Preventing Global Warming(2017)
Principal Initiatives in Fiscal Year 2017
01Setting a Medium-Term Target for the Reduction of CO₂ Emissions
The DIC Group has declared “low carbonization” as a key theme of it sustainability program and is working to reduce energy consumed by its businesses, as well as to advance the use of energy from renewable sources by, among others, adopting biomass fuel, introducing solar and wind power, and purchasing low-carbon electric power.
In October 2016, the Sustainability Committee set a medium-term target for reducing the DIC Group’s absolute emissions of CO₂ by 7.0% from the fiscal year 2013 level by fiscal year 2020. To this end, the Group has added promoting the use of electric power generated from renewable energy, including by biomass boilers and solar power systems, as well as the purchase of low-carbon electric power, to core initiatives implemented in line with this target. In its next medium-term management plan, formulation of which is currently in progress, the Group will set a target for beyond fiscal year 2020.
02Energy Consumption and CO₂ Emissions by the Global DIC Group
Despite a 1.1% increase in production volume in fiscal year 2017, energy consumption by DIC Group companies worldwide decreased 2.9%, to 11,054,000 GJ, from 11,379,000 GJ in fiscal year 2016, while global CO₂ emissions declined 3.7%, to 634,741 metric tonnes, from 659,378 metric tonnes. The DIC Group’s diverse product portfolio encompasses printing inks, polymers, pigments, LCs, engineering plastics and compounds. Recent years have seen an uptrend in the output of energy-intensive fine chemicals and a downtrend in the output of items the production of which is comparatively energy efficient. Against this backdrop, the Group’s success in achieving a reduction in the volume of CO₂ emitted worldwide that exceeded its target for the year was due in large part to the decisive implementation of energysaving and carbon-reduction initiatives.
CO₂ emissions per unit of production in fiscal year 2017, expressed in terms of kilograms of CO₂ per metric tonne of production, fell 4.7%, to 296.0 kg CO₂ /metric tonne, from 311.0 kg CO₂ /metric tonne in the previous period, a decline of 9.5% from fiscal year 2013, the Group’s current base year. Going forward, the Group will continue to take steps to reduce energy consumption, including promoting the installation of energy-efficient equipment, improving production processes and increasing facility operating rates, as well as to further advance the use of renewable energy by shifting to clean fuels and furthering its use of solar power.
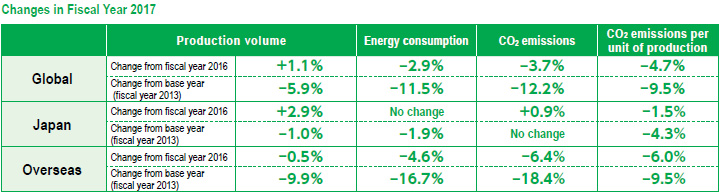
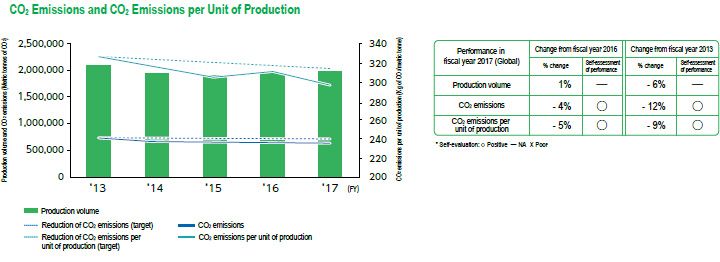
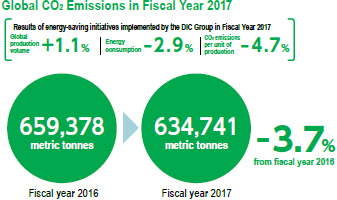
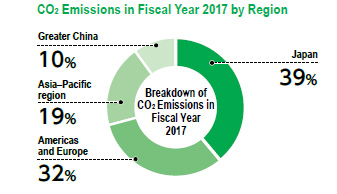
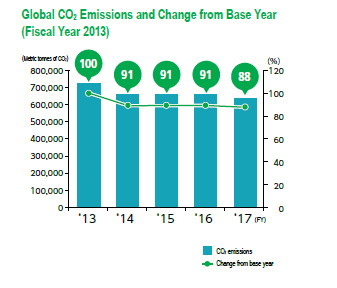
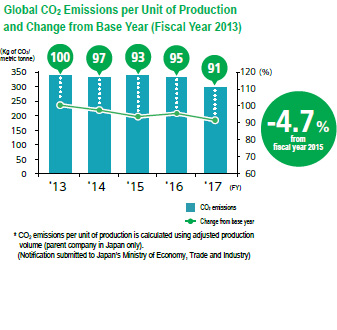
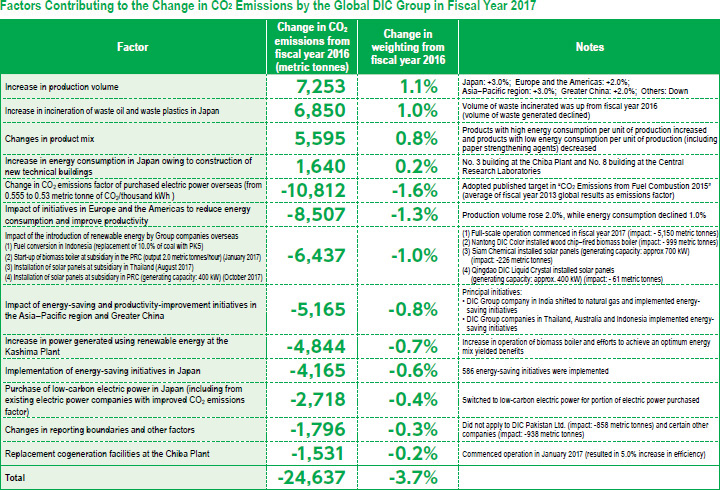
03Energy Consumption and CO₂ Emissions by the DIC Group in Japan
In fiscal year 2017, production volume by the DIC Group in Japan—the 52 sites operated by DIC and domestic Group companies—rose 2.9%. Although energy consumption remained level at 4,314,000 GJ, energy consumption per unit of production—the indicator specified in Japan’s Act on the Rational Use of Energy—declined 2.4%, to 3.914 GJ/metric tonne, from 4.010 GJ/metric tonne in the previous fiscal year. Similarly, while CO₂ emissions rose 0.9%, to 244,395 metric tonnes, from 242,194 metric tonnes in fiscal year 2016, CO₂ emissions per unit of production declined 1.5%, to 222.0 kg CO₂ /metric tonne, from 225.0 kg CO₂ /metric tonne in fiscal year 2016. CO₂ emissions were pushed up by increases in the output of energy-intensive fine chemicals and the volume of waste incinerated. These factors were countered by higher operating rates for renewable energy facilities (biomass boiler and wind and solar power facilities) and the positive impact of an appropriate balance of renewable energy sources, including a 1,700 kW–capacity cogeneration system, at the Kashima Plant. Other causes included the replacement of the Chiba Plant’s cogeneration system with a new system with a generating capacity of 3,375 kW and 8.0 metric tonnes of steam/hour and the implementation of 586 energy-saving initiatives at production sites, which underpinned improvements in both energy consumption per unit of production and CO₂ emissions per unit of production.
