a joy for us as people involved in development, but at the same time the pressure was that much higher because we were using tax-funded subsidies.
In 2014, we received an inquiry from Asics, who was wondering if CNFs could be used in sports shoes. This came as a complete surprise to the development team, which was supposedly focusing exclusively on automotive applications. We delivered samples, but the reaction was not positive, so we made gradual modifications to better meet Asics’ specific needs. Two years later, STARCEL was adopted by Asics for use for the midsole of its new running shoes, which became the world’s first running shoes made with CNFs.
Unfortunately, foreign matter was found in finished products after we shifted produc-tion from small-scale lab equipment to large-scale plant equipment, a move made to facilitate mass production for Asics. An analysis of the situation revealed a mass of fibers that had not been disentangled. With the deadline for delivery almost upon us, we were forced to take development of an easily disentan-gled modified cellulose pulp back to the drawing board. It was pretty rough going, but researcher Shuhei Yamada, who had joined the team part-way through the project, stepped in and solved the problem just like that. In recognition of this achievement, the new pulp was dubbed Yamada Pulp.
Asics running shoes made with STARCEL are not only light but also boast excellent durability with soles that do not wear down even with long-term wear. The company has already sold 50 million pairs worldwide. Leveraging our track record with Asics, we are working to achieve our next target, which is to earn adoption for use as an automotive structural material, a significantly larger market. Expanding use of environment-friendly STARCEL in vehicles will help reduce their environmen-tal impact. We look forward to the day when vehicles made with STARCEL are on roads around the world and will continue to promote ambitious development efforts.
Seiko PMC is expanding its global operations, particularly in promising Asian markets through KJ Chemicals Corporation, which boasts extensive sales channels in overseas markets, and Total Acrylic Polymer Industry Corporation in Taiwan, both recent additions to the Seiko PMC Group.
KJ Chemicals Corporation
KJ Chemicals began as the chemicals division of KOHJIN Co., Ltd. Since commencing operations in the 1970s, the company has engaged in the manufacture and sale of functional monomers, centering on nucleic acid monomer and acrylamide monomer derivatives. In April 2014, the company embarked on a new chapter in its evolution as KJ Chemicals, a member of the Seiko PMC Group. Our products are used as raw materials for water-soluble polymers for use in papermaking, oil drilling and household detergents, as well as for water-based coatings and ultravio-let (UV)-curable inks and coating resins. Going forward, we will work to further refine our production technologies and propose acrylic monomers and peripheral products that are safe and offer ever-more attractive performance features.
Total Acrylic Polymer Industry Corporation
Total Acrylic Polymer Industry was established in 1998 in Taiwan and is engaged in the development, manufacture and sale of a broad range of acrylic adhesives, including double-coated industrial adhesive tapes, protective tapes, medical tapes and optical tapes. The company has built a strong business foundation by supplying customers—principally companies in the PRC and Taiwan—with distinctive adhesives that match their specific needs. Total Acrylic Polymer Industry became a member of the Seiko PMC Group in January 2019 and is currently working to maximize synergies between its extensive expertise in the area of adhesive design and the Seiko PMC Group’s business foundation. By swiftly supplying high-grade adhesives, including through the sale of environment-friendly solvent-free products, we will endeavor to play a key role in realizing the Seiko PMC Group’s corporate vision, as well as in expanding its overseas operations in line with its new medium-term management plan.
In line with its goal of expanding its overseas operations under its New Stage 2021 medium-term management plan, Seiko PMC is in the process of establishing a local subsidiary to manufacture and sell papermaking chemicals in Vietnam. Economic growth is expected to continue to drive increased production of paper and paperboard in Association of Southeast Asian Nations (ASEAN) member countries, notably Vietnam. Seiko PMC looks forward to contributing to the growth of the papermaking industry in these markets by ensuring its ability to supply high-grade papermaking chemicals in a timely manner.