Regarding CO₂ emissions in the supply chain, DIC reports data for six of the 15 categories of Scope 3*, including “capital goods,” “waste generated in operations” and “business travel.” Third-party verification is obtained for “waste generated in operations.”
- Scope3:emissions are indirect emissions from production, transport, shipment, commuting and other activities in the supply chain.
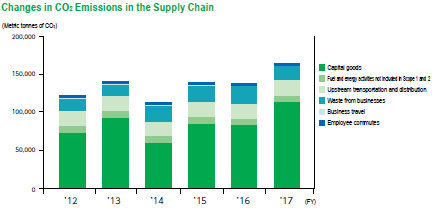
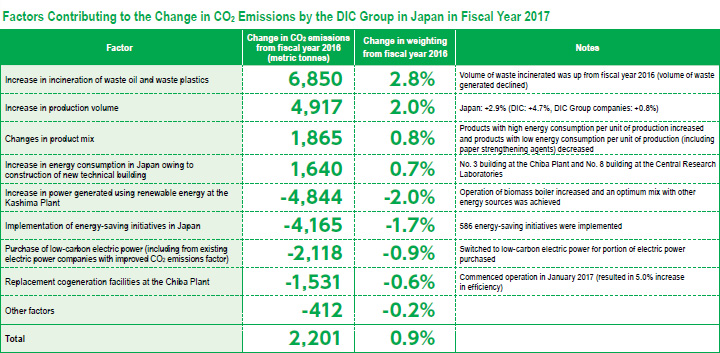
04Energy-Saving Initiatives by the DIC Group in Japan
DIC Group sites (plants and R&D facilities) in Japan endeavor to conserve energy by promoting the following initiatives, which target the reduction of base load energy consumption, and by applying the PDCA cycle to improve the efficiency of production methods—thereby reducing energy used—and shorten process times. In fiscal year 2017, sites also began promoting carbon-reduction initiatives.
- Employed highly efficient lighting and air conditioning measures to eliminate waste
- Introduced energy-saving controls on pumps and blowers
- Used more efficient compressors and implemented measures to reduce pressure losses
- Implemented measures to improve the power factors of electric equipment
- Adopted high coefficient of performance (COP) chillers and promoted measures to prevent cold and hot water supply waste
- Reduced use of boiler fuel, among others, through the recovery of waste heat
- Ensured appropriate warming times and temperatures for raw materials
- Actively promoted the use of energy from renewable sources, including solar power and power generated by biomass boilers, at suitable sites
- Actively promoted the use of energy from low-carbon sources at suitable sites
- Increased power generated using renewable energy at the Kashima Plant
- Implemented 586 energy-saving initiatives at domestic production sites
- Purchased low-carbon power (including from existing electric power companies with improved CO₂ emissions factors)
- Replaced cogeneration facilities at the Chiba Plant
In fiscal year 2017, these initiatives reduced energy consumption by approximately 233,000 GJ. This corresponds to approximately 30,000 200-liter drums of crude oil, or 5.4% of total energy consumed by the DIC Group in Japan during the period. Going forward, the Group will continue working to reduce its consumption of energy, and also share best practices among sites with the aim of discovering new themes. In addition, the Group will reinforce operating manuals for key energy-consuming equipment, including boilers, chillers and compressors, to optimize performance, as well as expand the deployment of initiatives developed in Japan at overseas sites.
Key DIC Group Energy-Saving Initiatives in Japan in Fiscal Year 2017 (Total Number of Initiatives Implemented: 586)
Production facility | Energy-saving initiative | Reduction in annual energy consumption(GJ) | Reduction in CO₂ emissions (metric tonnes) |
---|---|---|---|
Chiba Plant | Reduced amount of steam used by improving base load of polymer production line | 883 | 53 |
Chiba Plant | Changed heating method for glycerin (raw material) tanks | 670 | 40 |
Chiba Plant | Reduced energy used by replacing substandard steam traps (after analysis of traps) | 798 | 48 |
Chiba Plant | Replaced water and heating medium pumps; new pumps stop when reaction ceases | 3,172 | 155 |
Chiba Plant | Switched to LED lighting | 1,126 | 55 |
Chiba Plant | Other energy-saving initiatives at the Chiba Plant | 10,744 | 548 |
Kashima Plant | Implemented initiatives aimed at reducing energy intensity of production processes for pigments | 1,535 | 78 |
Kashima Plant | Implemented initiatives aimed at reducing energy intensity of production processes for functional products/additives | 695 | 35 |
Kashima Plant | Reduced heat used by improving dehydration, washing and heat treatment processes for engineering plastics | 6,488 | 327 |
Kashima Plant | Reduced power and steam losses, improved operation of mixer used in wastewater treatment and switched to LED lighting | 772 | 39 |
Kashima Plant | Other energy-saving initiatives at the Kashima Plant | 186 | 10 |
Sakai Plant | Installed heater box | 699 | 37 |
Sakai Plant | Adjusted amount of water used in hot water washing | 467 | 24 |
Sakai Plant | Reduced electric power consumption by installing systems for improving the efficiency of power use on B and D substations | 1,240 | 365 |
Sakai Plant | Reduced fuel consumption by improving dryness of steam in flue boiler | 1,194 | 63 |
Sakai Plant | Upgraded from gas turbine to EHP air conditioning system in technical building | 4,908 | 257 |
Sakai Plant | Other energy-saving initiatives at the Sakai Plant | 3,833 | 200 |
Hokuriku Plant | Reduced base load during production on SH production floor | 941 | 52 |
Hokuriku Plant | Modified operation of circulation pumps and steam traps, and implemented other initiatives on J production floor | 1,482 | 91 |
Hokuriku Plant | Shortened production processes, improved heating chamber and implemented other initiatives on E production floor | 511 | 31 |
Hokuriku Plant | Improved steam traps, and switched to LED lighting, among others, on GLM production floor | 504 | 32 |
Hokuriku Plant | Improved operation of wastewater mixer and well pump, and replaced transformer on utility floor | 991 | 63 |
Yokkaichi Plant | Switched to E-series FCP centrifugal pump | 397 | 20 |
Yokkaichi Plant | Switched to use of a single brining refrigerator | 1,159 | 59 |
Yokkaichi Plant | Standardized waste heat recovery method | 278 | 14 |
Yokkaichi Plant | Reduced steam loss, among others, by installing line valves | 504 | 25 |
Komaki Plant | Reduced energy consumption, among others, by revamping work schedules for DIC Graphics’ employees | 580 | 28 |
Komaki Plant | Revised maintenance of heater temperatures for extruders and drying conditions, among others, for SC production | 3,161 | 155 |
Komaki Plant | Reduced electric power consumption by switching to LED lighting, among others | 476 | 23 |
Komaki Plant | Other energy-saving initiatives at the Komaki Plant | 705 | 34 |
Tatebayashi Plant | Reduced base load, among others, by replacing compressors | 661 | 34 |
Tatebayashi Plant | Reduced electric power consumption by switching to LED lighting, among others | 355 | 18 |
Tatebayashi Plant | Implemented initiatives to reduce energy consumed by SC production processes | 870 | 45 |
Tatebayashi Plant | Other energy-saving initiatives at the Tatebayashi Plant | 680 | 35 |
Tokyo Plant | Reduced electric power consumption by switching to LED lighting, among others | 875 | 45 |
Tokyo Plant | Other energy-saving initiatives at the Tokyo Plan | 385 | 20 |
Gunma Plant | Disconnected unneeded power source for control panels (E plant) | 3,061 | 154 |
Gunma Plant | Modified procedures for operation of nitrogen generator (D plant) | 308 | 16 |
Gunma Plant | Replaced compressors (D plant) | 951 | 48 |
Utsunomiya Plant | Shortened operating times for air compressors and introduced inverters | 1,025 | 55 |
Utsunomiya Plant | Shortened operating times for cooling water, cold water and hot water pumps | 3,501 | 193 |
Utsunomiya Plant | Replaced chillers, turned of air fans for outdoor warehouses and implemented other measures to rationalize production | 2,469 | 141 |
Utsunomiya Plant | Rationalized production by introducing roll-less forming | 1,210 | 70 |
Utsunomiya Plant | Switched from non-explosion proof mercury lighting to LED lighting in printing inks production areas | 1,395 | 72 |
Kansai Plant | Reduced electric power consumption by switching to LED lighting, among others | 522 | 27 |
Kansai Plant | Promoted energy-saving measures at the Kansai Plant and elsewhere | 489 | 25 |
Others | Modified production processes, switched to LED lighting and replaced obsolete equipment with energy-efficient models | 8,912 | 506 |
Total for 5 86 initiatives | 78,768 | 4,165 |
Improving Yields by Expanding Use of System to Enhance the Visibility of Energy Consumption
With the aim of optimizing energy use on an individual facility basis, DIC developed a system that measures, monitors and verifies waste and irregularities in use in real-time, thereby enhancing the visibility of energy consumption. The system—which won the ECCJ Chairman’s Prize at Japan’s 2012 Energy Conservation Grand Prize awards, sponsored by the Energy Conservation Center, Japan (ECCJ)—has been rolled out at DIC sites across Japan. In fiscal year 2014, the system was installed at the Komaki Plant. In addition, a system to enhance visibility that also analyzes energy consumption during different production processes was installed on the V, C and B production floors of the Chiba, Kashima and Sakai plants, respectively, to reproduce optimum yields for materials inputs. In fiscal year 2016, DIC installed a more advanced version of the system at the Yokkaichi Plant.
Reducing Energy Consumption and Enhancing Product Quality through Kaizen Skill Improvement Training
Having recognized that enhancing the awareness of employees in production and providing them with the tools to continuously improve their work are crucial to strengthening front-line capabilities, in 2008 DIC began offering the Kaizen Skill Improvement Training Program. This program—which is structured around four themes, namely, reducing energy consumption, increasing yields, enhancing product quality and rationalizing operations—seeks to foster professionals who can identify and resolve issues on their own initiative. Participants spend one year participating in initiatives aimed at improving quality control methods and the following year putting their findings into practice. Each December, achievements are presented at a briefing attended by pertinent plant general managers and executives.
Since 2012, DIC has also offered the Kaizen Initiative Instructor Training program, designed to equip employees who have completed the Kaizen Skill Improvement Training program with the leadership and educational skills necessary to serve as instructors for the program. As of the end of fiscal year 2017, a cumulative total of 450 employees from pertinent DIC sites in Japan had completed Kaizen training, with approximately 15%, or one in seven, subsequently going on to earn accreditation as program instructors, adding momentum to energy-saving and other initiatives.
TOPICS
Horizontal Deployment and Further Strengthening of Energy-Saving Promotion Working Groups
In Japan, leaders of domestic site Utility Control Groups, which oversee energy and water supplies and wastewater treatment, hold quarterly Utility Control Liaison Working Group conferences. A central focus of conferences is Energy-Saving Promotion working groups. Here, Utility Control Group managers are joined by representatives of the Production Management Department, who are currently assisting with efforts to prepare a manual outlining key energy-saving measures, compile best practice case studies, discover and test new methods for reducing energy consumption, consider the use of renewable energy as a way to reduce carbon, and conduct energy-saving analyses at sites nationwide.
The Energy-Saving Promotion Manual sets forth measures for, among others, enhancing the visibility of energy consumption, the framework for promoting energy-saving initiatives, procedures for formulating energy-saving plans, creating energy management standards, approaches to benchmarks for gauging energy performance and to investments in energy-saving initiatives, and use of the PDCA cycle to measure the progress of initiatives. The manual is distributed for use across the domestic DIC Group. Energy-saving analysis begins with comparing initiatives against the manual, creating a numerical expression of findings and plotting the results on a radar chart. Subsequent steps are to formulate proposals for addressing weaknesses identified through this process, implement remedial measures and follow up on results. Efforts to formulate proposals are not limited to individuals directly responsible, but also include pertinent department and plant general managers. For the foreseeable future, DIC will continue to use these energy-saving analysis activities to raise the level of efforts at sites nationwide, in addition to which it will add risk management–based BCP to the list of assessment criteria used and begin deployment at overseas Group production facilities.
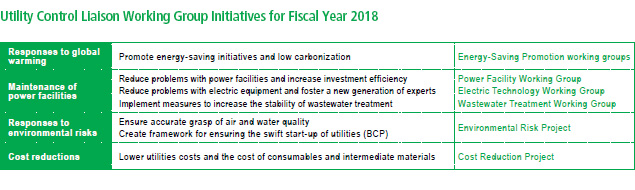
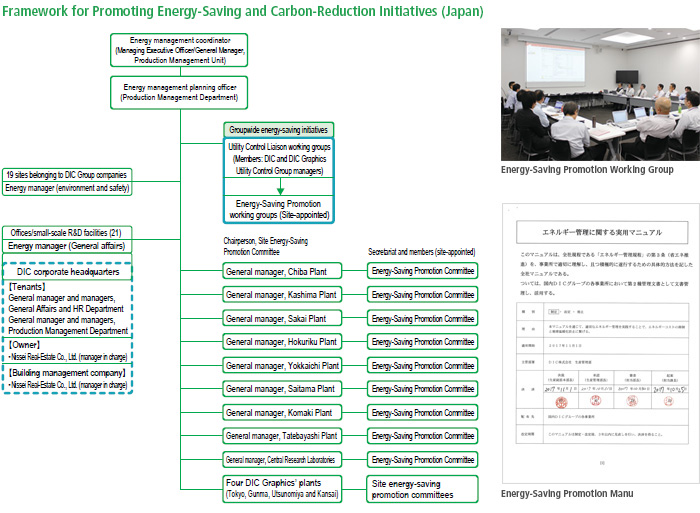
【Energy-Saving Analysis and Response】
Thermal Imaging Leak Detection and Elimination of Heat Loss
Boiler steam valves and other fittings are often not insulated, as a consequence of which heat escapes. DIC used infrared energy (thermal) imaging to accurately locate leaks and made use of removable insulating jackets to prevent the loss of heat energy.
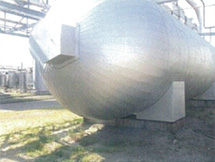
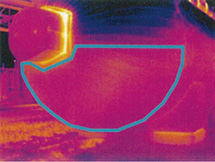
【Energy-Saving Analysis】 Enhancing the Visibility of Strengths/Weaknesses and Formulating Proposals for Remedial Measures
Working group teams were dispatched to sites to conduct energy-saving analyses and findings were plotted on radar charts to enhance visibility and provide hints for remedial measures. Working group members formulate proposals tailored to site needs, based on which remedial measures are implemented, many of which are later selected as best practice case studies and deployed Groupwide.
VOICE
Actions that are a matter of course at one facility can be advanced techniques suitable for deployment at another.
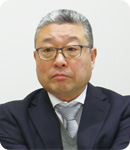
In visiting various production facilities to conduct energy-saving analyses, I have found that actions that are a matter of course at one site may be unheard of at other facilities. The purpose of energy-saving analysis activities is not to find fault, but rather to discover new ideas and gather hints. I view them as treasure hunts. The horizontal deployment of such actions can help reduce energy consumption, costs and risks, so the motivation for working group members is high. Each of our production facilities has a Utility Control Group, which is responsible for energy management. While influential, these entities have traditionally been somewhat underappreciated. However, thanks to the efforts of the Energy-Saving Promotion working groups the presence of Utility Control groups has increased across the Group. I am confident that their efforts will also contribute to efforts to curb global warming at overseas production facilities in the years ahead.
Energy Manager, Production Management Department
Satoshi Abe
05Reducing Fossil Fuel Use By Promoting the Introduction of Renewable Energy
Most of the energy from renewable sources used by DIC Group companies in Japan is natural energy generated using a biomass boiler and wind and solar power facilities at the Kashima Plant. In fiscal year 2017, such energy represented 10.3% of total energy (steam and electric power) consumption by these companies, amounting to 497,000 GJ (equivalent to 12,818 kl of crude oil), an increase of 21.0% from fiscal year 2016. The increase in renewable energy from the previous year was attributable to the stable operation of the Kashima Plant’s biomass boiler and the success of efforts to achieve an optimal mix of power sources (biomass boiler, wind power, solar power, a cogeneration system and purchased electric power). Going forward, the Group will continue to actively promote the use of renewable energy as an effective way to reduce its CO₂ emissions.
Boosting Renewable Energy to 10.3% of Total Energy Consumption in Japan
In Japan, the DIC Group actively promotes the use of energy from renewable sources at suitable sites. The biomass boiler at the Kashima Plant (generating capacity: 4,000 kW and 30.0 metric tonnes of steam/hour) contributes significantly to this effort. DIC focuses on improving the quality of wood chips used as boiler fuel, which influences operating rates, as well as on enhancing maintenance procedures. By combining this boiler with two wind power generation facilities (each with a generating capacity of 2,300 kW) and a solar power generation system (100 kW), the Group aims to achieve an optimal power mix of purchased electric power, electric power produced through cogeneration systems and electric power generated using renewable energy. Thanks to these and other efforts, in fiscal year 2017 DIC Group companies in Japan used 497,000 GJ of energy from renewable sources, accounting for 10.3% of total energy consumption by these companies. As a consequence, the positive impact of the use of renewable energy was 30,791 metric tonnes.
At the Kashima Plant, DIC commenced operation of a newly installed megasolar power system with a generating capacity of 1,600 kW (comprising 5,588 278-watt solar panels with a surface area of 13,772 m²) in January 2018. The same month, certain liquefied natural gas (LNG) boilers at the Hokuriku Plant, which produces synthetic resins, were replaced with a wood chip biomass boiler. As a consequence, the plant’s CO₂ emissions in fiscal year 2017 were down approximately 12% from the previous period.
In fiscal year 2017, electric power generated in Japan using cogeneration systems and other independent means amounted to 70,140,000 kW, an increase of 9.0% from fiscal year 2016, representing 25.6% of total energy consumed by the DIC Group in Japan. The Group also embarked on a review of the electric power companies from which it purchases electric power and is taking steps to promote the procurement of green energy by prioritizing companies that supply power with a low CO₂ emissions factor.
06Independent Electric Power Generation through Cogeneration and the Use of Renewable Energy Increased to 23.0% of Total Energy Consumption in Japan
With the aim of increasing energy efficiency, and as a precaution against natural disasters, the DIC Group in Japan is advancing the systematic adoption of cogeneration and the use of renewable energy, that is, energy from sources that are naturally replenished. Cogeneration systems burn fuel to drive turbines, facilitating the production of electric power and the recovery and reuse of waste heat (steam and hot water), thereby improving energy efficiency.
With cogeneration systems already in operation at three domestic plants (Chiba, Saitama and Gunma), in 2015 DIC installed a natural gas turbine–powered cogeneration system with a generating capacity of 1,700 kW at its Kashima Plant. In April 2017, DIC replaced the existing cogeneration system at the Chiba Plant, which had a generating capacity of 5,300 kW, with a new high-efficiency 3,375 kW– capacity system, thereby realizing a volume of independently generated power ideally suited to current needs and reducing energy consumption thanks to an estimated 5.0% increase in efficiency. As a consequence, the maximum generating capacity of the Group’s cogeneration systems in Japan was 14,000 kW. Electric power generated using cogeneration systems in fiscal year 2017 amounted to 44,270,000 kW and represented 16.0% of energy consumed by the Group in Japan during the period, while total independently generated electric power, including that from renewable sources, accounted for 23.0%.
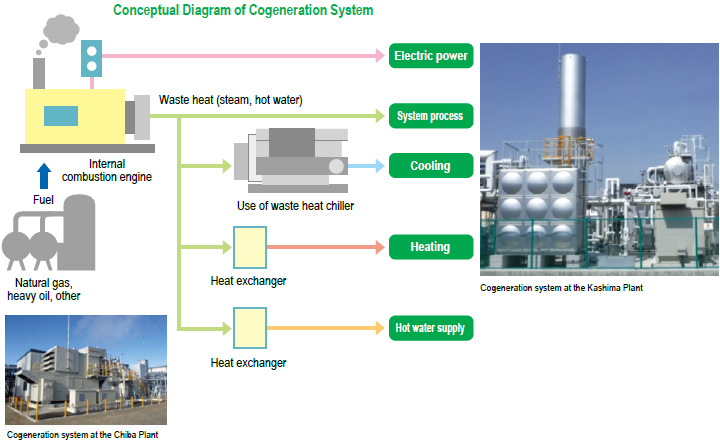
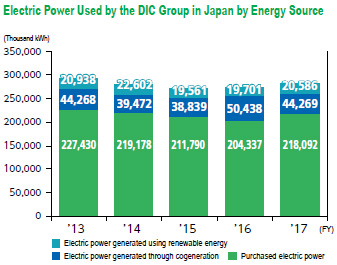
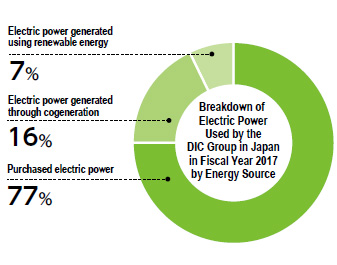
07Energy Consumption and CO₂ Emissions by the DIC Group Overseas
While production volume by overseas DIC Group companies edged down 0.5% in fiscal year 2017, energy consumption by these companies declined 4.6%, to 6,740,000 GJ, from 7,065,000 GJ in fiscal year 2016 and energy consumption per unit of production slipped 4.1%, to 6.469 GJ/metric tonne, from 6.746 GJ/metric tonne. CO₂ emissions decreased 6.4%, to 390,346 metric tonnes, from 417,184 metric tonnes in the previous period, and CO₂ emissions per unit of production declined 6.0%, to 374.6 kg CO₂/metric tonne, from 398.4 kg CO₂/metric tonne. Factors contributing to the decline in CO₂ emissions in fiscal year 2017 include efforts by individual Group companies to break down the Group’s emissions reduction targets and promote energy conservation and carbon-reduction initiatives, the installation of a biomass boiler at Hainan DIC Microalgae Co., Ltd., and a solar power system at Qingdao DIC Finechemicals Co., Ltd., in the PRC; in the Asia–Pacific region, the replacement of a portion of the coal used to fire boilers with palm kernel shells (PKS) at the Karawang Plant of PT. DIC Graphics; and in Europe and the Americas, the installation of additional solar power systems and further initiatives aimed at improving production efficiency.
Promoting Energy Savings Overseas
Laws and regulations, as well as infrastructure, differ between countries and regions. The DIC Group strives to promote energy savings and efficient operations wherever it is active and in so doing sets precedents for the global chemicals industry.
DIC Group companies overseas continue to implement a broad range of energy-saving initiatives, including improving production efficiency, reducing base load energy consumption, choosing high-efficiency models when replacing equipment and switching to LED lighting. As previously described, the Group is also promoting the use of energy from renewable sources and has several new projects currently under consideration for implementation in fiscal year 2018 and beyond. Efforts in fiscal year 2018 will center on installing solar power systems in regions with high-efficiency electric power generation and increasing the portion of coal it replaces with PKS. Looking ahead, DIC and DIC Group companies overseas will step up cooperation with the aim of contributing further to efforts to curb global warming.
Energy-Saving Initiatives at Overseas Group Companies
Asia–Pacific Region
The DIC Group has 23 sites in the Asia–Pacific region, which account for around 19.0% of the Group’s total global CO₂ emissions. Despite a 3.0% increase in production volume by Group companies in the region, CO₂ emissions in the region declined 6.0% in fiscal year 2017. Principal factors behind this decrease included an increase in the fuel conversion rate (replacement of 10.0% of coal used with biomass) and the implementation of an energy-saving project at a pigments production facility in Indonesia, the promotion of fuel conversion (transition from diesel to natural gas) and energy-saving initiatives at a printing inks production facility in India, and the implementation of energy-saving initiatives at a solid compounds production facility in Indonesia and a printing inks production facility in Australia. While production volume in the region in fiscal year 2017 was up 16.0% from the fiscal year 2013 base year, CO₂ emissions were held to a 6.0% increase.
A regional ESH country head meeting is held annually at the office of DIC Asia Pacific in Singapore, with participants including country heads, the executive in charge of regional operations and pertinent individuals from the Responsible Care Department and the Production Management Department. The principal purpose of the meeting is to explain safety and environmental policies and discuss and agree on concrete action plans for the region in the subsequent fiscal year. In fiscal year 2017, this included providing an explanation of the Group’s policies for combating global warming (reducing energy consumption and carbon) in fiscal year 2018 and determining action plans. As part of its efforts to ensure achievement of the CO₂ emissions reduction target set for the global DIC Group, corporate headquarters assists local Group companies by formulating and implementing energysaving plans; promoting ongoing energy-saving analysis activities to support the identification of energy-saving themes and the implementation of remedial measures; deploying a practical energy management manual and best practice case study materials (establishing management practices and promoting horizontal deployment will remain targets for the foreseeable future); and launching and providing support for energy-saving and carbon-reduction projects at suitable sites.
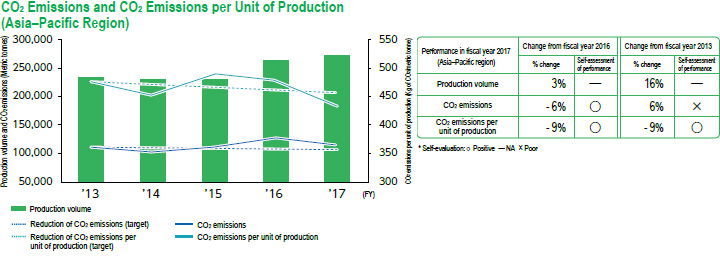
Greater China
The DIC Group’s 18 sites in Greater China, which include R&D facilities, account for approximately 10% of the Group’s total CO₂ emissions. While production volume in fiscal year 2017 was up 2.0%, CO₂ emissions across the region were down 3.0%. Among factors contributing to this decline were the installation of a biomass boiler at Hainan DIC Microalgae, which produces Spirulina, and a solar power system with a generating capacity of 400 kW at Qingdao DIC Finechemicals, and the implementation of energy-saving initiatives at Zhongshan DIC Colour Co., Ltd. Compared with the fiscal year 2013 base year, production volume in Greater China in fiscal year 2017 was up 1.0%, while CO₂ emissions rose 16.0%. The increase in CO₂ emissions primarily reflected expanded production of energy-intensive products, including LCs, in recent years; an increase in base load energy consumption attributable to the expansion of research facilities, increased operating rates for clean rooms and other factors not related to production, as well as to the start of operations at a new production facility for engineering plastics.
Once annually, regional energy officers and ESH officers hold a joint ESH conference that is also attended by the executive in charge of regional operations and pertinent individuals from the Responsible Care Department and the Production Management Department. In fiscal year 2017, the conference was held in November in Taipei. The environmental portion of the event included providing an explanation of the Group’s policies for combating global warming (reducing energy consumption and carbon) in fiscal year 2018, setting a target for reducing regional CO₂ emissions and determining action plans. Participating companies also gave presentations introducing case studies and plans for future initiatives. The objective of the conference is to provide information on successful energy management and other energy-saving efforts to help companies enhance their performance. Gatherings have thus had a positive ripple effect, which includes encouraging the deployment measures based on the experiences of other companies.
Other regional efforts include promoting energy-saving analysis activities to gauge the status of energy management and the performance of energy-related equipment. As part of these efforts, local employees known as energy-saving masters assess energy-saving promotion frameworks, actual energy consumption, efforts to formulate policies and manage goals, and the performances of key equipment. Findings are plotted on a radar chart to identify strengths and weaknesses and encourage remedial measures.
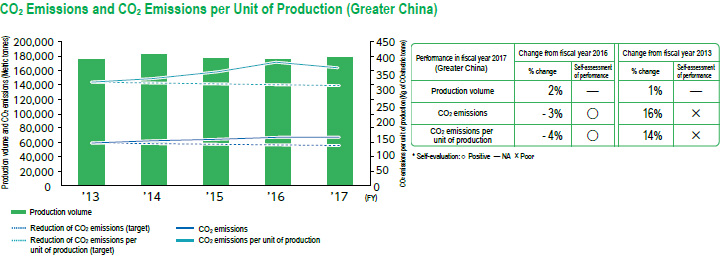
Expansion of the Use of Renewable Energy at Sites in the Asia–Pacific Region and Greater China
Achieving a decarbonization of the global economy has become a central focus worldwide. Against this backdrop, the use of energy from renewable sources has increased across the Asia–Pacific region and Greater China, as elsewhere. DIC Group sites in these regions are making use of government subsidies and support to expand their use of renewable energy by, among others, installing biomass boilers and solar power systems.
PKS to be used as fuel(Indonesia)
PKS to be used as fuel
PT. DIC Graphics’ Karawang Plant is a crucial facility for the production of pigments for inks and coatings for packaging applications, plastics and other applications, the production of which uses a significant amount of energy for boilers and water for washing. To date, the facility has primarily used coal, the combustion of which is extremely economical (approximately 1/5 the cost of heavy oil and 1/3 the cost of natural gas) and easy to obtain in Indonesia. Because the Karawang Plant accounts for a tenth of the DIC Group’s global CO₂ emissions, and because its production volume continues to expand, reducing the facility’s energy consumption and finding low-carbon energy sources is a critical challenge. To this end, the plant kicked off a CO₂ emissions reduction project focused on exploring low-carbon alternatives to coal that identified PKS. Because Indonesia is the world’s second-largest producer of palm oil, PKS—which are left after the extraction of oil—are easy to secure in large quantities. Japan imports PKS for use as fuel for coal-fired electric power production facilities and biomass boilers.Having determined that the calorific value of PKS, approximately 5,000 kCal/kg, is comparable to that of coal used at the plant, in December 2016 the project team began conducting combustion tests using a mixture of coal and pulverized PKS in various ratios, as a result of which it determined that approximately 20% of the coal could be replaced with PKS with no impact on boiler operation or combustion or on incinerated ash, which is used as an aggregate in cement.
In January 2017, the Karawang Plant began replacing approximately 10% of the coal it used with KPS. As a consequence, despite a 1.3% increase in production at the plant in fiscal year 2017, its CO₂ emissions declined 8.5%. In other words, thanks to introducing PKS on a trial basis, the plant realized a decrease of 5,000 metric tonnes in its annual CO₂ emissions. This reduction was equivalent to 0.8% of CO₂ emissions by the global DIC Group in fiscal year 2016. Beginning in fiscal year 2018, the plant will increase the proportion of PKS in its fuel mix to around 20%.
Siam Chemical Industry (Thailand)
Installation of Solar Panels Reduces CO₂ Emissions
Siam Chemical Industry, which manufactures a broad range of polymer products, including synthetic resins, continues to see rising demand for acrylic coating resins, underpinned by increases in automobile production. Thailand is seeking to diversify energy sources to reduce the country’s dependence on natural gas to generate electric power. Energy from renewable sources is attracting considerable attention thanks to tax breaks offered by the Thai government. Against this backdrop, Siam Chemical Industry installed solar panels with a total generating capacity of 704 kW (annual output: 1,049 MWh) on the roofs of production buildings and warehouses at its plant in Samut Prakan Province. The solar panels commenced operation in July 2017. Electric power generated using these facilities is used on production lines and in offices. In fiscal year 2017, solar power accounted for 16.0% of the electric power used by the plant, lowering the plant’s annual CO₂ emissions by 580 metric tonnes.
Hainan DIC Microalgae (PRC)
Biomass Boiler Replaces Diesel-Fired Unit
Hainan DIC Microalgae, DIC Lifetec Co., Ltd.’s production base in the PRC, cultivates Spirulina, an edible blue–green algae that is attracting attention as a superfood, which it processes into nutritional supplements and natural food colorings. Until recently, the facility used a diesel-fired boiler to produce the steam necessary for its production processes, but in October 2016 it switched to a biomass boiler that uses waste rubber tree wood from the thinning of rubber forests as fuel. The new boiler was in operation for the duration of fiscal year 2017, resulting in a reduction of 1,000 metric tonnes in the facility’s CO₂ emissions for the year, equivalent to 40.0% of its emissions in the previous year. This also accounted for 1.5% of the overall decrease in CO₂ emissions achieved by the DIC Group in Greater China in fiscal year 2017.
Qingdao DIC Finechemicals (PRC)
Solar Power System Installation Helps Reduce Energy Consumption and CO₂ Emissions
Recognizing the monsoon climate, abundant sunshine and excellent atmospheric conditions of Qingdao as suited to solar power generation, subsidiary Qingdao DIC Finechemicals, a manufacturer of base materials for TFT LCs, which it supplies to local customers, installed a solar power system that features panels on the roof of the company’s plant building. The new system, which has a generating capacity of 440 kW, began operating in September 2017. With this installation, Qingdao DIC Finechemicals’ annual output of solar power is expected to reach 480 MWh, reducing its annual CO₂ emissions by approximately 8.5% from the fiscal year 2016 level.
Planned and Ongoing Efforts to Update Facilities and Modify Production Processes
Efforts to Optimize Equipment Contribute to a Significant Reduction of Refrigerator Power Consumption (DIC Synthetic Resins (Zhongshan))
Refrigerators account for a third of the electric power consumed by DIC Synthetic Resins (Zhongshan) Co., Ltd.’s metal carboxylates plant. This is primarily because cooling water is supplied by remote motors and water supply pumps, and the pumps operate at full capacity when refrigerators are running. To bolster efficiency, in May 2015 the company launched a project to review processes and equipment and explore potential improvements. This resulted in the installation of a cooling tower and water pump near refrigerators to recirculate cooling water. The company also identified a way to link refrigerator compressors with ice water pumps, facilitating the automatic adjustment of water temperature. Full-scale operations with the new setup commenced in January 2016. This has succeeded in reducing annual refrigerator power consumption to approximately 120,000 kWh, from around 320,000 kWh prior to optimization.
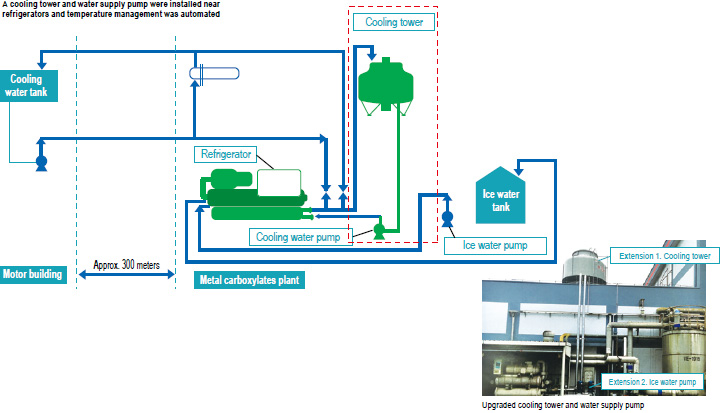
Efforts Succeed in Harnessing Residual Heat from Incinerating Waste Resin Varnish Factory (Nantong DIC Color)
Nantong DIC Color Co., Ltd., incinerates waste resin varnish internally. The temperature of waste gas from this process reaches between 700ºC and 800ºC. The facility installed a heat exchanger to recycle this heat for showers and hot water in pigment manufacturing processes. This move has cut the facility’s annual electric power bill by around Rmb168,000.
VOICE
A key theme is promoting investment in decarbonization with a view to future social change and risk.
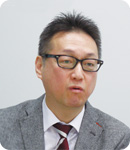
The adoption of the Paris Agreement in 2015 further accelerated the efforts of developed economies to curb their CO₂ emissions. Efforts of particular note include the creation of preferential tax systems and subsidies with the aim of supporting efforts to make use of energy from renewable sources, encouraging companies to diversify energy sources by moving away from fossil fuels (thereby reducing carbon) and avoiding the risk of resource depletion. Indonesia has become the first country in Asia to sell green bonds to raise funds for investments in global warming countermeasures and environmental projects. Such moves will in no small way influence the plans of companies to update their facilities. For example, when looking to replace a key piece of equipment such as a boiler, companies must scrutinize not only performance and cost but also environmental considerations, investment recovery period and the availability of government subsidies, as well as anticipate changes that will take place in society over the useful life of the unit, in determining the timing of the change and selecting the most appropriate model.
When my colleagues and I visit production sites in Indonesia for energy-saving analysis activities or energy-saving promotion conferences, we discuss such issues with local executives. Today, the risk of not making environmental investments is rapidly becoming greater than the risk of being unable to recover such investments. Accordingly, taking steps to become a company that helps to advance decarbonization before regulations are tightened is crucial if we are to continue growing together with society. Going forward, we will step up efforts to share energy conservation and management expertise from Japan, as well as best practice case studies, with overseas Group companies.
Manager in Charge of Efficiency, Production Management Department
Kazuo Kawaguchi
Europe and the Americas
The DIC Group has 113 sites in Europe and the Americas (this category also includes sites in Africa), which account for around 32.0% of the Group’s total CO₂ emissions. Despite a 2.0% increase in production volume in fiscal year 2017, CO₂ emissions across the region were down 3.0%. This decline reflected multiple factors, notably the further integration of production facilities and execution of measures to raise production efficiency, the installation of solar panels and the implementation of other energy-saving and cost-cutting initiatives. Although regional production volume in fiscal year 2017 was essentially level with the fiscal year 2013 base year, CO₂ emissions were down 24.0%, with key contributing factors including a significant increase in production efficiency realized through a large-scale business reorganization, the use of outsourcing, including the contracting of energy-efficiency consultants to advance the reduction of energy consumption, and active efforts to promote the use of energy from renewable sources, including solar power, small hydroelectric power and landfill biogas.
Sun Chemical Group (United States)
Efforts to Promote the Use of Renewable Energy Stepped Up
Sun Chemical signed a solar power purchase agreement (PPA) with Onyx Renewable Partners and installed a solar power system comprising more than 2,500 panels on the roof of the parking structure at its research facility in Carlstadt, California. Under the 20-year PPA, Onyx will own and maintain the system, which has a generating capacity of 916 kW. Sun Chemical will purchase power generated by the system at approximately 50% of the market rate, thereby helping to reduce energy costs. Installation of the panels began in the fall of 2017 and was completed in January 2018. The system came on line in March 2018.
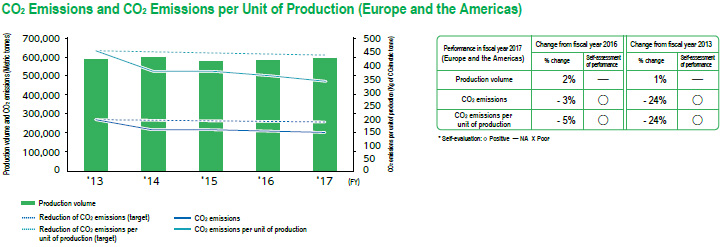
Sun Chemical Group (Austria)
Site Wins the Energy Globe Award Lower Austria in the “Water” Category
Benda-Lutz Werke GmbH, the Sun Chemical Group’s production site in Nussdorf, Austria, operates two small hydroelectric power facilities along the Traisen River. These two units are part of a consortium of 52 such riverside small hydroelectric power facilities operated with the aim of reducing the local community’s consumption of energy. In 2017, the consortium received the Energy Globe Award Lower Austria in the “Water” category in recognition of its efforts to promote the sustainable use of hydroelectric power. At the award presentation ceremony, Sun Chemical and other consortium members gave a presentation titled “The Ecological, Compatible Usage of Hydrodynamic Power in the Lower Part of the Traisen.” Receiving the Energy Globe Award Lower Austria increases the consortium’s chances of being recommended for the national Energy Globe Award for Austria and the Energy Globe World Award in the Water category.
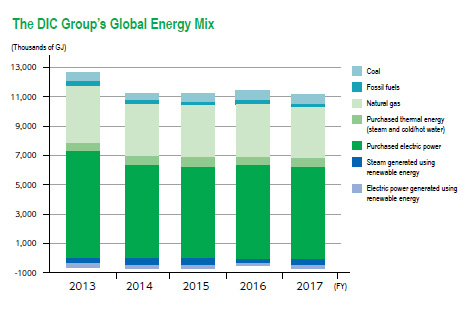
08Initiatives in Areas Other than Production
In fiscal year 2017, DIC once again promoted efforts in Japan in line with the country’s Cool Biz and Warm Biz campaigns, official efforts to reduce electric power consumption by limiting the use of air conditioning in summer and winter through measures such as the introduction of more relaxed office dress codes. The Company also continued to promote initiatives aimed at reinforcing employees’ awareness of the importance of lowering energy consumption, including replacing aging light fixtures and air conditioning equipment with newer, high-efficiency models that satisfy standards set by the ECCJ for its Top Runner program, turning off lights when not needed and implementing mandatory 22º C and 28º C summer air conditioning settings.
09Reporting to the CDP
The CDP (formerly the Carbon Disclosure Project) is a global NPO that works on behalf of institutional investors worldwide to motivate companies to disclose information on initiatives to combat climate change and key environmental data. The CDP analyzes and evaluates information on strategies, greenhouse gas emissions, reduction targets and forecasts, and actual initiatives reported by approximately 6,200 leading global companies participating in its climate change assessment program, including 500 in Japan, and communicates its findings to said institutional investors. DIC has been reporting to the CDP since 2010.
In 2017, DIC was recognized by the organization for reaching the program’s leadership level, receiving high marks for its efforts to reduce its greenhouse gas emissions and its disclosure and earning an overall score of A-, second only to the top score of A, for the second consecutive year. DIC received particularly high marks for its efforts to reduce greenhouse gases attributable to its expanding global production activities and for its disclosure. Cognizant of an increased awareness of risks to global water resources, in 2017 DIC also began participating in the CDP’s water program, which evaluates companies’ efforts to manage such resources.
A total of 73 Japanese companies reached the leadership level in the CDP’s climate change assessment program in 2017, with 13 earning a score of A and 60 a score of A-. A total of six companies in the materials sector earned a score of A-.
Looking Ahead
With the goal of deepening understanding of the importance of energy efficiency across the Group, DIC has inaugurated a number of important new initiatives. In Japan, for example, the Company has created a forum for DIC Group energy officers at principal production facilities to meet regularly. In fiscal year 2018, the efforts of working groups will be guided by four central themes: advance and establish energy-saving initiatives based on the energy conservation manual; promote decarbonization by actively encouraging the use of renewable energy; search for and verify new methods of reducing energy consumption (e.g., small hydroelectric power, binary power and geothermal energy); and conduct energysaving analyses at sites to identify new measures of reducing energy consumption and support use of the PDCA cycle. The progress of these initiatives will be confirmed at quarterly working group meetings. Through initiatives implemented in line with these themes, the Group will probe deeper into issues of concern to society and foster experts in key areas to further reinforce responsiveness Groupwide.
VOICE
To reduce carbon, we will expand from a Group-specific to a region-focused and global-scale approach.
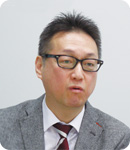
Overseas sites account for approximately 60% of the DIC Group’s global CO₂ emissions. With production in the Asia–Pacific region and Greater China continuing to expand, we face increasing calls to further improve production efficiency and realize an optimum energy balance. Against this backdrop, our ability to reduce carbon increasingly depends on taking a strategic perspective to investment in facilities and energy-saving initiatives. Going forward, we will continue to promote the horizontal deployment of best practice case studies. We will also expand to a region-focused and global-scale approach by stepping up collaboration with other departments and making full use of available human, organizational and administrative resources, including government subsidies and external experts, with the aim of ensuring a solid reputation as a leading global manufacturer of fine chemicals.
General Manager, Production Management Department
Yuuichi Kougo
Back number
- Principal Initiatives in Fiscal Year 2021
- Principal Initiatives in Fiscal Year 2020
- Principal Initiatives in Fiscal Year 2019
- Principal Initiatives in Fiscal Year 2018
- Principal Initiatives in Fiscal Year 2017
- Principal Initiatives in Fiscal Year 2016
- Principal Initiatives in Fiscal Year 2015
- Principal Initiatives in Fiscal Year 2014
- Principal Initiatives in Fiscal Year 2013